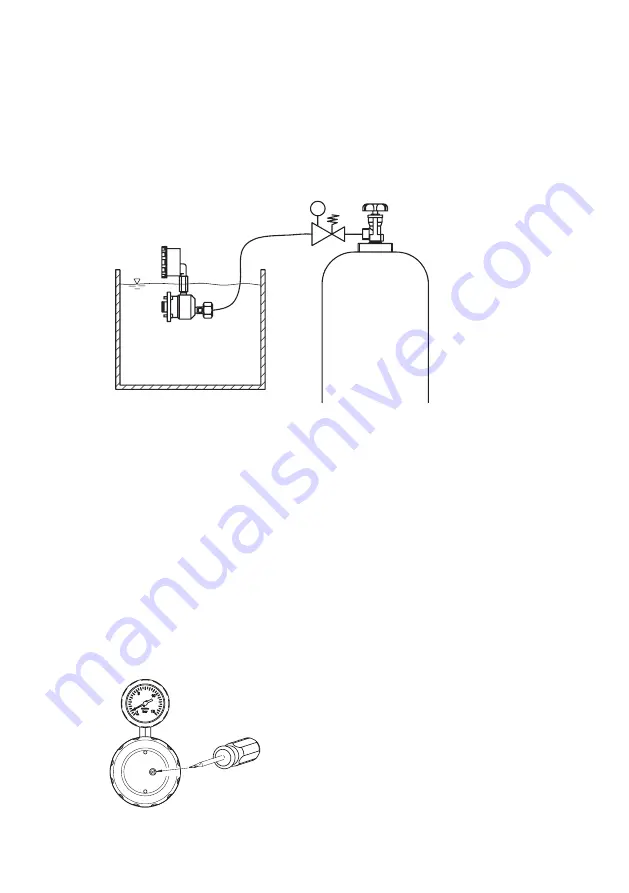
26
| Operation Manual C 2213 | Troubleshooting
9.2 Check
9.2.1 Inlet valve check
The inlet valve is the main safety component of the whole chlorination plant. That's why it has to be checked
particularly carefully. For the check you need dry and oil-free compressed air or nitrogen. Using an edgeless
object (e.g.a biro without reservoir) press in the ball of the inlet valve and then let it off in order to make sure
that it is properly seated. Connect the inlet valve using a hose to the compressed air and immerse it in water.
Do not immerse the pressure gauge!
N2
PI
Fig. 17: Checking the inlet valve
Neither at high pressures (e.g. 16 bar) nor at low pressures (e.g. 0.5 bar) bubbles must rise. After the check
the inlet valve is dried thoroughly and then inserted into the vacuum part by turning it slightly. The O-ring has
to be lubricated with silicone grease. The four screws for fixing the inlet valve are also exchanged, greased with
fitting grease or sprayed with Teflon and tightened slightly.
9.2.2 Checking the complete vacuum regulator
The whole vacuum regulator must be checked on vacuum tightness. For this purpose the vacuum regulator has
to be mounted to the wall holder or the closed chlorine cylinder. Shortly after switching on the ejector the flow
meter must indicate zero.
9.3 Adjustment of simultaneous delivery
Simultaneous delivery should only be set if it is really used. If not the adjustment screw should be unscrewed
until the screw head extends into the housing approx. 3mm.
Fig. 18:
Adjustment of simultaneous delivery