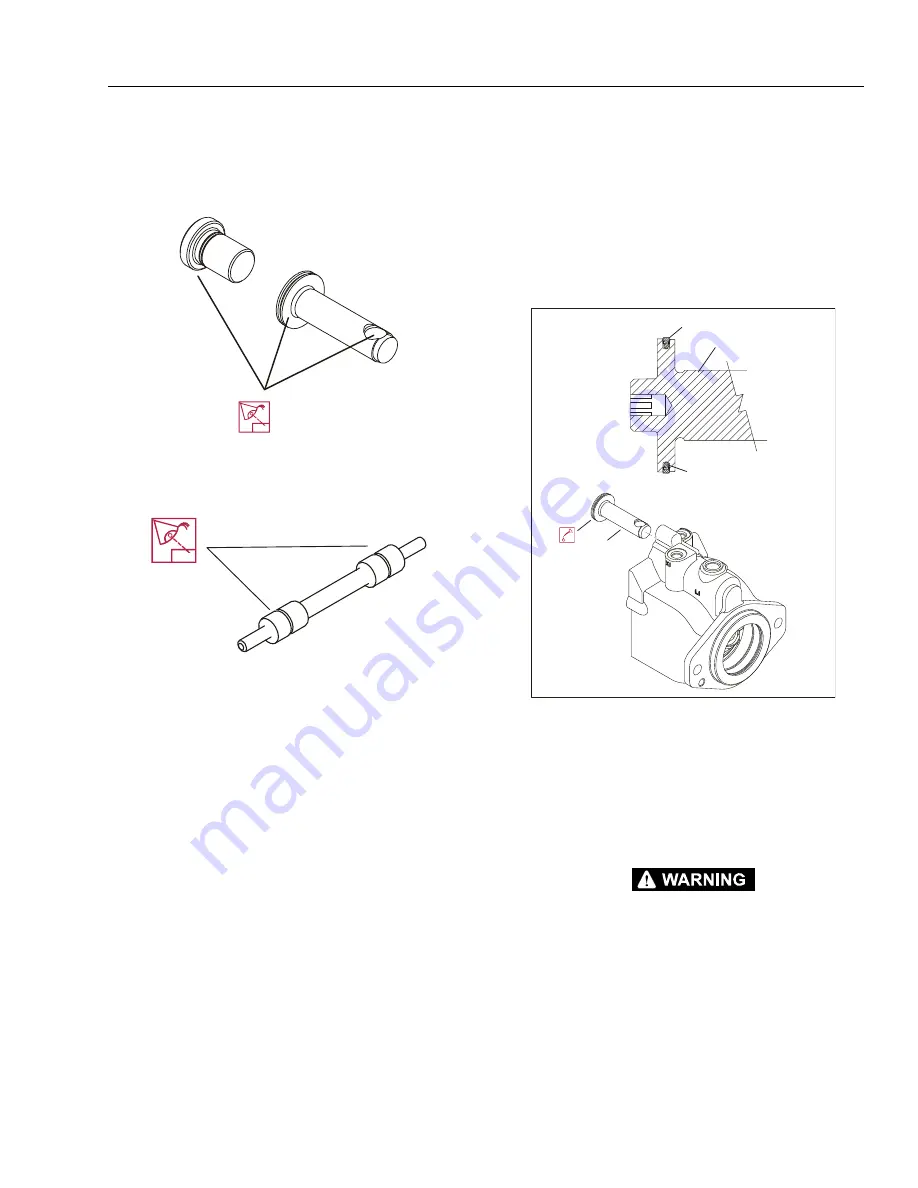
SECTION 3 - CHASSIS, PLATFORM & SCISSOR ARMS
3121781
3-29
SERVO PISTON AND MINIMUM ANGLE STOP
Inspect the minimum angle stop, servo piston head, and
servo piston ball-socket for damage or excessive wear.
Replace if necessary.
LOOP FLUSHING SPOOL
Inspect the loop flushing spool. Check for cracks or
damage. Replace if necessary.
Assembly
1. Install new O-ring (1) and piston seal (2) to the servo
piston (3). Install the piston seal over the O-ring.
Installing the piston seal stretches it, making it diffi-
cult to install the servo piston in its bore. Allow 30
minutes for the seal to relax after installation. To
speed up seal relaxation, compress the seal by install-
ing the piston head into the servo cavity in the end-
cap and let it stand for at least five minutes.
2. After piston seal has relaxed, lubricate and install
servo piston into the housing bore. Align the piston
with the ball socket facing the inside of the housing.
RISK OF PERSONAL INJURY: COMPRESSING THE BLOCK SPRING
REQUIRES ABOUT 80 TO 90 LBF (350 TO 400 N) OF FORCE. USE A
PRESS SUFFICIENT TO MAINTAIN THIS FORCE WITH REASONABLE
EFFORT. ENSURE THE SPRING IS SECURE BEFORE ATTEMPTING TO
INSTALL THE SPIRAL RETAINING RING. RELEASE THE PRESSURE
SLOWLY AFTER THE RETAINING RING IS INSTALLED.
3
2
1
3
1.
O-ring
2.
Piston Seal
3.
Servo Piston
Figure 3-17. Servo Piston
Summary of Contents for 530LRT
Page 2: ......
Page 4: ...INTRODUCTION b 3121781 REVISION LOG Original Issue A September 03 2018...
Page 14: ...x 3121781 TABLE OF CONTENTS This page left blank intentionally...
Page 26: ...SECTION 1 SPECIFICATIONS 1 10 3121781 Figure 1 6 Torque Chart Sheet 2 of 5 SAE Fasteners...
Page 27: ...SECTION 1 SPECIFICATIONS 3121781 1 11 Figure 1 7 Torque Chart Sheet 3 of 5 SAE Fasteners...
Page 28: ...SECTION 1 SPECIFICATIONS 1 12 3121781 Figure 1 8 Torque Chart Sheet 4 of 5 METRIC Fasteners...
Page 29: ...SECTION 1 SPECIFICATIONS 3121781 1 13 Figure 1 9 Torque Chart Sheet 5 of 5 METRIC Fasteners...
Page 30: ...SECTION 1 SPECIFICATIONS 1 14 3121781 NOTES...
Page 110: ...SECTION 3 CHASSIS PLATFORM SCISSOR ARMS 3 68 3121781 NOTES...
Page 261: ......