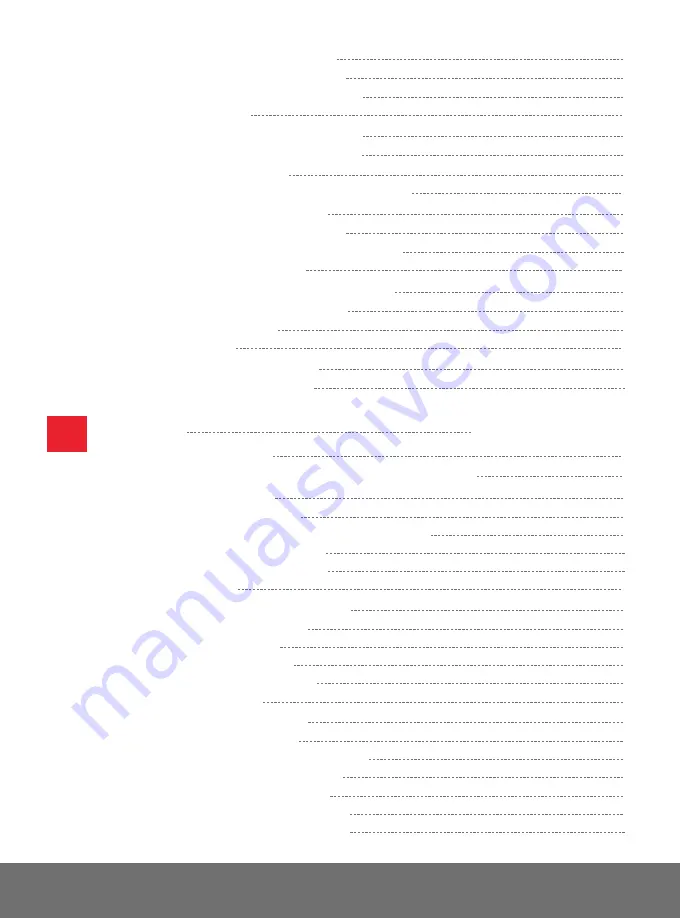
PAGE v of vi
EB0162 Rev 00
5.5.3. Positioning the Detector
32
5.5.4. Adjusting Detector Height
33
5.5.5. Adjusting the Detector Angle
33
5.6. Source Cart
34
5.6.1. Releasing the Mounting Plate
34
5.6.2. Attaching the Mounting Plate
34
5.6.3. Mounting Plate
35
5.7. Connecting Chain & Dovetail Links
36
5.7.1. Connecting Chain Links
36
5.7.2. Disconnecting Chain Links
36
5.7.3. Disconnecting the Red Dovetail Links
37
5.8. Cable Management
38
5.8.1. Cable Management Dovetail Mount
38
5.8.2. Cable Management Setup
38
5.8.3. Clamp Setup
39
5.9. Backpack
40
5.9.1. Mounting a Backpack
40
5.9.2. Using the backpack
41
Chapter
6
Operation
42
6.1. System Startup
42
6.2. Placement of Crawler on Inspection Surface
44
6.2.1. Chain System
44
6.2.2. Magnetic System
49
6.2.2.2 Scanner Installation/Removal Mat Use
49
6.2.2.3 Detector Setup
51
6.2.2.4 Crawler Position
51
6.3. Operation
52
6.3.1. Handheld Controller Layout
52
6.3.1.1 Touchscreen
52
6.3.1.2 D-pad
53
6.3.1.3 Joysticks
53
6.3.2. Mode Select Screen
53
6.3.3. Jog Mode
54
6.3.4. Latched Jog Mode
55
6.3.5. 1 Axis Scan Mode
56
6.3.5.1 1 Axis Scan Setup Screen
56
6.3.5.2 1 Axis Scan Screen
57
6.3.6. System Utilities Screen
59
6.3.6.1 User Settings Screen
60
6.3.6.2 Diagnostics Screens
61