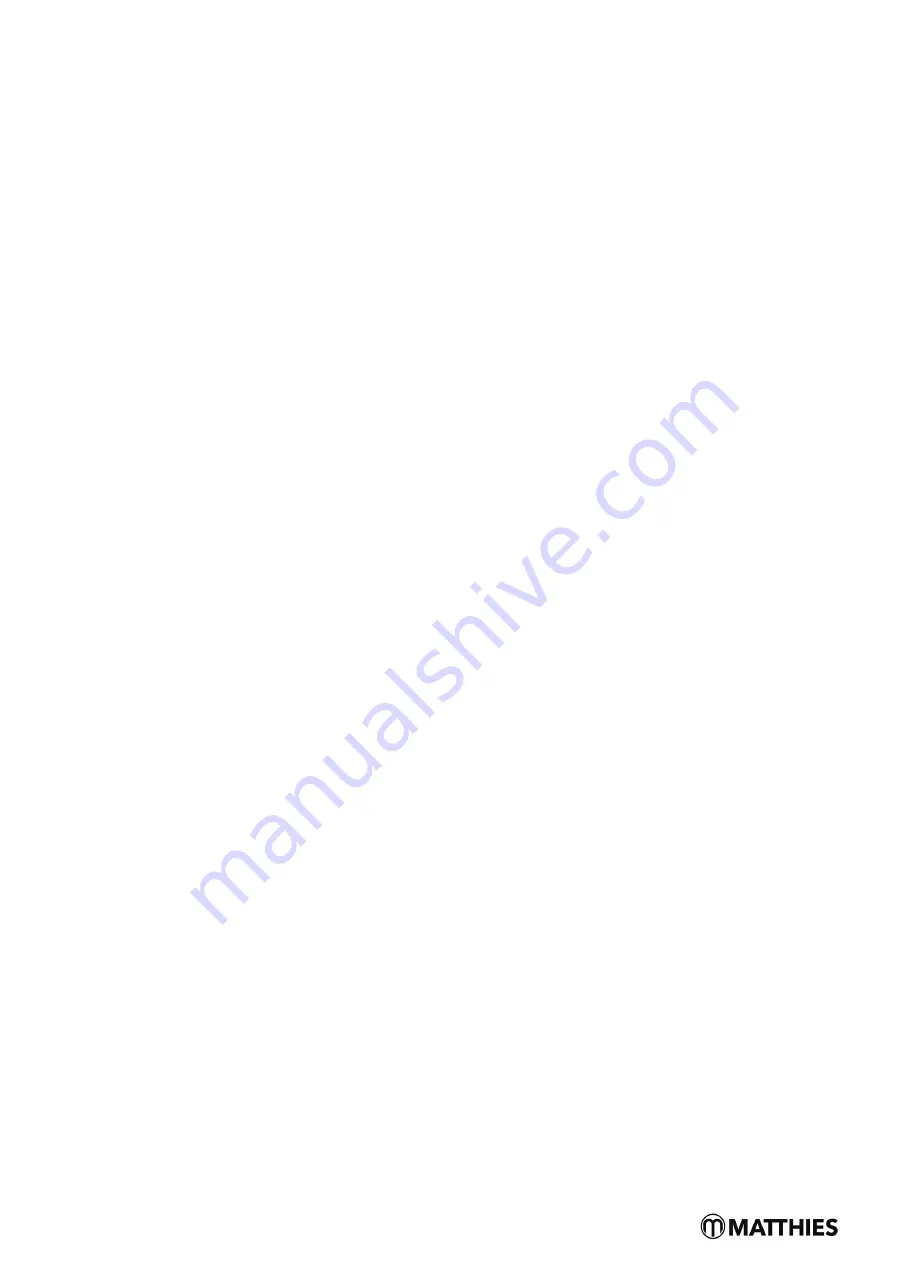
24
12. Installation and commissioning
12.1. Installation guidelines
-
Installation of the lift is realised by trained service technicians of the manufacturer or an authorised dealer. If the
operator has appropriately trained service technicians, he can also realise installation of the lift. Installation is to
be realised pursuant to the installation instructions.
-
The standard lift should not be installed in potentially explosive rooms, an exposed environment or in washing
bays.
-
Verification of an adequate foundation must be obtained or compiled pursuant to the guidelines in the founda-
tion plan prior to installation. The installation site must be perfectly level. Foundations outdoors and in rooms in
which winter weather or frost is to be expected must be primed to freezing depth.
-
3 PE, 400V, 50Hz must be provided on site for the electrical connection. The supply line must be
appropriately secured on site pursuant to VDE0100 with 16 Ampere slow blow fuse protection. The minimum
conductor cross section is 2.5 mm². The connection point is contained in the control unit.
-
All cable bushings must be fitted with cable sleeves or flexible plastic tubing to protect electric cables.
-
Following completion of installation and prior to initial commission, on-site (operator) inspection of the lift pro-
tective conductor must be conducted pursuant to IEC directives (60364-6-61). An insulation resistance test is
also recommended.
-
Following completion of installation, a safety sticker must be applied in a visible location.
Summary of Contents for FOX 4000 H
Page 11: ...9 6 3 Data sheets a Standard version with 4090 mm ...
Page 12: ...10 b Lift column extension version with 4690 mm ...
Page 13: ...11 6 4 Load distribution ...
Page 14: ...12 6 5 Foundation plan ...
Page 15: ...13 6 6 Electrical diagram and parts list ...
Page 16: ...14 6 7 Hydraulic diagram and hydraulic parts list ...
Page 32: ...30 12 7 Installation of covers pipe clips and hydraulic line ...
Page 33: ...31 ...
Page 34: ...32 Ensure that hydraulic hoses F G and I are firmly connected and no leaks are evident ...
Page 37: ...35 12 10 Installation of limit switch ...
Page 41: ...39 B Safety catch A Cable from control cabinet B Safety catch cable ...
Page 42: ...40 C Shut off bar C Cable from control cabinet D Safety catch cable ...
Page 44: ...42 E Pump unit A Limit switch cable B Column extension cable bushing ...
Page 45: ...43 A Limit switch cable C Cable sleeve Clamp 102 Clamp 111 ...
Page 49: ...47 12 16 Dowel data sheet ...
Page 62: ...60 16 CE Confirmation ...