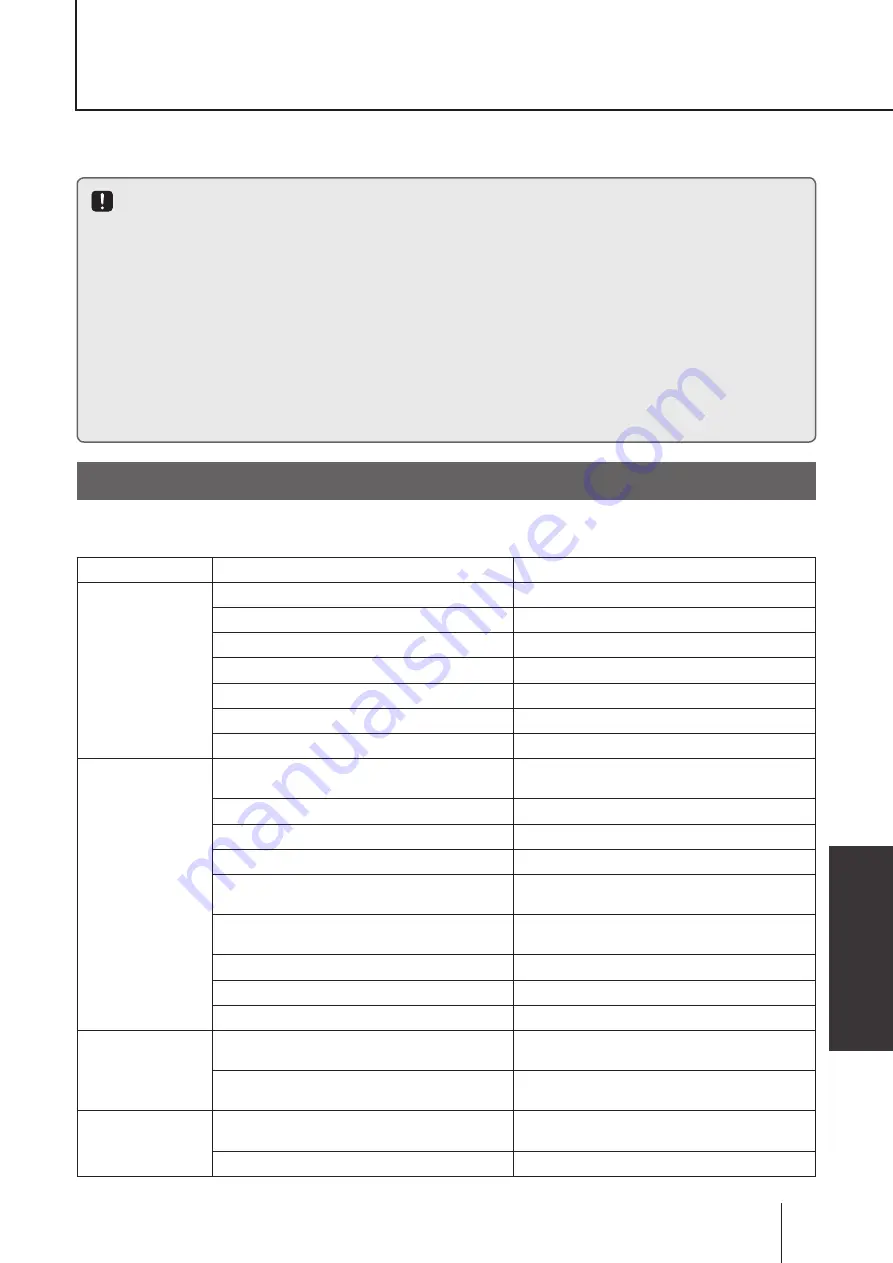
27
M
a
int
ena
n
c
e
Troubleshooting
Maintenance
This section describes troubleshooting, maintenance, wear part replace-
ment, exploded views and specifications.
Points to be observed
Observe the following points during maintenance work:
•
Follow instructions in this manual for replacement of wear parts. Do not disassemble the
pump beyond the extent of the instructions.
•
Always wear protective clothing such as an eye protection, chemical resistant gloves, a
mask and a face shield during disassembly, assembly or maintenance work.
• Risk of electrical shock. Be sure to turn off power to stop the pump and related devices
before/during service is performed. See below.
•
Risk of burning. Do not touch the pump or pipe with bare hands. The surface temperature
of the pump or pipe rises high along with liquid temperature in or right after operation.
Troubleshooting
First check the following points. If the following measures do not help remove problems, con
-
tact your nearest distributor.
States
Possible causes
Solutions
Motor does not
starts to run.
Grid power is directly connected to the motor. Use an inverter. Replace motor if necessary.
Disconnection
Replace/reconnect motor wires as necessary.
Power fuse has blown.
Inspect/solve the root cause of the blowout.
Power voltage reduction
Inspect/solve the root cause of the reduction.
Overpressure (discharge line)
Check a discharge line or check valves.
Out of frequency range.
Observe the allowable frequency. See page 25.
Inverter is not working.
Repair the inverter. Replace as necessary.
Flow is too low.
NPSHr is not satisfied.
Review the pump and piping system to meet
the NPSHr.
A check valve and valve seat have been worn. Replace with new ones.
Foreign matters in the check valve
Take apart and clean the valve.
Clogged suction line or strainer
Take apart and clean them.
Air ingress from the suction line.
Check for loose connections and retighten
as necessary.
Different liquid is used.
Check liquid characteristics and pump spec-
ification.
A relief valve is open.
Check/reset the set pressure.
Damaged diaphragm
Replace with new one.
Damaged gaskets or O rings
Replace with new ones.
Flow is too high.
Minimal differential pressure of 0.03MPa is
not kept and overfeeding results.
Keep the minimal differential pressure. Use
a back pressure valve as necessary.
Different liquid is used.
Check liquid characteristics and pump spec-
ification.
Flow fluctuates.
NPSHr is not satisfied.
Review the pump and piping system to meet
the NPSHr.
A check valve and valve seat have been worn. Replace with new ones.