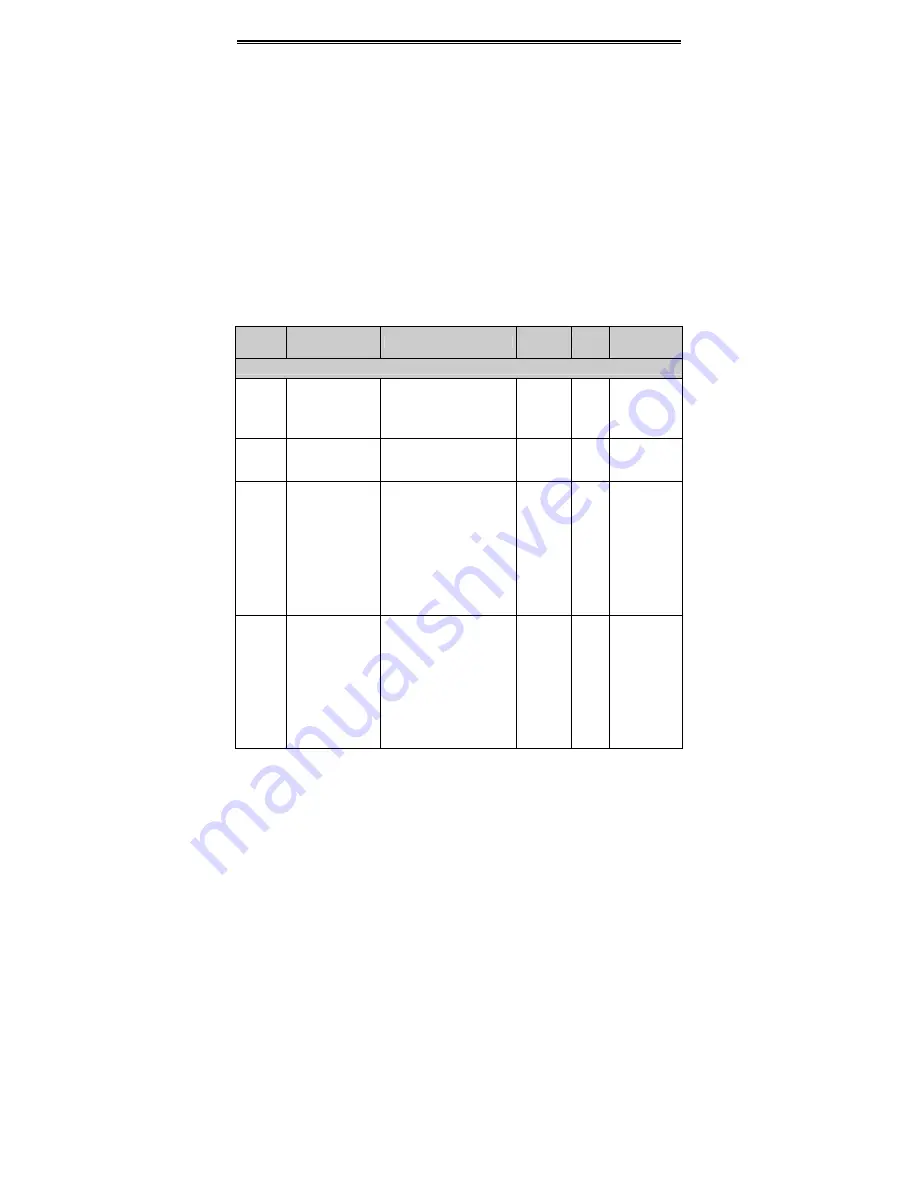
List of Function parameters
109
9. LIST OF FUNCTION PARAMETERS
Notice:
1. PE group is factory reserved, users are forbidden to access these
parameters.
2.
The column “Modify” determines the parameter can be modified or not.
“
○
” indicates that this parameter can be modified all the time.
“
◎
”indicates that this parameter cannot be modified during the inverter is
running.
“
●
” indicates that this parameter is read only.
3.
“Factory Setting” indicates the value of each parameter while restoring the
factory parameters, but those detected parameters or record values cannot be
restored.
Function
Code
Name
Description
Factory
Setting
Modify LCD Display
P0 Group: Basic Function
P0.00
Speed control
mode
0:Sensorless vector control
1:Vector control With PG
2:V/F control
0
◎
CONTROL
MODE
P0.01
Run command
source
0: Keypad
1: Terminal
2: Communication
0
◎
RUN
COMMAND
P0.02
UP/DOWN setting
0: Valid, save UP/DOWN
value when power off
1: Valid, do not save
UP/DOWN value when
power off
2: Invalid
3
:
Valid during running, clear
when power off
0
◎
UP/DOWN
SETTING
P0.03
Frequency A
command source
0: Keypad
1: AI1
2. AI3
3: HDI1
4:Simple PLC
5. Multi-Step speed
6: PID
7: Communication
0
◎
FREQ
SOURCE A