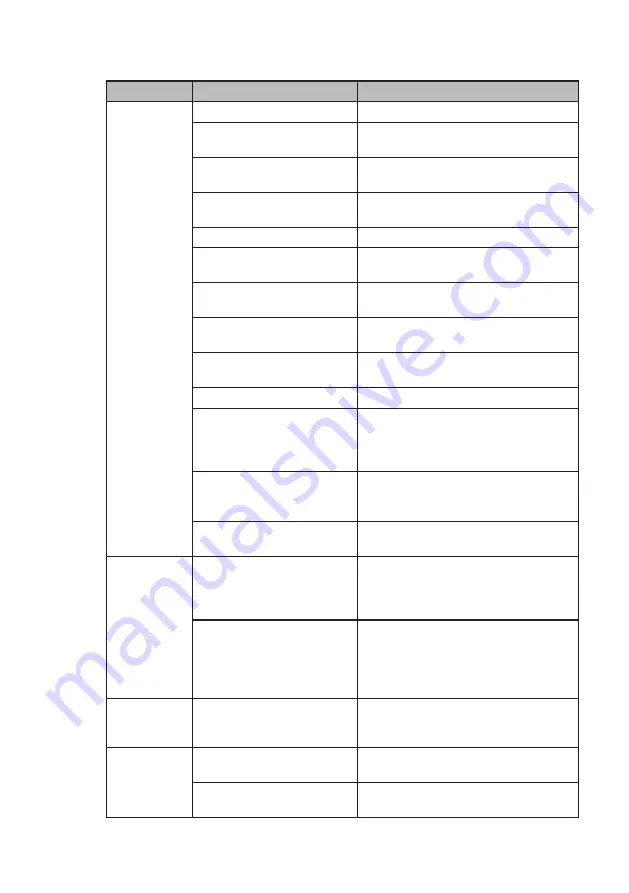
30
| Operation Manual C 2213 | Accessories
10 Troubleshooting
Type of fault
Possible cause
Recommended action
No flow meter
indication or
indicated value
too low.
Chlorine cylinder empty.
Connect new cylinder.
Cylinder valve or auxiliary valve
not open.
Open valves.
Vacuum system is not completely
tight so that ambient air is primed.
Open valves step by step in order to find and
remove untight point.
Changeover unit did not switch to
full cylinder.
Actuate changeover unit by hand and check its
function.
Filter of inlet valve clogged.
Replace filter element.
Floating element in flow meter
clogged.
Dismantle and clean flow meter.
Dirt screen in motive water line
clogged.
Clean and exchange filter.
Solution injection fitting clogged.
Clean solution injection fitting or open the stop
valve.
Ejector performance too low.
Exchange ejector, reduce back pressure or
increase motive water pressure.
Ejector clogged.
Clean ejector.
Carbonate precipitations in ejector.
Remove precipitations (e.g.10% hydrochloric
acid approx. 5 min.). If possible, set higher chlo-
rine concentration (1..2 g/l) and reduce, motive
water pressure, if necessary.
High back pressure at ejector
resulting from incorrect running of
solution line.
Optimize solution line, avoid sharp bends and
cross-sectional contractions (possibly caused by
excessive cement.)
Vacuum lines too small.
Use larger vacuum lines or increase ejector
priming output.
Chlorine smell or
chlorine alarm
Leaking overpressure system.
Close chlorine cylinder immediately (using .pro-
tecting mask) and evacuate lines using ejector.
Look for leaking points as described in section
LEAKAGE TEST.
Safety valve bleeds off in the case
of overpressure resulting from
clogged inlet valve.
Maintain inlet and safety valve as described in
section MAINTENANCE and exchange loaded ac-
tivated carbon if necessary. If there are heavy dirt
deposits in inlet valve, check chlorine gas purity
and provide for room heating (approx. 20°C).
White deposits in
flow meter.
Vacuum system is leaky and air
humidity condenses forming white
fog.
Look for untight spots and remove them.
Otherwise incrustations will be formed affecting
valve functions.
Water in vacuum
system.
Ejector nonreturn valve untight
because defective or clogged.
Maintain ejector nonreturn valve, install back-
stop.
End of blowoff line under water and
safety valve untight.
Maintain safety valve and pull out end of blowoff
line of the water.