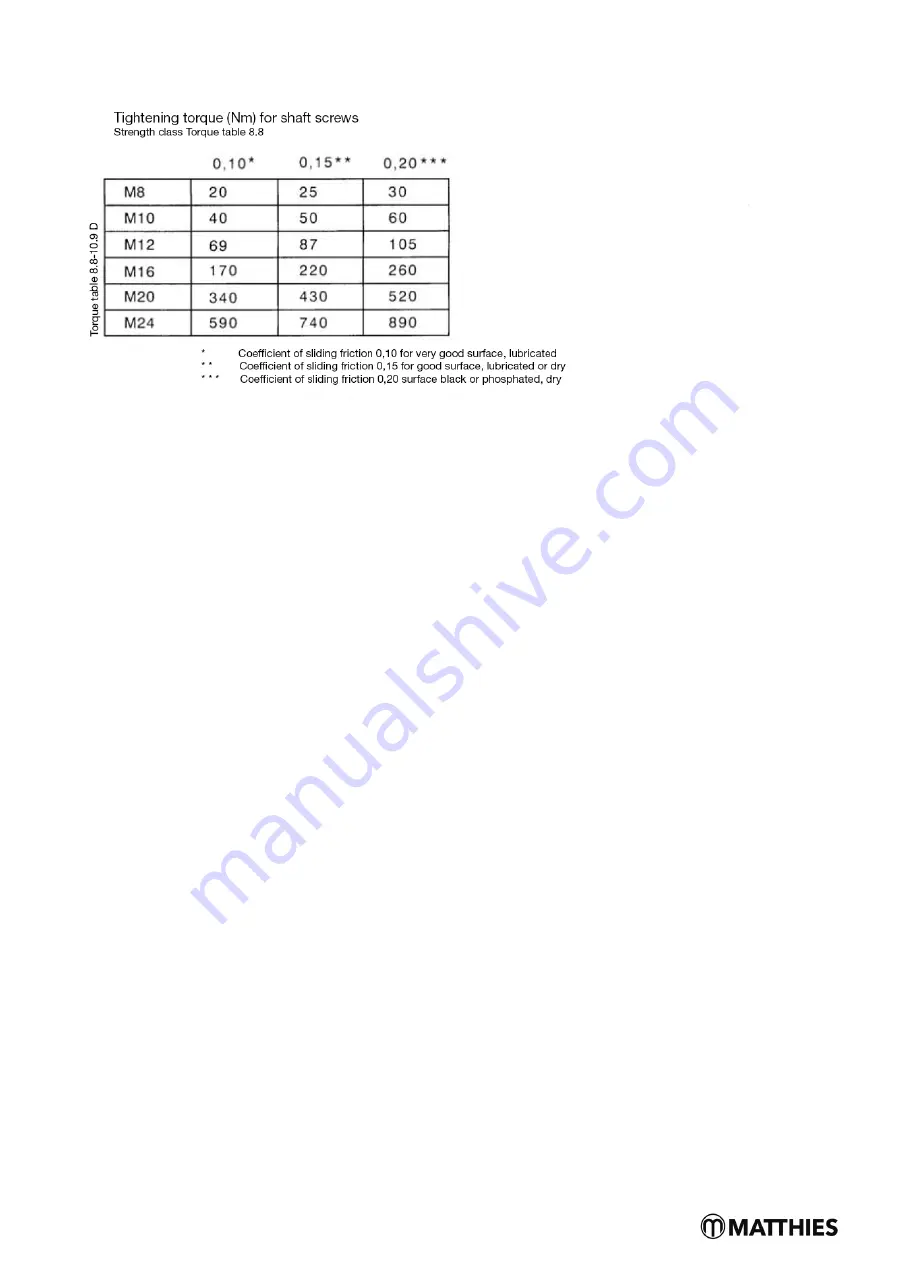
21
-
Visually inspect all welds. Shut down the lift and contact your dealer if any cracks or breakages are detected in welds.
-
Check steel synchronisation cables for damage. Replace the complete cable set if cable breakages are detected.
-
Clean pin and bearing points, rollers and running surfaces for rollers and check for wear. Replace if necessary.
-
Check all hydraulic screw fittings for leaks.
-
Check hydraulic oil level and, if necessary, fill up with clean oil with a viscosity of HLP 32 or replace comple-
tely with new oil (1 litre container JM No. 558.49.41). The hydraulic oil should be between the upper and lower
marking on the oil dipstick after filling.
-
Check powder coating and repair if necessary. Treat damage caused by outside influences immediately after
detection. Infiltration of deposits of all kinds can cause extensive and permanent damage to the powder
coating if areas are not treated. Rust occurs due to mechanical damage, wear, aggressive deposits (road salt,
leaking operational fluids), inadequate or unrealised cleaning. These areas must be sanded lightly (120 grit),
cleaned and freed from grease. Then rework with appropriate repair paint (observe RAL no. 7016).
-
Check all safety equipment (support arm locking system, shut-off bar, circuit breaker, foot deflector, safety
plates on support arm, etc.).
-
Check electrical cables and their cable ducts for damage.
-
Hydraulic hose lines: Hose lines should be replaced every 6 years (operating duration including max. 2 years
storage duration) under normal circumstances. The recommended replacement interval is 2 years under incre-
ased operating conditions (e.g. multiple shifts, shorter cycle times and pressure pulses, severe inner and outer
influences that sharply reduce the duration of use).
Needs-based work:
-
Free the lifting cylinder piston rods of sand and dirt with compressed air. Moisten the piston rods lightly with
acid-free oil.
-
Clean the lifting cylinder wipers and check for damage.
-
Grease moving parts.
Summary of Contents for FOX 4000 H
Page 11: ...9 6 3 Data sheets a Standard version with 4090 mm ...
Page 12: ...10 b Lift column extension version with 4690 mm ...
Page 13: ...11 6 4 Load distribution ...
Page 14: ...12 6 5 Foundation plan ...
Page 15: ...13 6 6 Electrical diagram and parts list ...
Page 16: ...14 6 7 Hydraulic diagram and hydraulic parts list ...
Page 32: ...30 12 7 Installation of covers pipe clips and hydraulic line ...
Page 33: ...31 ...
Page 34: ...32 Ensure that hydraulic hoses F G and I are firmly connected and no leaks are evident ...
Page 37: ...35 12 10 Installation of limit switch ...
Page 41: ...39 B Safety catch A Cable from control cabinet B Safety catch cable ...
Page 42: ...40 C Shut off bar C Cable from control cabinet D Safety catch cable ...
Page 44: ...42 E Pump unit A Limit switch cable B Column extension cable bushing ...
Page 45: ...43 A Limit switch cable C Cable sleeve Clamp 102 Clamp 111 ...
Page 49: ...47 12 16 Dowel data sheet ...
Page 62: ...60 16 CE Confirmation ...