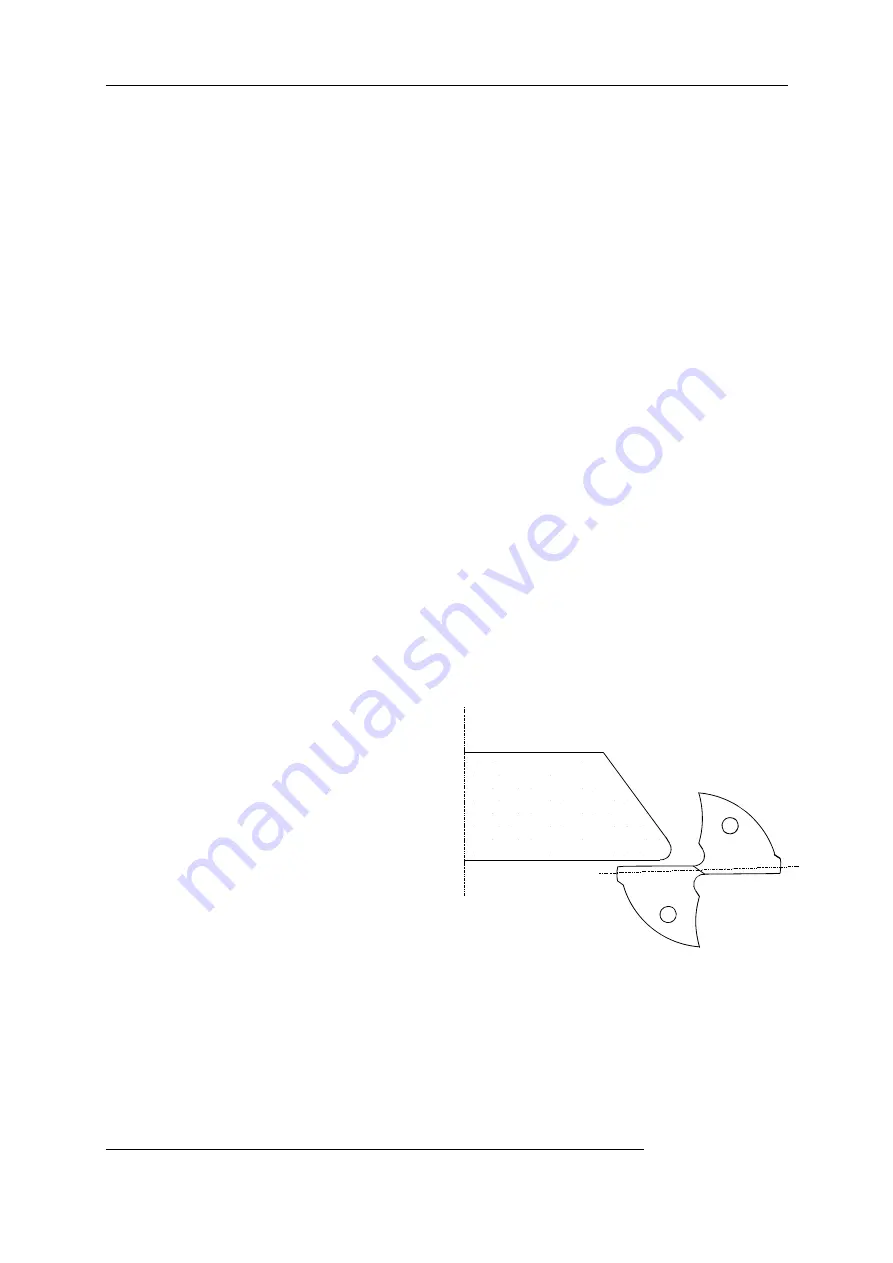
KPS SERIES
Technical
Documentation
M-UK-KPS--06
11/02/03 Page 123 of 138
KALTENBACH
The re grinding of the head of the drill from app. 30° to app. 10° gives the following
advantages:
-
better drilling results;
-
better countermarking;
-
fewer chips during drilling;
-
longer usage-time
-
shorter drilling distance (gain in production time);
-
an optimum feed rate (gain in production time);
-
optimum cutting speed (gain in production time);
-
less drill-resonance.
-
shorter chips
The web of the drill of a normal drill does not cut, but only presses away the material
during the rotation of the drill. Because of this, an enormous drilling pressure is
required (up to 1,000 kg) for drills with a large diameter (> 25 mm).
This causes problems among which:
-
unnecessary fast wear of the drills;
-
maximum burrs caused by the coming through of the drill;
-
no optimum feeding rate (loss of production time);
-
disturbing drill-resonance;
-
distortion of flanges of small profiles.
When grinding out the web, it should be
made certain that on the place of the web
two cutting fields are created.
The making of the cutting area to 16
ensures short, small chips and a even
longer usage-time of the drill.
The level of burrs is further reduced by the
45 inclining of the outer side of the drill.
Refer to the Manual of the Grinding machine BSGB60 for guideline settings for
grinding.
Summary of Contents for KPS 501
Page 1: ...MANUAL KPS 515 Serial No 2008 01 14564...
Page 2: ......
Page 6: ...KPS SERIES Contents M UK KPS 06 11 02 03 Page 6 of 138 KALTENBACH 7 Appendix 138...
Page 136: ......
Page 263: ......
Page 264: ......
Page 265: ......
Page 266: ......
Page 267: ......