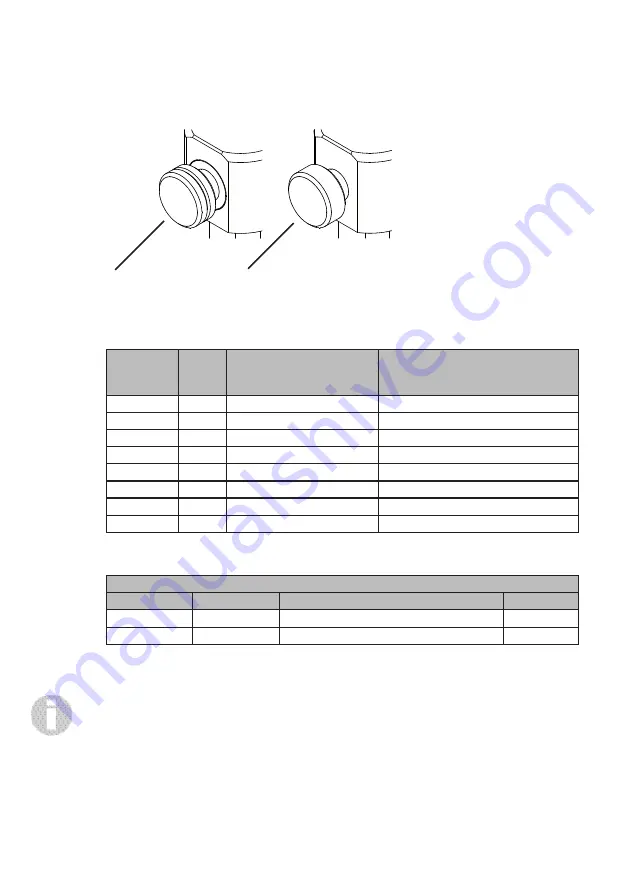
34
| Operation Manual C 2213 | Maintenance kits
Due to the large number of combination possibilities of flow meters, twofold and threefold flow meters are
combined from: 2-3 single flow meters, mounting kit, mounting plate and mounting material. Please specify the
required measuring ranges when ordering.
The adjustment valves and the valve seats in the flow meter housing differ for each model / flow capacity. The
adjustment valves and the flow meter housings are marked respectively.
①
②
Fig. 25: Identification of the flow capacity on the adjustment valves:
①
: 2 notchs at max 80 g/h,
②
: 1 notch at max 500 g/h,
②
: no notch at max 4 kg/h,
Measuring
range
g CI
2
/h
Quantity
Notchs
1 flow meter
for stand alone mounting,
incl. mounting plate
1 flow meter
for use in a manifold flow meter, wit-
hout mounting plate
1 ... 25
2
25100001
25100009
4 ... 80
2
25100002
25100010
10 ... 200
1
25100003
25100011
25 ... 500
1
25100004
25100012
50 ...1000
0
25100005
25100013
100 ...2000
0
25100006
25100014
125 ...2500
0
25100007
25100015
200 ...4000
0
25100008
25100016
Tab.: 5: Flow meter
Mounting set for manifold flow meter, incl. mounting plate and mounting material
Model
Dim. A
Dim. B
Part.-No.
2-fold
152 mm
120 mm
33375
3-fold
202 mm
170 mm
33376
Tab.: 6: Mounting sets for manifold flow meter
Measuring glasses for larger metering capacities are also available.
NOTICE!
If the chlorine gas flow is to be adjusted remotely in an automatic control system, a chlorine control valve is
integrated in the vacuum line between measuring glass and back-pressure regulator. If the chlorination instal-
lation is to correspond to the German standard DIN 19606, a back-pressure regulator must be used, which
avoids pressure fluctuations in the system. This back-pressure regulator is integrated in the non-return valve.