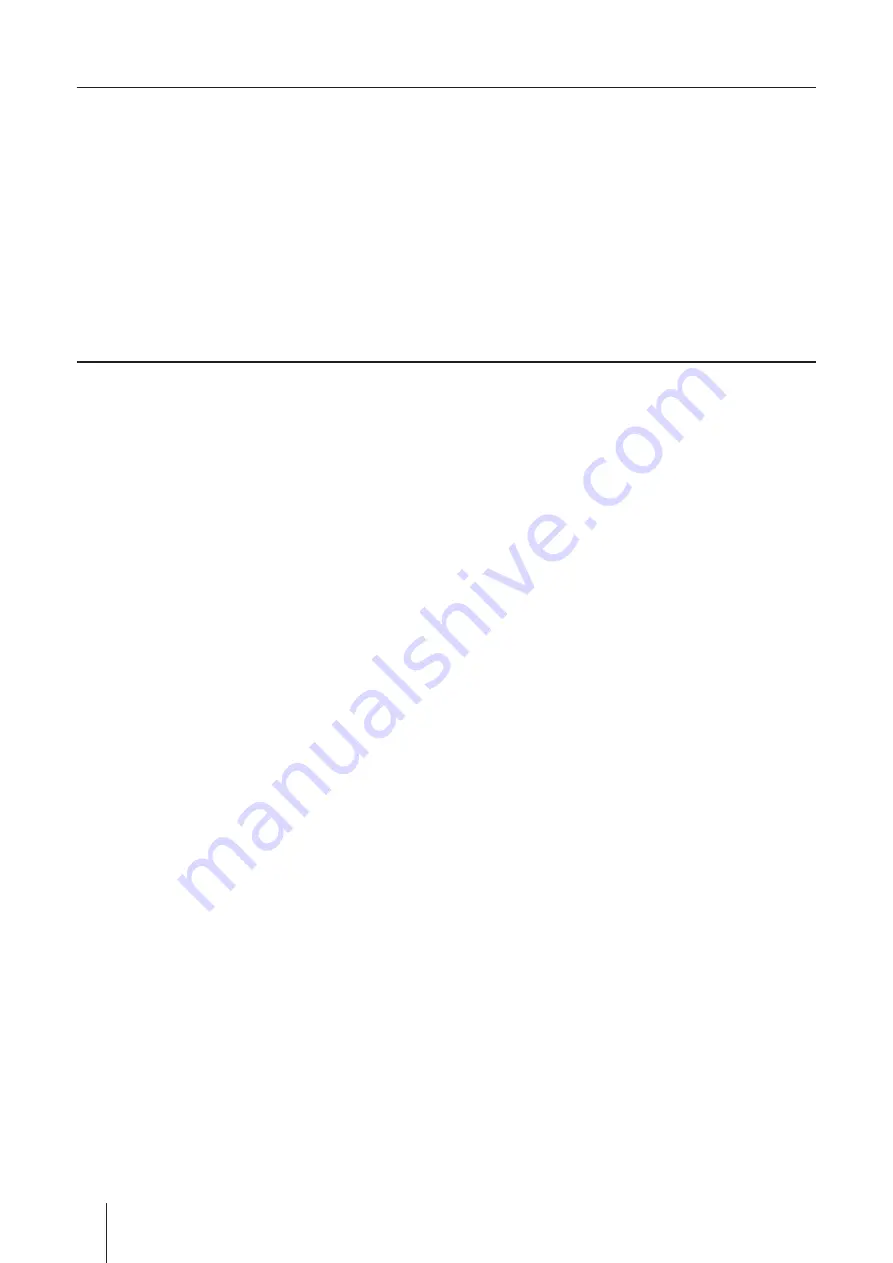
26
Operation
Before stoppage
• After everyday operation,
release the liquid and pressure from the pump and pipework and turn off power.
• Before a
long period of stoppage, flush the inside of the pump and pipework with clean water or cleaning liq-
uid. Completely drain and depressurize them afterwards.
• Frozen liquid may damage the pump and piping. Remove liquid completely in winter.
•
Band heaters can be used to keep the pump and piping warm when suspending operation just for a short
period of time in winter.
Resumption after a long period of stoppage
When operation is resumed after a long period of stoppage (one week later), do not run the pump without com
-
missioning. Always check a tank liquid level and run the pump according to the starting procedure on page 24.