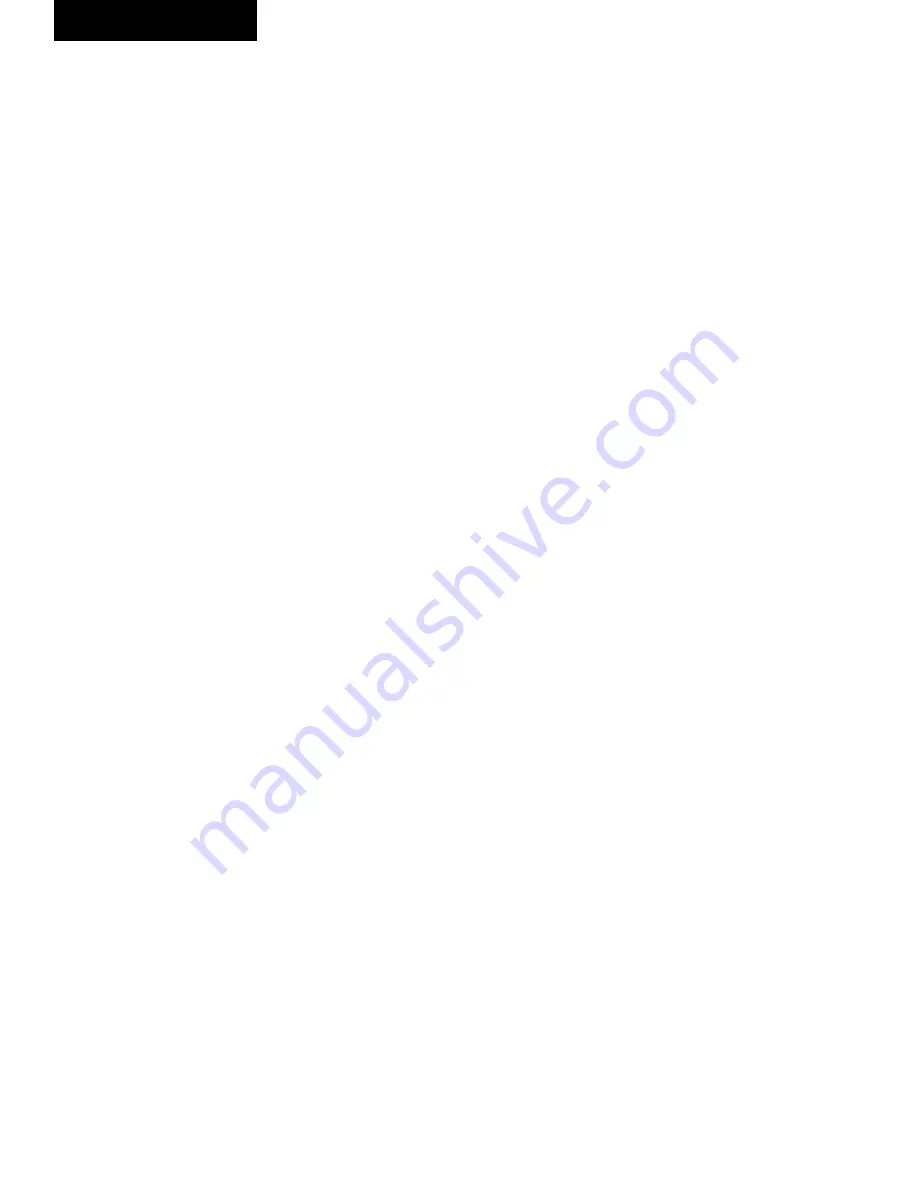
JOHNSON CONTROLS
20
FORM 150.72-NM1 (1020)
Product Description
The evaporator is constructed, tested and stamped in
accordance with applicable sections of ASME pressure
vessel code for minimum 450 PSIG (3103 kPa)
refrigerant side design working pressure and 150 PSIG
(1034 kPa) water side design working pressure
A strainer with a mesh size between .5 and 1.5 mm (40
mesh) is recommended upstream of the heat exchanger
to prevent clogging from water system debris.
Condenser
Coils
Condenser coils are Microchannel type and made of
a single material to avoid galvanic corrosion due to
dissimilar metals. Coils and headers are brazed as one
piece. Integral sub cooling is included. The design
working pressure of the coil is 650 PSIG (45 bar).
Low Sound Fans
The condenser fans are composed of corrosion resistant
aluminum hub and glass-fiber reinforced polypropylene
composite blades molded into a low noise airfoil section.
They are designed for maximum efficiency and are
statically and dynamically balanced for vibration free
operation. They are directly driven by independent
motors, and positioned for vertical air discharge. The
fan guards are constructed of heavy gauge, rust resistant,
coated steel. All blades are statically and dynamically
balanced for vibration free operation.
Motors
The fan motors are Totally Enclosed Air-Over, squirrel
cage type, current protected. They feature ball bearings
that are double sealed and permanently lubricated.
Ambient Kit (High)
Required if units are to operate when the ambient
temperature is above 115°F (46°C). Includes discharge
pressure transducers.
Millennium Control Center
All controls are contained in a NEMA 3R/12 cabinet
with hinged outer door and includes Liquid Crystal
Display with Light Emitting Diode backlighting for
outdoor viewing:
• Two display lines
• Twenty characters per line
Display/Print
Color coded 12-button non-tactile keypad with sections
for display and print of typical information:
• Chilled liquid temperatures
• Ambient temperature
• System pressures (each circuit)
• Operating hours and starts (each compressor)
• Print calls up to the liquid crystal display
• Operating data for the systems
• History of fault shutdown data for up to the last
six fault shutdown conditions.
• An RS-232 port, in conjunction with this press-to-
print button, is provided to permit the capability
of hard copy print-outs via a separate printer (by
others).
Entry
This section is used to enter setpoints or modify system
values.
Setpoints
Updating can be performed to:
• Chilled liquid temperature setpoint and range
• Remote reset temperature range
• Set daily schedule/holiday for start/stop
• Manual override for servicing
• Low and high ambient cutouts
• Number of compressors
• Low liquid temperature cutout
• Low suction pressure cutout
• High discharge pressure cutout
• Anti-recycle timer (compressor start cycle
time)
• Anti-coincident timer (delay compressor starts)
Unit
This section is used to:
• Set time
• Set unit options
Summary of Contents for YORK Tempo YLAA Series
Page 4: ...JOHNSON CONTROLS 4 FORM 150 72 NM1 1020 THIS PAGE INTENTIONALLY LEFT BLANK...
Page 12: ...JOHNSON CONTROLS 12 FORM 150 72 NM1 1020 THIS PAGE INTENTIONALLY LEFT BLANK...
Page 14: ...JOHNSON CONTROLS 14 FORM 150 72 NM1 1020 THIS PAGE INTENTIONALLY LEFT BLANK...
Page 18: ...JOHNSON CONTROLS 18 FORM 150 72 NM1 1020 THIS PAGE INTENTIONALLY LEFT BLANK...
Page 36: ...JOHNSON CONTROLS 36 FORM 150 72 NM1 1020 THIS PAGE INTENTIONALLY LEFT BLANK...
Page 49: ...FORM 150 72 NM1 1020 49 JOHNSON CONTROLS THIS PAGE INTENTIONALLY LEFT BLANK...
Page 71: ...FORM 150 72 NM1 1020 71 JOHNSON CONTROLS THIS PAGE INTENTIONALLY LEFT BLANK...
Page 73: ...FORM 150 72 NM1 1020 73 JOHNSON CONTROLS 5 5...
Page 75: ...FORM 150 72 NM1 1020 75 JOHNSON CONTROLS 5 5...
Page 77: ...FORM 150 72 NM1 1020 77 JOHNSON CONTROLS 5 5...
Page 79: ...FORM 150 72 NM1 1020 79 JOHNSON CONTROLS 5 5...
Page 81: ...FORM 150 72 NM1 1020 81 JOHNSON CONTROLS 5 5...
Page 83: ...FORM 150 72 NM1 1020 83 JOHNSON CONTROLS 5 5...
Page 85: ...FORM 150 72 NM1 1020 85 JOHNSON CONTROLS 5 5 LD13901...
Page 87: ...FORM 150 72 NM1 1020 87 JOHNSON CONTROLS 5 5...
Page 89: ...FORM 150 72 NM1 1020 89 JOHNSON CONTROLS 5 5 LD13232...
Page 91: ...FORM 150 72 NM1 1020 91 JOHNSON CONTROLS THIS PAGE INTENTIONALLY LEFT BLANK...
Page 92: ...JOHNSON CONTROLS 92 FORM 150 72 NM1 1020 Technical Data WIRING LD13238 FIG 22 WIRING...
Page 93: ...FORM 150 72 NM1 1020 93 JOHNSON CONTROLS 5 5 LD13239...
Page 176: ...JOHNSON CONTROLS 176 FORM 150 72 NM1 1020 THIS PAGE INTENTIONALLY LEFT BLANK...
Page 191: ...FORM 150 72 NM1 1020 191 JOHNSON CONTROLS 10 NOTES...