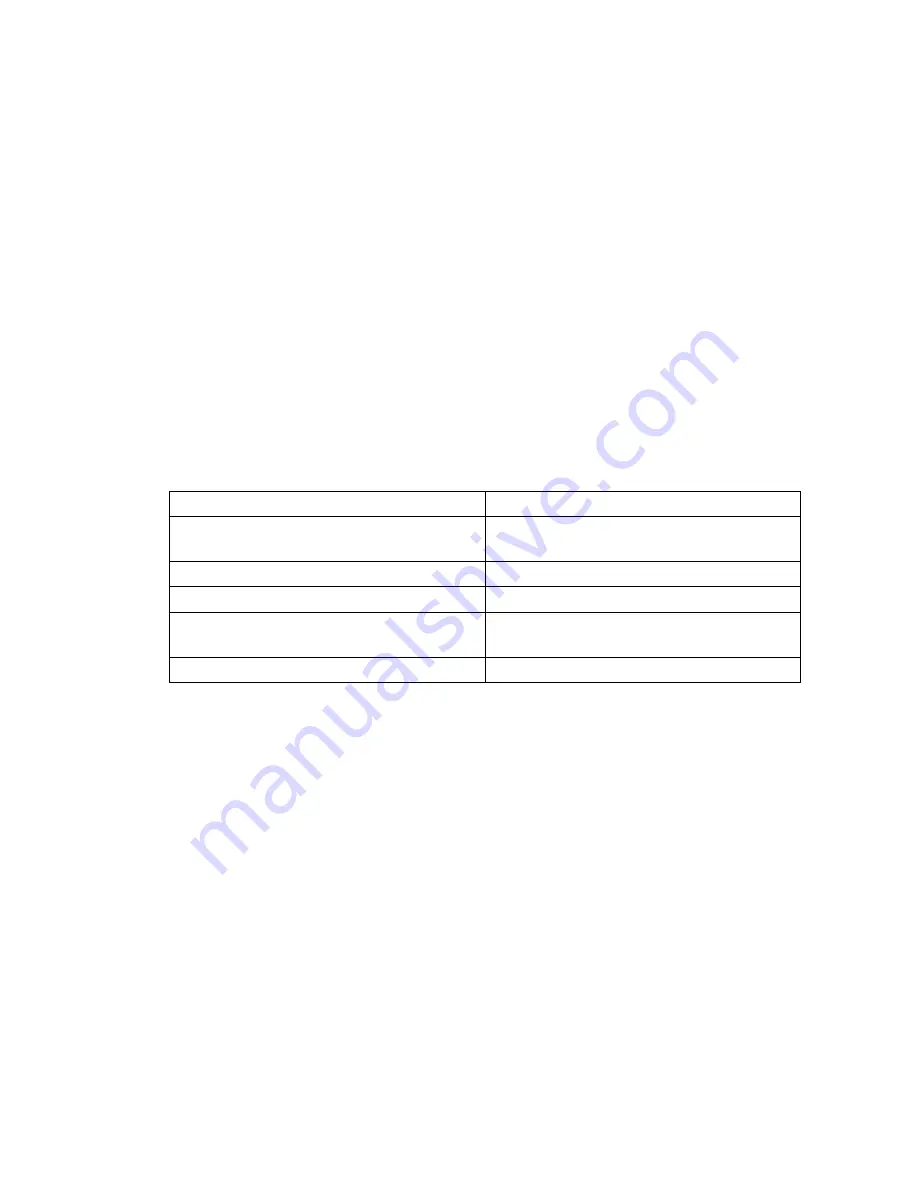
11
.1
4
E
N
58
5
Troubleshooting
This chapter enables the user to identify and rectify basic faults and the effects of
incorrect operation. When trying to locate a fault, proceed in the order shown in the
table.
Z
If, after carrying out the following remedial action, the truck cannot be restored to
operation or if a fault in the electronics system is displayed with a corresponding
error code, contact the manufacturer’s service department.
Additional troubleshooting must only be performed by the manufacturer’s specialist
service engineers. The manufacturer's customer service department is specially
trained to carry out these operations.
In order for customer services to react quickly and specifically to the fault, the
following information is essential:
- Truck serial number
- Error number on the display unit (if applicable)
- Error description
- Current location of truck
5.1
Truck does not start
Possible Cause
Action
Battery connector not plugged in
Check the battery connector and plug it in
if necessary.
Emergency Disconnect pressed.
Unlock the Emergency Disconnect
Key switch set to O.
Set the key switch to “I”
Battery charge too low
Check the battery charge and charge
battery if necessary.
Faulty fuse
Check fuses
11
.1
4
E
N
58
5
Troubleshooting
This chapter enables the user to identify and rectify basic faults and the effects of
incorrect operation. When trying to locate a fault, proceed in the order shown in the
table.
Z
If, after carrying out the following remedial action, the truck cannot be restored to
operation or if a fault in the electronics system is displayed with a corresponding
error code, contact the manufacturer’s service department.
Additional troubleshooting must only be performed by the manufacturer’s specialist
service engineers. The manufacturer's customer service department is specially
trained to carry out these operations.
In order for customer services to react quickly and specifically to the fault, the
following information is essential:
- Truck serial number
- Error number on the display unit (if applicable)
- Error description
- Current location of truck
5.1
Truck does not start
Possible Cause
Action
Battery connector not plugged in
Check the battery connector and plug it in
if necessary.
Emergency Disconnect pressed.
Unlock the Emergency Disconnect
Key switch set to O.
Set the key switch to “I”
Battery charge too low
Check the battery charge and charge
battery if necessary.
Faulty fuse
Check fuses
Summary of Contents for EZS 350 XL
Page 1: ...08 09 11 14 51133023 EZS 350 350 XL C40 Operating instructions G EZS 350 XL EZS C40 EZS 350 ...
Page 3: ...11 14 EN 4 ...
Page 9: ...0506 GB 2 ...
Page 18: ...17 11 14 EN 3 2 Dimensions ...
Page 25: ...11 14 EN 24 ...
Page 29: ...11 14 EN 28 ...
Page 39: ...11 14 EN 38 ...
Page 42: ...41 11 14 EN 2 Displays and Controls 44 4 3 45 41 8 9 7 6 10 41 8 11 43 5 10 42 ...
Page 77: ...11 14 EN 76 ...