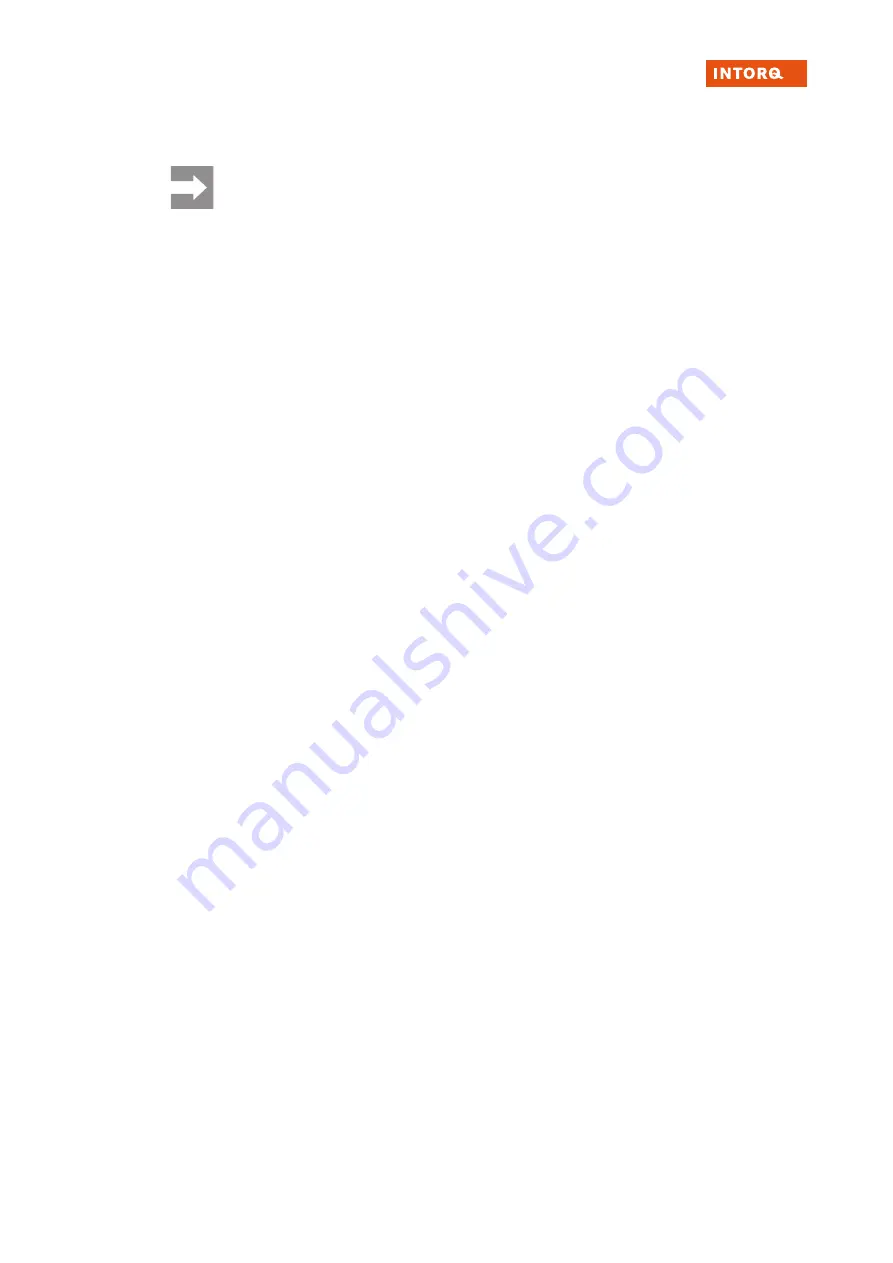
Technical specifications
INTORQ | BA 14.0222 | 06/2020
15
4.4
Electromagnetic compatibility
Notice
The user must ensure compliance with EMC Directive 2014/30/EC using appropriate controls
and switching devices.
4.5
Emissions
Heat
Since the brake converts kinetic energy and electrical energy into heat, the surface temperature varies
considerably, depending on the operating conditions and possible heat dissipation. A surface temperature
of 130 °C may be reached under unfavorable conditions.
In the servo-motor, heat is dissipated by the thermal coupling of the brake to the motor end shield.
Noise
The loudness of the switching noise during engaging and disengaging depends on the air gap "s
L
" and the
brake size.
Depending on the natural oscillation after installation, operating conditions and the state of the friction sur-
faces, the brake may squeak during braking.
4.6
Rust film on friction parts
The flange (sheet metal part) and the counter friction surface are not protected against corrosion. Rust film
may occur under certain circumstances. The functionality of the brake is not affected by this.