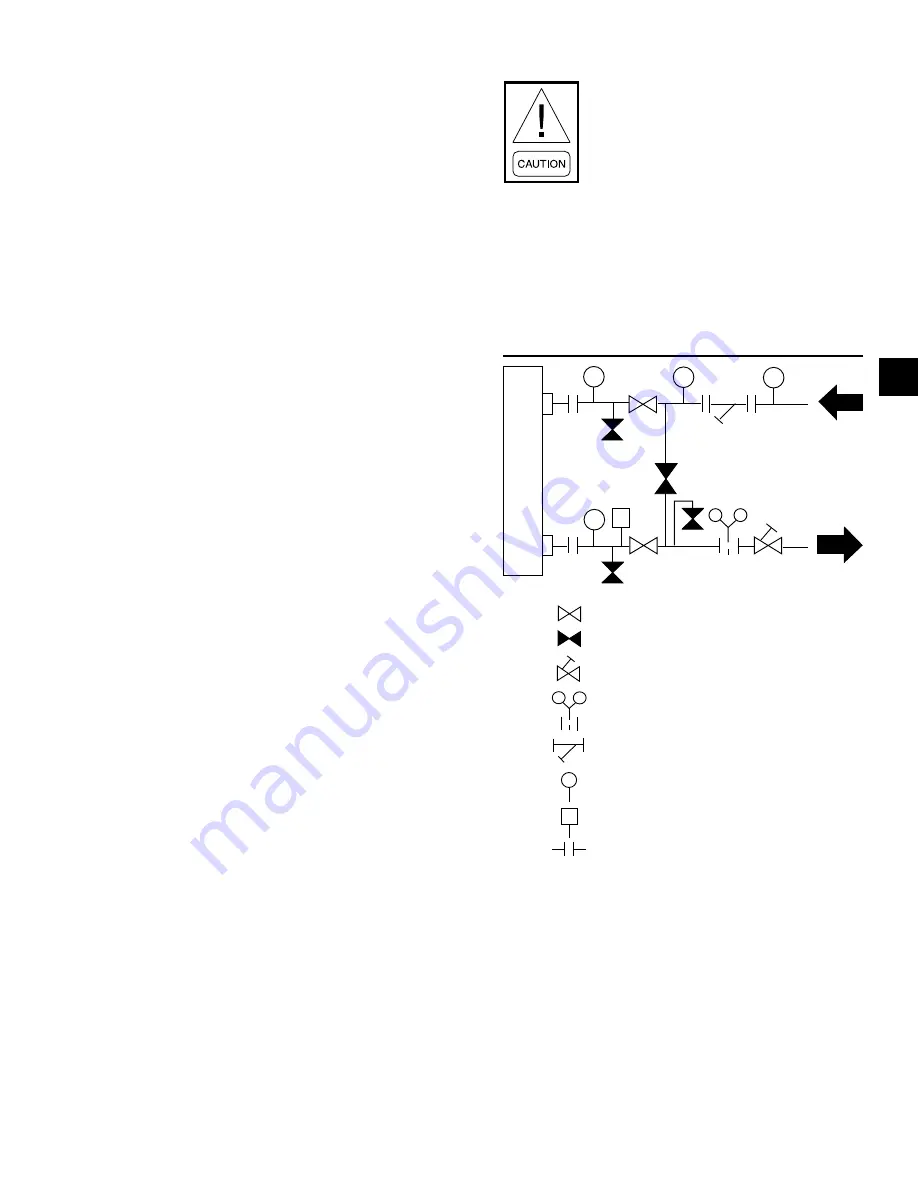
FORM 150.72-NM1 (1020)
41
JOHNSON CONTROLS
4
The piping to and from the cooler must be designed to
suit the individual installation. It is important that the
following considerations be observed:
1. The chilled liquid piping system should be laid out
so that the circulating pump discharges directly
into the cooler. The suction for this pump should
be taken from the piping system return line and not
the cooler. This piping scheme is recommended,
but is not mandatory.
2. The inlet and outlet cooler connection sizes are
provided in Table 4 (Physical Data).
3. A strainer, preferably 40 mesh, must be installed in
the cooler inlet line just ahead of the cooler. This
is important to protect the cooler from entrance of
large particles which could cause damage to the
evaporator.
4. All chilled liquid piping should be thoroughly
flushed to free it from foreign material before
the system is placed into operation. Use care not
to flush any foreign material into or through the
cooler.
5. As an aid to servicing, thermometers and pressure
gauges should be installed in the inlet and outlet
water lines.
6. The chilled water lines that are exposed to outdoor
ambients should be wrapped with supplemental
heater cable and insulated to protect against freeze-
up during low ambient periods, and to prevent
formation of condensation on lines in warm humid
locations. As an alternative, ethylene glycol should
be added to protect against freeze-up during low
ambient periods.
7. A chilled water flow switch, (either by YORK or
others) MUST be installed in the leaving water
piping of the cooler. There should be a straight
horizontal run of at least 5 diameters on each side
of the switch. Adjust the flow switch paddle to the
size of the pipe in which it is to be installed (see
manufacturer’s instructions furnished with the
switch). The switch is to be wired to Terminals
13 – 14 of XTBC1 located in the control panel, as
shown on the unit wiring diagram.
The Flow Switch MUST NOT be used
to start and stop the chiller (i.e. start
-
ing and stopping the chilled water
pump). It is intended only as a safety
switch.
PIPEWORK ARRANGEMENT
The following are suggested pipework arrangements for
single unit installations, for multiple unit installations,
each unit should be piped as shown.
RECOMMENDATIONS OF THE BUILDING
SERVICES RESEARCH ASSOCIATION.
FIG. 8 – CHILLED LIQUID SYSTEM
LD06597
LD06596
ISOLATING VALVE - NORMALLY OPEN
ISOLATING VALVE - NORMALLY CLOSED
FLOW REGULATING VALVE
FLOW MEASUREMENT DEVICE
STRAINER
PRESSURE TAPPING
FLOW SWITCH
FLANGED CONNECTION
FLOW MEASUREMENT DEVICE
STRAINER
PRESSURE TAPPING
FLOW SWITCH
FLANGED CONNECTI0N
FLOW REGULATING VALVE
ISOLATING VALVE - NORMALLY OPEN
ISOLATING VALVE - NORMALLY CLOSED
Summary of Contents for YORK Tempo YLAA Series
Page 4: ...JOHNSON CONTROLS 4 FORM 150 72 NM1 1020 THIS PAGE INTENTIONALLY LEFT BLANK...
Page 12: ...JOHNSON CONTROLS 12 FORM 150 72 NM1 1020 THIS PAGE INTENTIONALLY LEFT BLANK...
Page 14: ...JOHNSON CONTROLS 14 FORM 150 72 NM1 1020 THIS PAGE INTENTIONALLY LEFT BLANK...
Page 18: ...JOHNSON CONTROLS 18 FORM 150 72 NM1 1020 THIS PAGE INTENTIONALLY LEFT BLANK...
Page 36: ...JOHNSON CONTROLS 36 FORM 150 72 NM1 1020 THIS PAGE INTENTIONALLY LEFT BLANK...
Page 49: ...FORM 150 72 NM1 1020 49 JOHNSON CONTROLS THIS PAGE INTENTIONALLY LEFT BLANK...
Page 71: ...FORM 150 72 NM1 1020 71 JOHNSON CONTROLS THIS PAGE INTENTIONALLY LEFT BLANK...
Page 73: ...FORM 150 72 NM1 1020 73 JOHNSON CONTROLS 5 5...
Page 75: ...FORM 150 72 NM1 1020 75 JOHNSON CONTROLS 5 5...
Page 77: ...FORM 150 72 NM1 1020 77 JOHNSON CONTROLS 5 5...
Page 79: ...FORM 150 72 NM1 1020 79 JOHNSON CONTROLS 5 5...
Page 81: ...FORM 150 72 NM1 1020 81 JOHNSON CONTROLS 5 5...
Page 83: ...FORM 150 72 NM1 1020 83 JOHNSON CONTROLS 5 5...
Page 85: ...FORM 150 72 NM1 1020 85 JOHNSON CONTROLS 5 5 LD13901...
Page 87: ...FORM 150 72 NM1 1020 87 JOHNSON CONTROLS 5 5...
Page 89: ...FORM 150 72 NM1 1020 89 JOHNSON CONTROLS 5 5 LD13232...
Page 91: ...FORM 150 72 NM1 1020 91 JOHNSON CONTROLS THIS PAGE INTENTIONALLY LEFT BLANK...
Page 92: ...JOHNSON CONTROLS 92 FORM 150 72 NM1 1020 Technical Data WIRING LD13238 FIG 22 WIRING...
Page 93: ...FORM 150 72 NM1 1020 93 JOHNSON CONTROLS 5 5 LD13239...
Page 176: ...JOHNSON CONTROLS 176 FORM 150 72 NM1 1020 THIS PAGE INTENTIONALLY LEFT BLANK...
Page 191: ...FORM 150 72 NM1 1020 191 JOHNSON CONTROLS 10 NOTES...