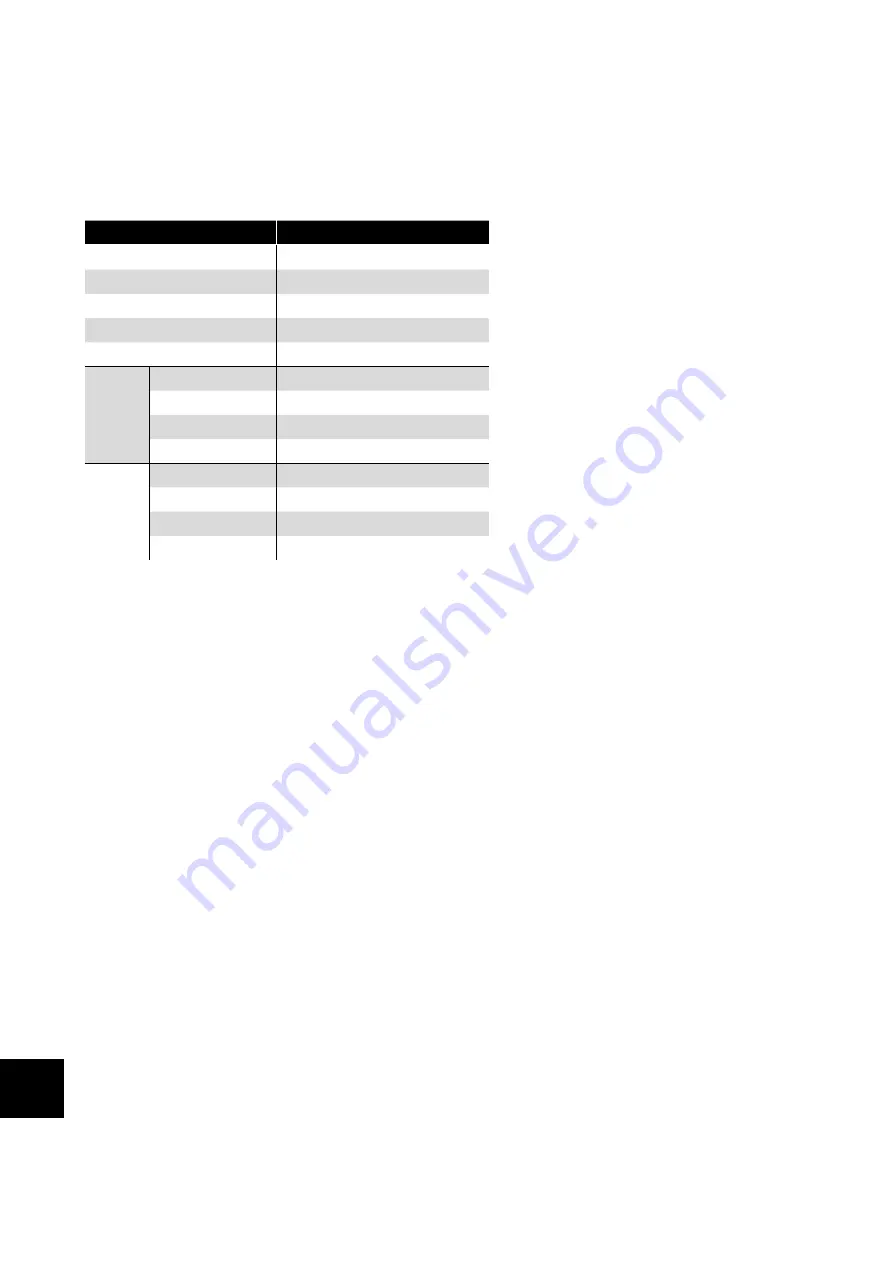
14
| Optidrive ODP-2ETHEG-IN |
Version 1.10
www.invertekdrives.com
6.3.2. Method 2: Class 1 connection via OPC-2-ETHIG-IN ‘Forward Open Assembly’ object
The OPC-2-ETHIG-IN provides the Vendor Class ‘Forward Open Assembly (0x0300)’ which negates the need for the control to
provide the forward open mapping.
For Drive specific allocation refer to Drive Manual and/or Ethernet/IP EDS file.
For Drive specific read/write limitations refer to Drive Manual and/or Ethernet/IP EDS file.
The following connection setting will establish a Class 1 connection to transfer Drive PDI/PDO registers:
Connection setting
Value
Path
21 00 00 03 24 01 2C 01 2C 06
RPI
Min 50ms
Timeout Multiplier
Recommend x32
Trigger
Cyclic
Transport type
Exclusive owner
O->T
Size
8
Connection Type
Point to Point
Length
Fixed
Transfer Format
32bit Run/Idle
T->O
Size
8
Connection Type
Point to Point
Length
Fixed
Transfer Format
Pure data
6.4. Process Data Exchange
All Optidrives support a 4 word input, 4 word output process data exchange to allow control and monitoring of the drive. The
functions and overview of each word are described below.
6.4.1. Process Data Exchange Overview
All Optidrives support a 4 word process data exchange as follows:
PDI: EIP Master
Drive
o Word 1: FIXED: Drive Control Word
o Word 2: FIXED: Frequency/Speed Setpoint
o Word 3
Optidrive E3: FIXED: No Function
Optidrive P2/Eco: USER SELECTED Function determined by P5-14
o Word 4
Optidrive E3: FIXED: Ramp Control (When P-12 = 4 only)
Optidrive P2/Eco: USER SELECTED Function determined by P5-13
PDO: Drive
EIP Master
o Word 1: FIXED: Drive Status
Low Byte: Drive Status Byte
High Byte: Trip Code
o Word 2: FIXED: Output Frequency/Motor Speed
o Word 3
Optidrive E3: FIXED: Output Current
Optidrive P2/Eco: USER SELECTED: Function determined by P5-12
o Word 4
Optidrive E3: FIXED: No Function
Optidrive P2/Eco: USER SELECTED: Function determined by P5-08
Operation
6