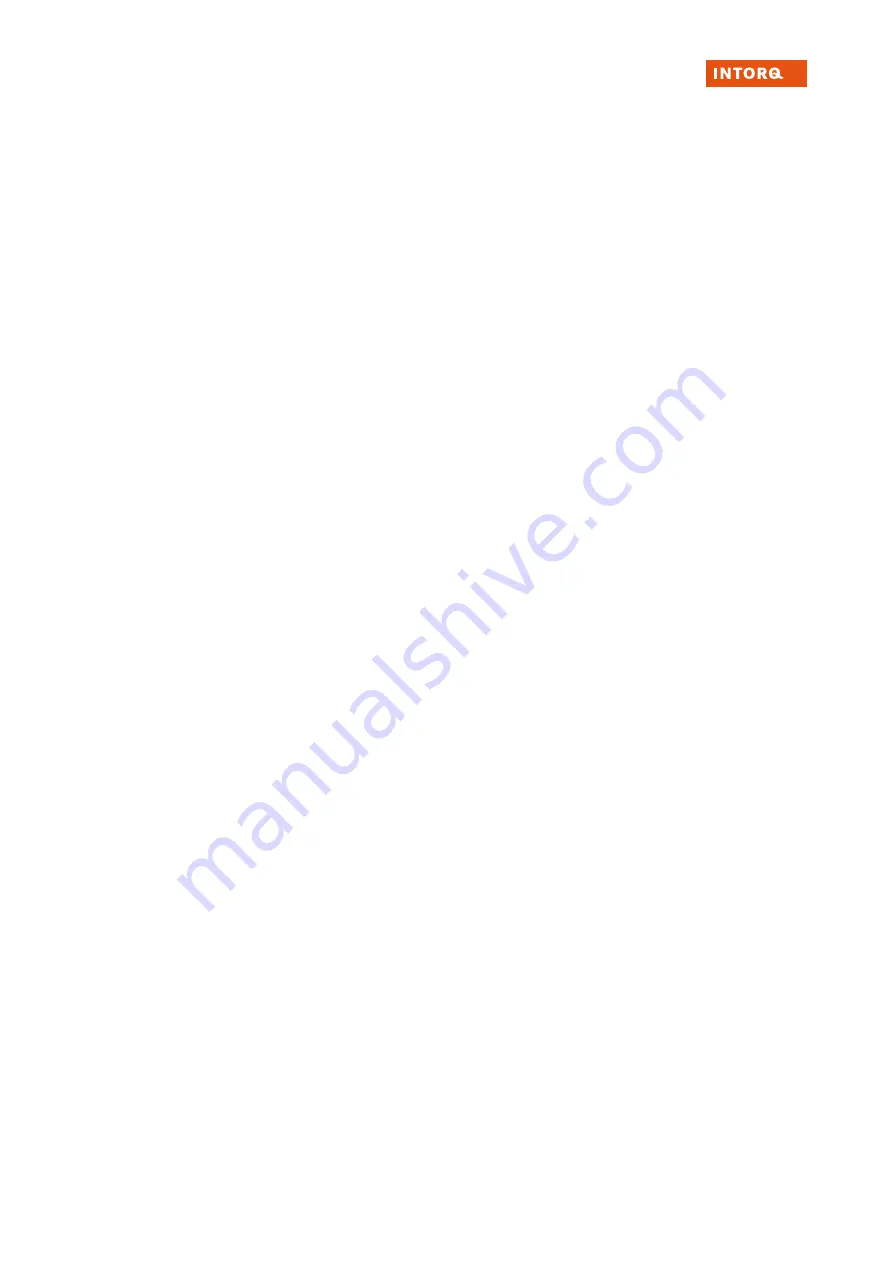
Product description
INTORQ | BA 14.0222 | 06/2020
11
3.3
Function
This brake is an electrically releasable spring-applied brake with a rotating brake disk (rotor) that is
equipped on both sides with friction linings. In its de-energized state, the rotor is clamped with spring force
applied by pressure springs between the armature plate and a counter friction surface. This corresponds
to a fail-safe functionality.
The brake torque applied to the rotor is transferred to the input shaft via a hub that has axial gear teeth.
The brake can be used as a holding brake and for emergency stops.
The friction linings designed to be used in servo drives ensure a safe braking torque.
To release the brake, the armature plate is released electromagnetically from the rotor. The rotor, shifted
axially and balanced by the spring force, can rotate freely.
3.4
Braking and release
During the braking procedure, the pressure springs use the armature plate to press the rotor (which can
be shifted axially on the hub) against the friction surface. The friction linings ensure high braking torque
and low wear. The braking torque is transmitted between the hub and the rotor via gear teeth.
When the brakes are applied, an air gap (s
L
) is present between the stator and the armature plate. To re-
lease the brake, the coil of the stator is energized with the DC voltage provided. The resulting magnetic
flux works against the spring force to draw the armature plate to the stator. This releases the rotor from the
spring force and allows it to rotate freely.
3.5
Project planning notes
¾
The friction linings are specially designed for the typical usage scenario of a servo drive.
¾
When designing a brake for specific applications, torque tolerances, the limiting speeds of the rotors,
the thermal resistance of the brake, and the effect of environmental influences must all be taken into
account.
¾
However, as the organic friction linings used do not all have identical properties and because environ-
mental conditions can vary, deviations from the specified braking torques are possible. These must be
taken into account in the form of appropriate dimensioning tolerances. Increased breakaway torque is
common in particular after long downtimes in humid environments where temperatures vary.