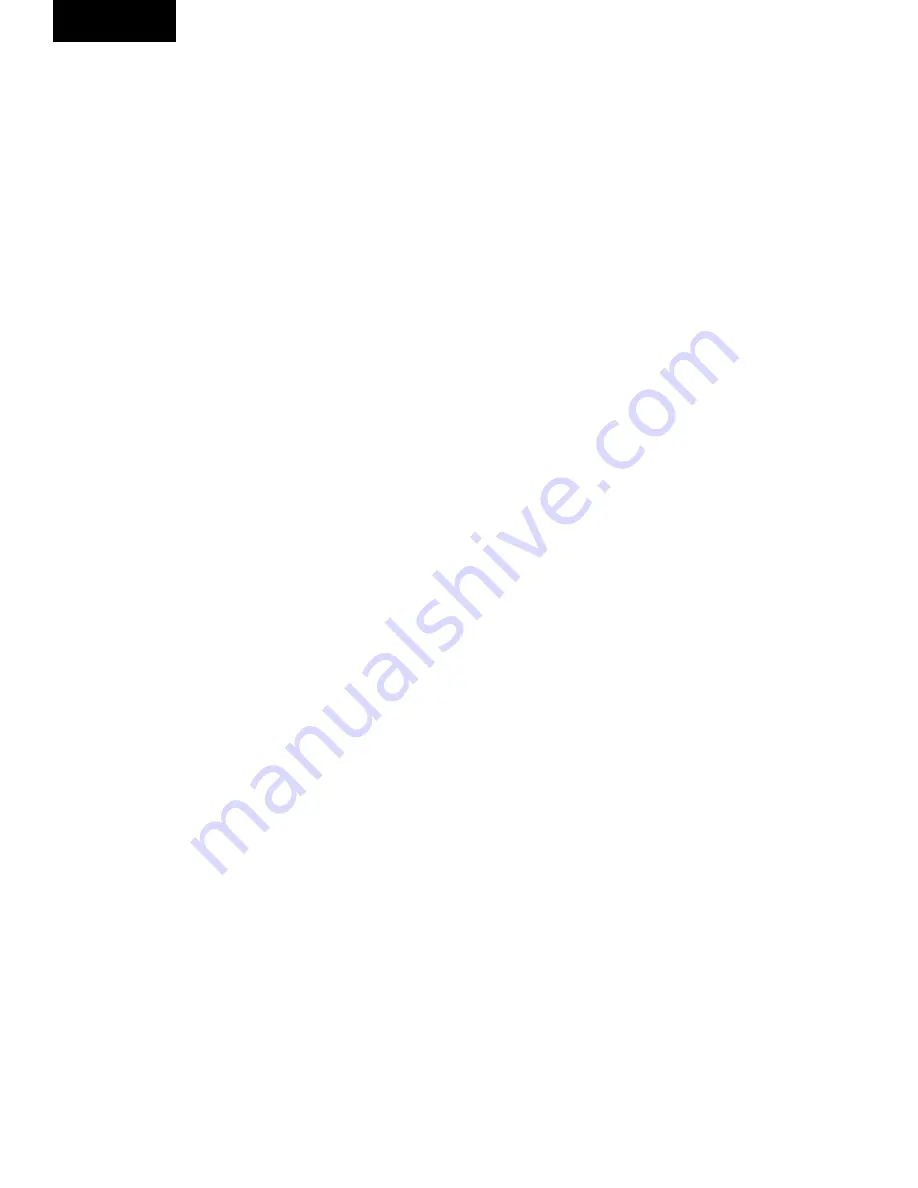
JOHNSON CONTROLS
42
FORM 150.72-NM1 (1020)
Installation
DUCT WORK CONNECTION
General Requirements
The following duct work recommendations are intended
to ensure satisfactory operation of the unit. Failure to
follow these recommendations could cause damage to
the unit, or loss of performance, and may invalidate the
warranty.
When ducting is to be fitted to the fan discharge it is
recommended that the duct should be the same cross-
sectional area as the fan outlet and straight for at least
three feet (1 meter) to obtain static regain from the fan.
Duct work should be suspended with flexible hangers
to prevent noise and vibration being transmitted to the
structure. A flexible joint is also recommended between
the duct attached to the fan and the next section for the
same reason. Flexible connectors should not be allowed
to concertina.
The unit(s) is not designed to take structural loading. No
significant amount of weight should be allowed to rest
on the fan outlet flange, deck assemblies or condenser
coil module. No more than 3 feet (1 meter) of light
construction duct work should be supported by the unit.
Where cross winds may occur, any duct work must be
supported to prevent side loading on the unit.
If the ducts from two or more fans are to be combined
into a common duct, back-flow dampers should be
fitted in the individual fan ducts. This will prevent re-
circulation of air when only one of the fans is running.
Units are supplied with outlet guards for safety and
to prevent damage to the fan blades. If these guards
are removed to fit duct work, adequate alternative
precautions must be taken to ensure persons cannot be
harmed or put at risk from rotating fan blades.
WIRING
Liquid Chillers are shipped with all factory-mounted
controls wired for operation.
Field Wiring –
Power wiring must be provided through
a fused disconnect switch to the unit terminals (or
optional molded disconnect switch) in accordance with
N.E.C. or local code requirements. Minimum circuit
ampacity and maximum dual element fuse size are given
in Tables 5 .
Copper power wiring only should be used for supplying
power to the chiller. This is recommended to avoid safety
and reliability issues resulting from connection failure at
the power connections to the chiller. Aluminum wiring
is not recommended due to thermal characteristics
that may cause loose terminations resulting from the
contraction and expansion of the wiring. Aluminum
oxide may also build up at the termination causing hot
spots and eventual failure. If aluminum wiring is used
to supply power to the chiller, AL-CU compression
fittings should be used to transition from aluminum to
copper. This transition should be done in an external
box separate to the power panel. Copper conductors
can then be run from the box to the chiller.
A 120-1-60, 15 amp source must be supplied for the
control panel through a fused disconnect when a control
panel transformer (optional) is not provided
(Refer to
Fig. 9).
See unit wiring diagrams for field and power wiring
connections, chilled water pump starter contacts,
alarm contacts, compressor run status contacts, PWM
input, and load limit input. Refer to section on UNIT
OPERATION for a detailed description of operation
concerning aforementioned contacts and inputs.
Evaporator Pump Start Contacts
Terminal Block XTBC2 – Terminals 23 (115VAC) to 24,
are nor mally- open contacts that can be used to switch
field supplied power to provide a start signal to the
evapo rator pump contactor. The contacts will be closed
when any of the following conditions occur:
1. Low Leaving Chilled Liquid Fault
2. Any compressor is running
3. Daily schedule is not programmed OFF and the
Unit Switch is ON
The pump will not run if the microprocessor panel has
been powered up for less than 30 seconds, or if the pump
has run in the last 30 seconds, to prevent pump motor
overheating.
Refer to Fig. 11 and unit wiring dia gram.
System Run Contacts
Contacts are available to monitor system status.
Normally-open auxiliary contacts from each com pressor
contactor are wired in parallel with XTBC2 – Terminals
25 to 26 for system 1, and XTBC2 – Terminals 27 to
28 for system 2.
Refer to Fig. 4, 11 and unit wiring
diagram.
Summary of Contents for YORK Tempo YLAA Series
Page 4: ...JOHNSON CONTROLS 4 FORM 150 72 NM1 1020 THIS PAGE INTENTIONALLY LEFT BLANK...
Page 12: ...JOHNSON CONTROLS 12 FORM 150 72 NM1 1020 THIS PAGE INTENTIONALLY LEFT BLANK...
Page 14: ...JOHNSON CONTROLS 14 FORM 150 72 NM1 1020 THIS PAGE INTENTIONALLY LEFT BLANK...
Page 18: ...JOHNSON CONTROLS 18 FORM 150 72 NM1 1020 THIS PAGE INTENTIONALLY LEFT BLANK...
Page 36: ...JOHNSON CONTROLS 36 FORM 150 72 NM1 1020 THIS PAGE INTENTIONALLY LEFT BLANK...
Page 49: ...FORM 150 72 NM1 1020 49 JOHNSON CONTROLS THIS PAGE INTENTIONALLY LEFT BLANK...
Page 71: ...FORM 150 72 NM1 1020 71 JOHNSON CONTROLS THIS PAGE INTENTIONALLY LEFT BLANK...
Page 73: ...FORM 150 72 NM1 1020 73 JOHNSON CONTROLS 5 5...
Page 75: ...FORM 150 72 NM1 1020 75 JOHNSON CONTROLS 5 5...
Page 77: ...FORM 150 72 NM1 1020 77 JOHNSON CONTROLS 5 5...
Page 79: ...FORM 150 72 NM1 1020 79 JOHNSON CONTROLS 5 5...
Page 81: ...FORM 150 72 NM1 1020 81 JOHNSON CONTROLS 5 5...
Page 83: ...FORM 150 72 NM1 1020 83 JOHNSON CONTROLS 5 5...
Page 85: ...FORM 150 72 NM1 1020 85 JOHNSON CONTROLS 5 5 LD13901...
Page 87: ...FORM 150 72 NM1 1020 87 JOHNSON CONTROLS 5 5...
Page 89: ...FORM 150 72 NM1 1020 89 JOHNSON CONTROLS 5 5 LD13232...
Page 91: ...FORM 150 72 NM1 1020 91 JOHNSON CONTROLS THIS PAGE INTENTIONALLY LEFT BLANK...
Page 92: ...JOHNSON CONTROLS 92 FORM 150 72 NM1 1020 Technical Data WIRING LD13238 FIG 22 WIRING...
Page 93: ...FORM 150 72 NM1 1020 93 JOHNSON CONTROLS 5 5 LD13239...
Page 176: ...JOHNSON CONTROLS 176 FORM 150 72 NM1 1020 THIS PAGE INTENTIONALLY LEFT BLANK...
Page 191: ...FORM 150 72 NM1 1020 191 JOHNSON CONTROLS 10 NOTES...