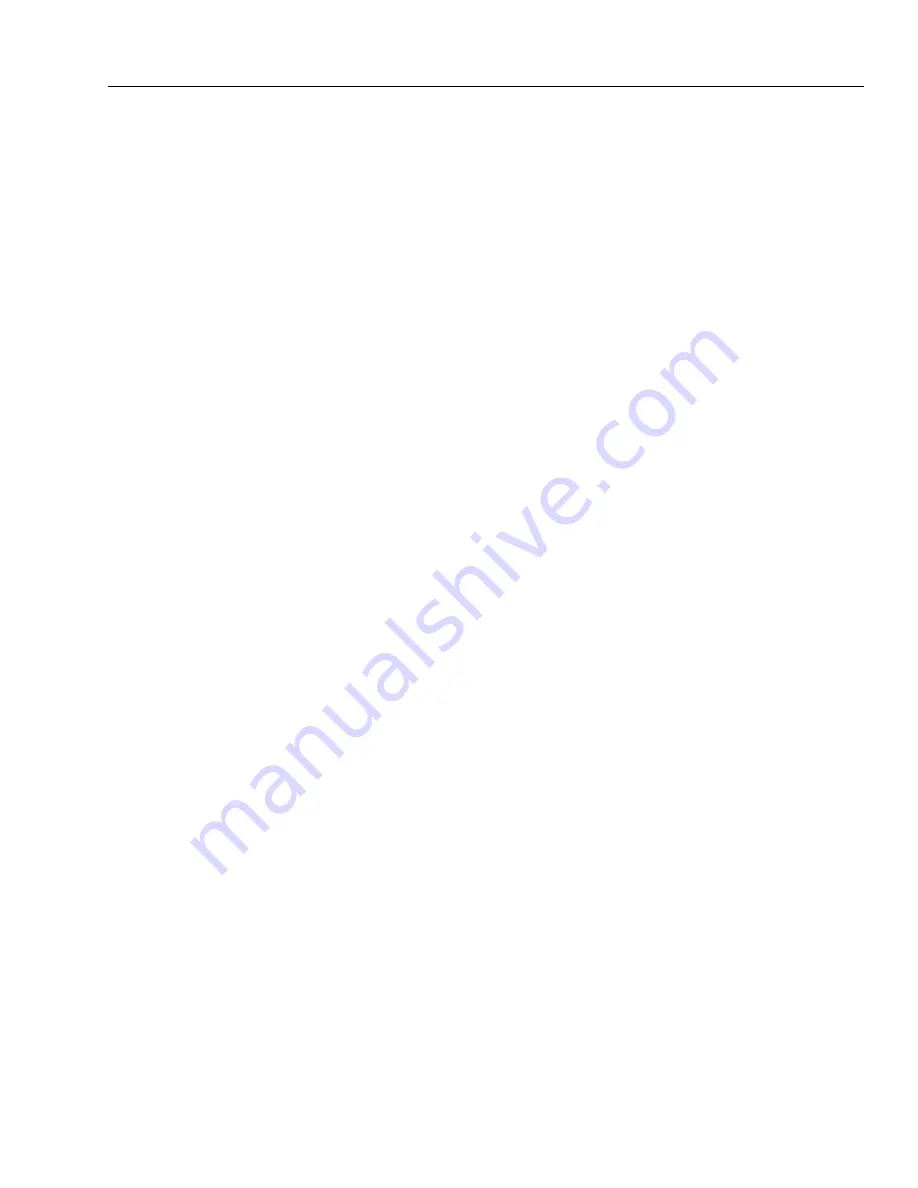
SECTION 3 - CHASSIS, PLATFORM & SCISSOR ARMS
3121781
3-1
SECTION 3. CHASSIS, PLATFORM & SCISSOR ARMS
3.1
OPERATING CHARACTERISTICS
Leveling Jacks
The machine is equipped with auto leveling jacks. These
leveling jacks are operated through one switch unlike
the traditional four switch system. The leveling jacks are
operated by a bang bang valve.
1. Activate the leveling jack button located on the plat-
form control box.
2. Extend the jacks by moving the joystick forward.
NOTE:
Once all four jacks make contact with the ground the
system will go from set mode into level mode. At this
point the engine will return to idle.
3. The tilt indicator will go out once the machine is
level.
NOTE:
If the machine is not level it will not lift. If you hit the
end of stroke on any of the cylinders you cannot lift
the machine.
NOTE:
There is a limit switch on each cylinder that senses
when the cylinder is fully retracted when all four are
fully retracted, the stowed light in the platform con-
trol box will light.
If you receive a 2/5 flash code through the system
fault light at the platform control station the
machine is unable to level. You must reposition and
try again.
The jacks are operational (extend or retract) if the
machine is in the stowed position. The armstack angle
tilt sensor and rotary sensor together must sense that
the machine is stowed. A failure of either sensor will pre-
vent the jacks from being activated.
Generator
When the generator switch is activated, the engine RPM
will increase to high idle.
When a function is selected for operation, which
requires a higher engine speed than the generator, the
generator will automatically shut off during the opera-
tion of the function. Once the function has stopped, the
generator will be active again.
Lift
A proportional flow control valve allows for propor-
tional control of the lift up function. Proportional valves
on both the upper and lower cylinders allow for smooth
control of the lift down function.
Drive
If driving at high drive up a grade and you hit an 8°
incline, the drive function will cut back to mid drive
speed. The drive pump will shift back into high drive
once the incline decreases to 5°. There will be a 2 second
delay before the machine goes back into high drive.
3.2
TIRES, WHEELS & DRIVE ASSEMBLY
Tire Inflation
The air pressure for pneumatic tires must be equal to
the air pressure that is stenciled on the side of the JLG
product or rim decal for safe and proper operational
characteristics.
Tire Damage
For pneumatic tires, JLG Industries, Inc. recommends
that when any cut, rip, or tear is discovered that exposes
sidewall or tread area cords in the tire, measures must
be taken to remove the JLG product from service imme-
diately. Arrangements must be made for replacement of
the tire or tire assembly.
For polyurethane foam filled tires, JLG Industries, Inc.
recommends that when any of the following are discov-
ered, measures must be taken to remove the JLG prod-
uct from service immediately and arrangements must
be made for replacement of the tire or tire assembly.
• a smooth, even cut through the cord plies which
exceeds 3 inches (7.5 cm) in total length
• any tears or rips (ragged edges) in the cord plies
which exceeds 1 inch (2.5 cm) in any direction
• any punctures which exceed 1 inch in diameter
• any damage to the bead area cords of the tire
If a tire is damaged but is within the above noted crite-
ria, the tire must be inspected on a daily basis to ensure
the damage has not propagated beyond the allowable
criteria.
Tire Replacement
JLG recommends a replacement tire be the same size,
ply and brand as originally installed on the machine.
Please refer to the JLG Parts Manual for the part number
Summary of Contents for 530LRT
Page 2: ......
Page 4: ...INTRODUCTION b 3121781 REVISION LOG Original Issue A September 03 2018...
Page 14: ...x 3121781 TABLE OF CONTENTS This page left blank intentionally...
Page 26: ...SECTION 1 SPECIFICATIONS 1 10 3121781 Figure 1 6 Torque Chart Sheet 2 of 5 SAE Fasteners...
Page 27: ...SECTION 1 SPECIFICATIONS 3121781 1 11 Figure 1 7 Torque Chart Sheet 3 of 5 SAE Fasteners...
Page 28: ...SECTION 1 SPECIFICATIONS 1 12 3121781 Figure 1 8 Torque Chart Sheet 4 of 5 METRIC Fasteners...
Page 29: ...SECTION 1 SPECIFICATIONS 3121781 1 13 Figure 1 9 Torque Chart Sheet 5 of 5 METRIC Fasteners...
Page 30: ...SECTION 1 SPECIFICATIONS 1 14 3121781 NOTES...
Page 110: ...SECTION 3 CHASSIS PLATFORM SCISSOR ARMS 3 68 3121781 NOTES...
Page 261: ......