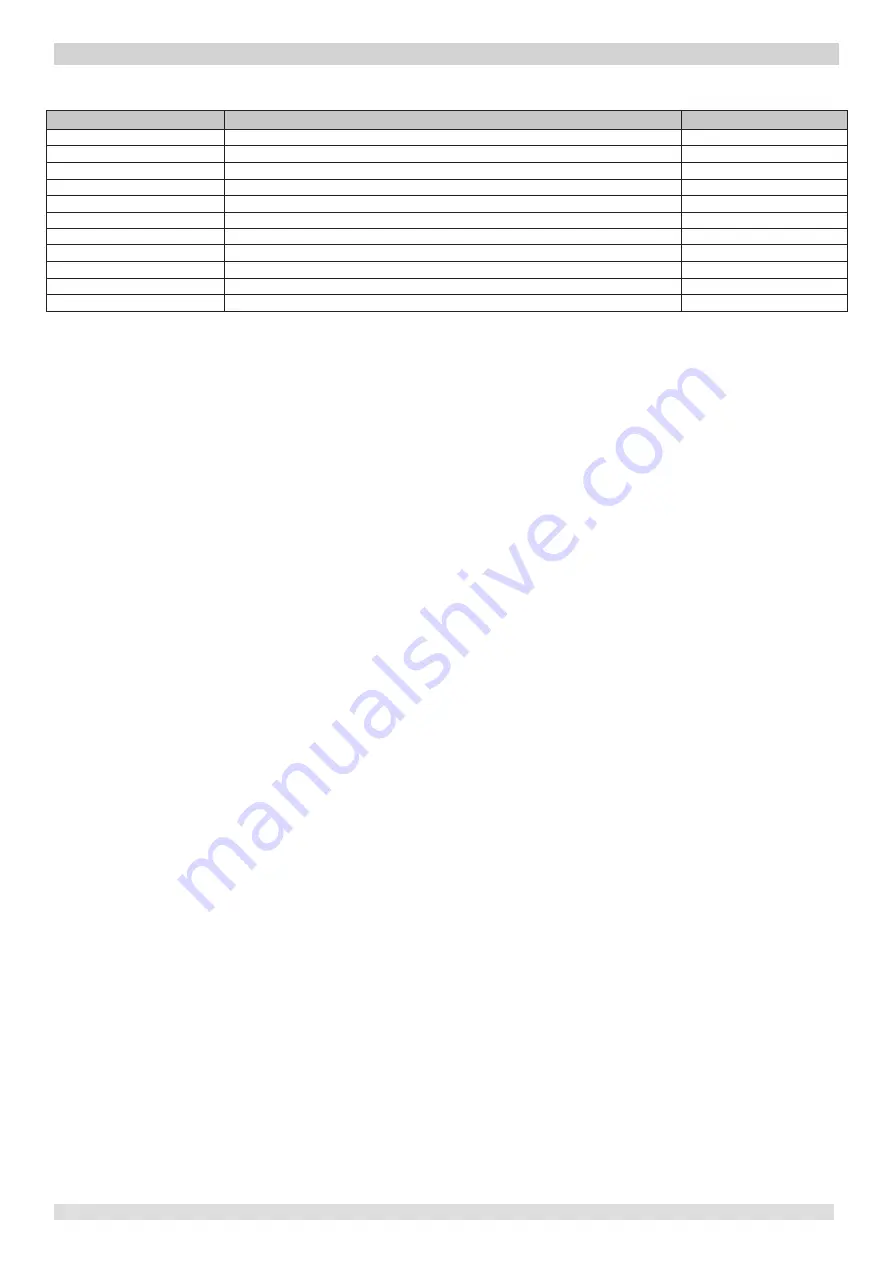
M thermal Split
30
202004
Midea
M t
her
ma
l S
pli
t Ser
vice M
anual
Table 3-7.1: Names of the temperature sensors
Number
Sensor name
Sensor code
1
Suction pipe temperature sensor
Th
2
Discharge pipe temperature sensor
Tp
3
Outdoor ambient temperature sensor
T4
4
Air side heat exchanger refrigerant outlet temperature sensor
T3
5
Water side heat exchanger
refrigerant outlet (gas pipe)
temperature sensor
T2B
6
Water side heat exchanger
refrigerant outlet (liquid pipe)
temperature sensor
T2
7
Water side heat exchanger
water out
let temperature sensor
Tw_out
8
Water side heat exchanger
water i
nlet temperature sensor
Tw_in
9
Final water outlet temperature sensor
T1
10
Domestic hot water tank temperature sensor
T5
11
Room temperature sensor (built in wired controller)
Ta
Midea CAC Confidential
Split
Summary of Contents for KMK-60RY1
Page 1: ...SERVICEMANUAL SPLIT TYPE HEAT PUMP R32...
Page 2: ...Split...
Page 4: ...M thermal Split 2 202004 Midea M thermal Split Service Manual Midea CAC Confidential Split...
Page 8: ...M thermal Split 6 202004 Midea M thermal Split Service Manual Midea CAC Confidential Split...
Page 18: ...M thermal Split Midea M thermal Split Service Manual 16 202004 Midea CAC Confidential Split...
Page 41: ...M thermal Split 202004 39 Midea CAC Confidential Split...
Page 42: ...M thermal Split 40 202004 Midea M thermal Split Service Manual Midea CAC Confidential Split...
Page 113: ...Split...
Page 114: ...kaisai com...