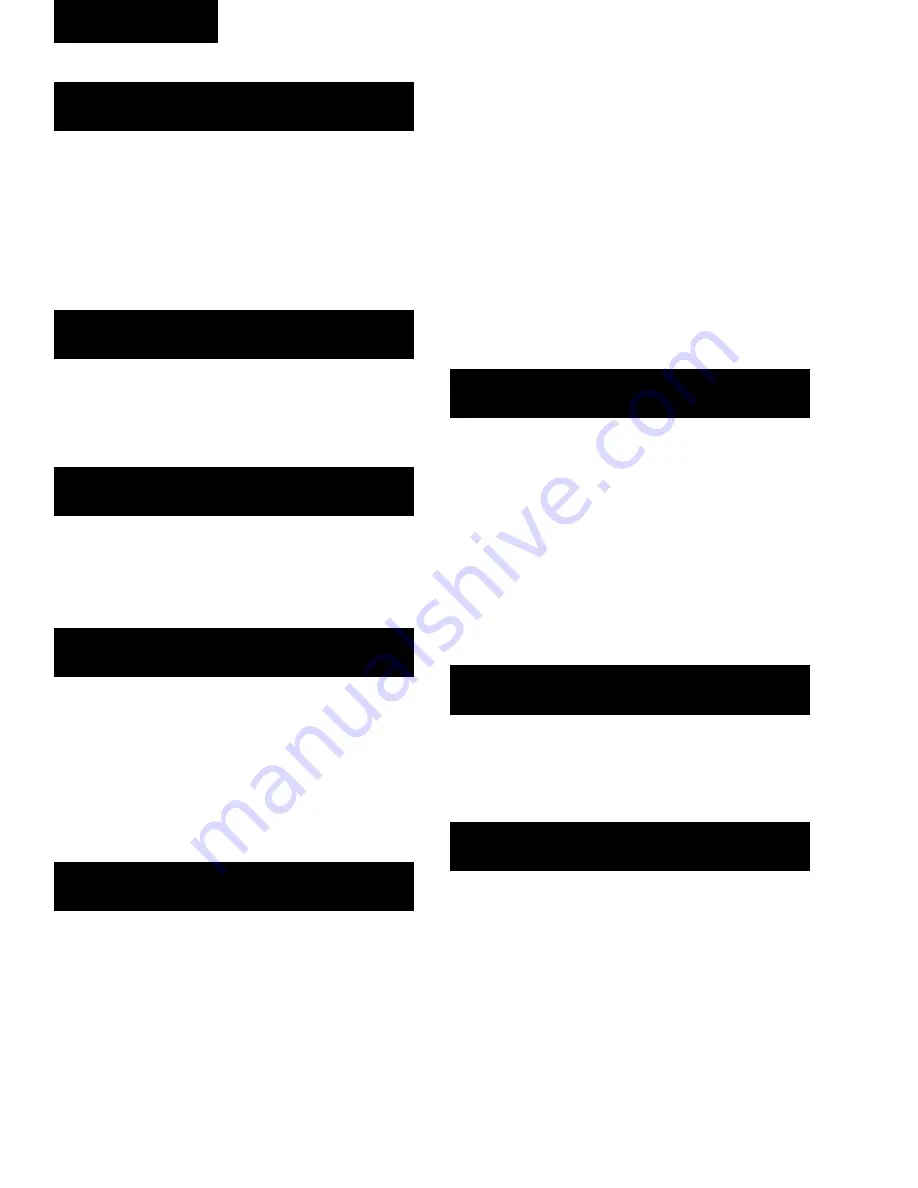
JOHNSON CONTROLS
128
FORM 150.72-NM1 (1020)
Unit Controls
This message informs the operator that the chilled
liquid temperature is below the point (determined by
the setpoint and control range) that the microprocessor
will bring on a system or that the microprocessor has
not loaded the lead system far enough into the loading
sequence to be ready to bring the lag system “ON”. The
lag system will display this message until the loading
sequence is ready for the lag system to start.
The COMPS RUNNING message indicates that the
respective system is running due to demand. The “X”
will be replaced with the number of compressors in that
system that are running.
The anti-recycle timer message shows the amount of
time left on the respective systems anti-recycle timer.
This message is displayed when the system is unable to
start due the anti-recycle timer being active.
The anti-coincidence timer is a software feature that
guards against 2 systems starting simultaneously.
This assures instantaneous starting current does not
become excessively high due to simultaneous starts.
The microprocessor limits the time between compressor
starts to 1 minute regardless of demand or the anti-
recycle timer being timed out. The anti-coincidence
timer is only present on two system units.
`
When this message appears, discharge pressure limiting
is in effect. The Discharge Pressure Limiting feature
is integral to the standard software control; however
the discharge transducer is optional on some models.
Therefore, it is important to keep in mind that this
control will not function unless the discharge transducer
is installed in the system.
S Y S 1 N O C O O L L O A D
S Y S 2 N O C O O L L O A D
S Y S 1 C O M P S R U N X
S Y S 2 C O M P S R U N X
S Y S 1 A R T I M E R X X S
S Y S 2 A R T I M E R X X S
S Y S 1 A C T I M E R X X S
S Y S 2 A C T I M E R X X S
S Y S 1 D S C H L I M I T I N G
S Y S 2 D S C H L I M I T I N G
The limiting pressure is a factory set limit to keep the
system from faulting on the high discharge pressure
cutout due to high load or pull down conditions.
When the unload point is reached, the microprocessor
will automatically unload the affected system by de
energizing one compressor. The discharge pressure
unload will occur when the discharge pressure gets
within 10 PSIG (0.69 barg) of the programmed discharge
pressure cutout. This will only happen if the system is
fully loaded and will shut only one compressor off. If
the system is not fully loaded, discharge limiting will
not go into effect. Reloading the affected system will
occur when the discharge pressure drops to 85% of the
unload pressure and 10 minutes have elapsed.
`
When this message appears, suction pressure limiting is
in effect. The suction pressure limit is a control point that
limits the loading of a system when the suction pressure
drops to within 15% above the suction pressure cutout.
On a standard system programmed for 44 PSIG/3.0
Bar suction pressure cutout, the microprocessor would
inhibit loading of the affected system with the suction
pressure less than or equal to 1.15 * 44 PSIG/3.0 Bar
= 50 PSIG/3.5 Bar. The system will be allowed to load
after 60 seconds and after the suction pressure rises
above the suction pressure load limit point.
`
This message indicates that load limiting is in effect and
the percentage of the limiting in effect. This limiting
could be due to the load limit/pwm input, ISN or RCC
controller sending a load limit command.
If MANUAL OVERRIDE mode is selected, the STATUS
display will display this message. This will indicate that
the Daily Schedule is being ignored and the chiller will
start-up when chilled liquid temperature allows, Remote
Contacts, UNIT switch and SYSTEM switches permitting.
This is a priority message and cannot be overridden by
anti-recycle messages, fault messages, etc. when in the
STATUS display mode. Therefore, do not expect to see
any other STATUS messages when in the MANUAL
OVERRIDE mode. MANUAL OVERRIDE is to only
be used in emergencies or for servicing. Manual override
mode automatically disables itself after 30 minutes.
S Y S 1 S U C T L I M I T I N G
S Y S 2 S U C T L I M I T I N G
S Y S 1 L O A D L I M I T X X %
S Y S 2 L O A D L I M I T X X %
M
A N
U A L
O
V E R
R I D E
Summary of Contents for YORK Tempo YLAA Series
Page 4: ...JOHNSON CONTROLS 4 FORM 150 72 NM1 1020 THIS PAGE INTENTIONALLY LEFT BLANK...
Page 12: ...JOHNSON CONTROLS 12 FORM 150 72 NM1 1020 THIS PAGE INTENTIONALLY LEFT BLANK...
Page 14: ...JOHNSON CONTROLS 14 FORM 150 72 NM1 1020 THIS PAGE INTENTIONALLY LEFT BLANK...
Page 18: ...JOHNSON CONTROLS 18 FORM 150 72 NM1 1020 THIS PAGE INTENTIONALLY LEFT BLANK...
Page 36: ...JOHNSON CONTROLS 36 FORM 150 72 NM1 1020 THIS PAGE INTENTIONALLY LEFT BLANK...
Page 49: ...FORM 150 72 NM1 1020 49 JOHNSON CONTROLS THIS PAGE INTENTIONALLY LEFT BLANK...
Page 71: ...FORM 150 72 NM1 1020 71 JOHNSON CONTROLS THIS PAGE INTENTIONALLY LEFT BLANK...
Page 73: ...FORM 150 72 NM1 1020 73 JOHNSON CONTROLS 5 5...
Page 75: ...FORM 150 72 NM1 1020 75 JOHNSON CONTROLS 5 5...
Page 77: ...FORM 150 72 NM1 1020 77 JOHNSON CONTROLS 5 5...
Page 79: ...FORM 150 72 NM1 1020 79 JOHNSON CONTROLS 5 5...
Page 81: ...FORM 150 72 NM1 1020 81 JOHNSON CONTROLS 5 5...
Page 83: ...FORM 150 72 NM1 1020 83 JOHNSON CONTROLS 5 5...
Page 85: ...FORM 150 72 NM1 1020 85 JOHNSON CONTROLS 5 5 LD13901...
Page 87: ...FORM 150 72 NM1 1020 87 JOHNSON CONTROLS 5 5...
Page 89: ...FORM 150 72 NM1 1020 89 JOHNSON CONTROLS 5 5 LD13232...
Page 91: ...FORM 150 72 NM1 1020 91 JOHNSON CONTROLS THIS PAGE INTENTIONALLY LEFT BLANK...
Page 92: ...JOHNSON CONTROLS 92 FORM 150 72 NM1 1020 Technical Data WIRING LD13238 FIG 22 WIRING...
Page 93: ...FORM 150 72 NM1 1020 93 JOHNSON CONTROLS 5 5 LD13239...
Page 176: ...JOHNSON CONTROLS 176 FORM 150 72 NM1 1020 THIS PAGE INTENTIONALLY LEFT BLANK...
Page 191: ...FORM 150 72 NM1 1020 191 JOHNSON CONTROLS 10 NOTES...