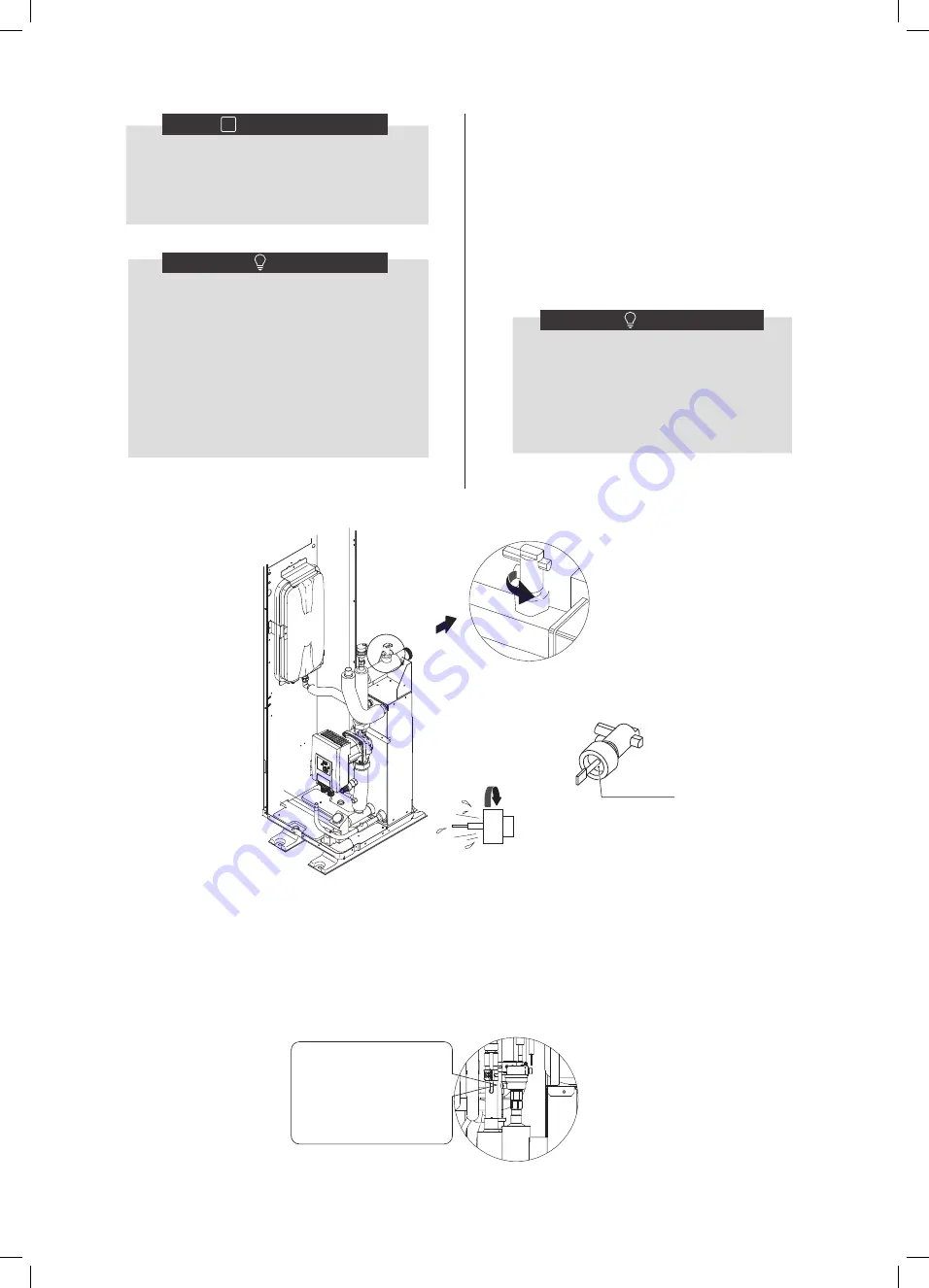
31
Also refer to "
10.3 Pre-operation checks/Checks
before initial start-up
".
Connect the water supply to the fill valve and open the valve.
Make sure the automatic air purge valve is open (at least 2 turns).
Fill with water until the manometer indicates a pressure of approximately 2.0 bar. Remove air in the circuit as much as
possible using the air purge valves. Air in the water circuit could lead to malfunction of the backup electric heater.
9.5 Adding water
Do not fasten the black plastic
cover on the vent valve at the
topside of the unit when the
system is running. Open air
purge valve, turn anticlockWise
at least 2 full turns to release air
from the system.
▪ Protection against bursting: the glycol will prevent
the piping from bursting, but NOT the liquid inside the
piping from freezing.
▪ Protection against freezing: the glycol will prevent
the liquid inside the piping from freezing.
INFORMATION
i
▪ The required concentration might differ depending
on the type of glycol. ALWAYS compare the
requirements from the table above with the specifica-
tions provided by the glycol manufacturer. If
necessary, meet the requirements set by the glycol
manufacturer.
▪ If the liquid in the system is frozen, the pump will
NOT be able to start. Mind that if you only prevent
the system from bursting, the liquid inside might still
freeze.
▪ When water is at standstill inside the system, the
system is very likely to freeze and get damaged.
NOTE
2. Freeze protection by freeze protection
valves
About freeze protection valves
When no glycol is added to the water, you can use
freeze protection valves to drain the water from the
system before it can freeze.
▪
Install freeze protection valves (field supply) at all
lowest points of the field piping.
Normally closed valves (located indoors near the
piping entry/exit points) can prevent that all water
from indoor piping is drained when the freeze
protection valves open.
▪
NOTE
Water may enter into the flow switch and
cannot be drained out and may freeze when
the temperature is low enough. The flow switch
should be removed and dried, then can be
reinstalled in the unit.
Counterclock Wise rotation, remove the flow
switch.
Drying the flow switch completely.
Keep dry
32
A main switch or other means of disconnection, having a contact separation in all poles, must be incorporated in the
fixed wiring in accordance with relevant local laws and regulations. Switch off the power supply before making any
connections. Use only copper wires. Never squeeze bundled cables and make sure they do not come in contact with
the piping and sharp edges. Make sure no external pressure is applied to the terminal connections. All field wiring and
components must be installed by a licensed electrician and must comply with relevant local laws and regulations.
The field wiring must be carried out in accordance with the wiring diagram supplied with the unit and the instructions
given below.
Be sure to use a dedicated power supply. Never use a power supply shared by another appliance.
Be sure to establish a ground. Do not ground the unit to a utility pipe, surge protector, or telephone ground. Incomplete
grounding may cause electrical shock.
Be sure to install a ground fault circuit interrupter (30 mA). Failure to do so may cause electrical shock.
Be sure to install the required fuses or circuit breakers.
WARNING
9.7.2 Wiring overview
The ground fault circuit interrupter must be a high- speed type breaker of 30 mA (<0.1 s).
NOTE
This unit is equipped with an inverter. Installing a phase advancing capacitor not only will reduce the power factor improve-
ment effect, but also may cause abnormal heating of the capacitor due to high-frequency waves. Never install a phase
advancing capacitor as it could lead to an accident.
The illustration below gives an overview of the required field wiring between several parts of the installation. Refer also to "8
Typical application examples".
Secure the electrical wiring with cable ties as shown in figure so that it does not come in contact with the piping, particularly
on the high-pressure side.
Make sure no external pressure is applied to the terminal connectors.
When installing the ground fault circuit interrupter make sure that it is compatible with the inverter (resistant to high frequency
electrical noise) to avoid unnecessary opening of the ground fault circuit interrupter.
Fix cables so that cables do not make contact with the pipes (especially on the high pressure side).
9.7.1 Precautions on electrical wiring work
9.6 Water piping insulation
9.7 Field wiring
The complete water circuit including all piping, water piping must be insulated to prevent condensation during cooling operation
and reduction of the heating and cooling capacity as well as prevention of freezing of the outside water piping during winter. The
insulation material should at least of B1 fire resistance rating and complies with all applicable legislation. The thickness of the
sealing materials must be at least 13 mm with thermal conductivity 0.039 W/mK in order to prevent freezing on the outside water
piping.
If the outdoor ambient temperature is higher than 30°C and the humidity is higher than RH 80%, then the thickness of the
sealing materials should be at least 20 mm in order to avoid condensation on the surface of the seal.
NOTE
During filling, it might not be possible to remove all air in the system. Remaining air will be removed through the
automatic air purge valves during the first operating hours of the system. Topping up the water afterwards might be
required.
The water pressure indicated on the manometer will vary depending on the water temperature (higher pressure at
higher water temperature). However, at all times water pressure should remain above 0.3 bar to avoid air entering
the circuit.
The unit might drain-off too much water through the pressure relief valve.
Water quality should be complied with EN 98/83 EC Directives.
Detailed water quality condition can be found in EN 98/83 EC Directives.
115
114
Summary of Contents for MONO KHC-22RX3
Page 1: ...INSTRUKCJA INSTALACYJNA INSTALATIONMANUAL POMPA CIEPŁA MONO MONO TYPE HEAT PUMP PL EN ...
Page 2: ......
Page 79: ...79 ...
Page 80: ......
Page 157: ...NOTE 157 ...
Page 158: ...NOTE ...
Page 159: ...16125300002403 V C ...
Page 160: ...kaisai com ...