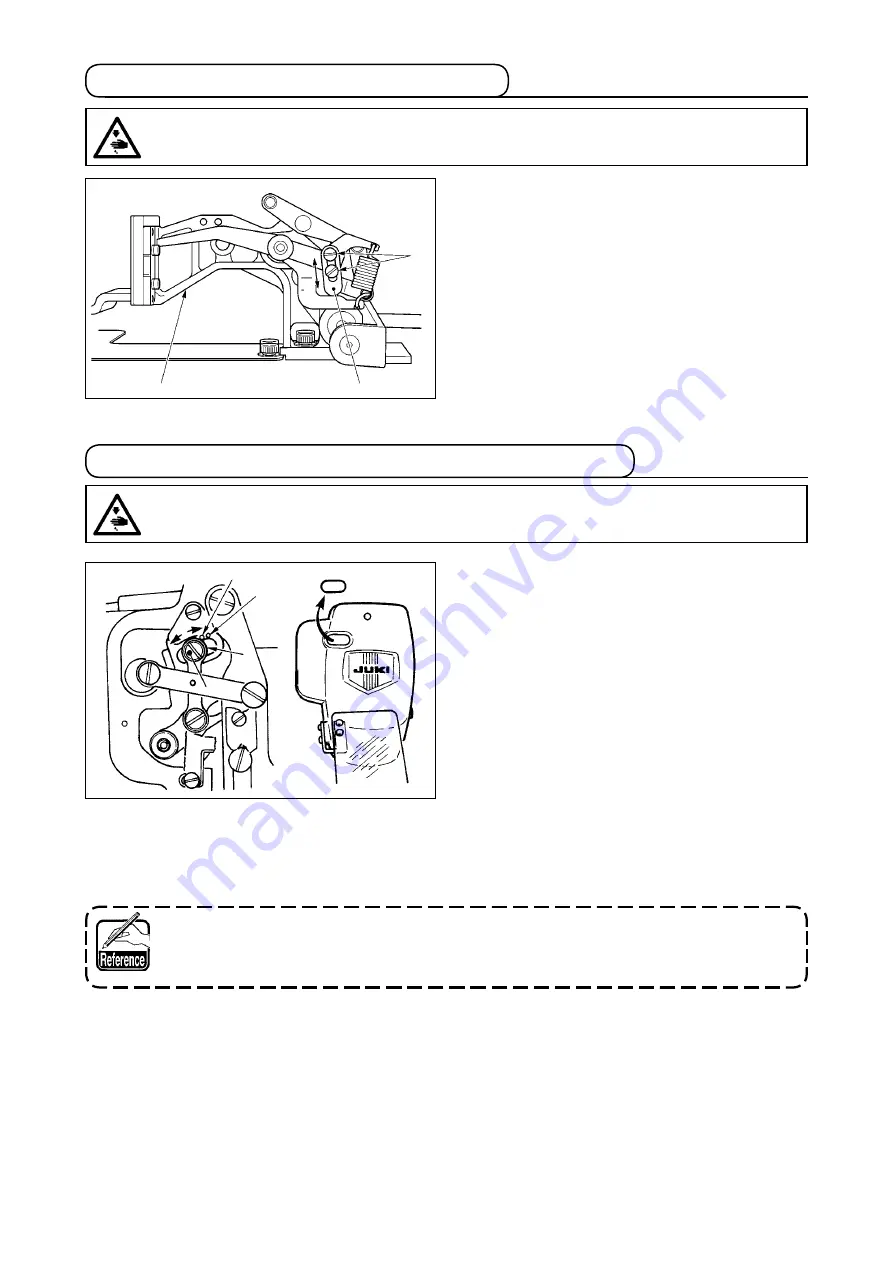
– 116 –
1
A
B
1-4. Adjusting the vertical stroke of the intermediate presser
* Turn ON the power once, and turn OFF the
power again after making the intermediate
presser in the lowered state.
1) Remove face cover.
2) Turn handwheel to make the needle bar come
down to its lowest point.
3) Loosen hinge screw
1
and move it to the
direction
A
to increase the stroke.
4) When marker dot
A
is aligned with the right
side of the outer periphery of washer
2
, the
vertical stroke of the intermediate presser
becomes 4 mm. And, when marker dot
B
is
aligned with the right side of the outer periphery
of the washer, it becomes 7 mm. (The vertical
stroke of the intermediate presser is factory-set
to 4 mm at the time of delivery.)
By removing the rubber plug in the face plate cover, adjustment can be performed
without removing the face plate cover.
2
A
1-3. Adjusting the height of the feeding frame
1
3
2
1) Loosen screws
2
located on the right and left
sides of feed bracket
1
. Moving cloth presser
stopper
3
to the direction B will increase the
height of feeding frame.
2) After the adjustment of the height of the feeding
frame, securely tighten the screws
2
.
WARNING :
Turn OFF the power before starting the work so as to prevent accidents caused by abrupt start of
the sewing machine.
WARNING :
Turn OFF the power before starting the work so as to prevent accidents caused by abrupt start of
the sewing machine.
A
B