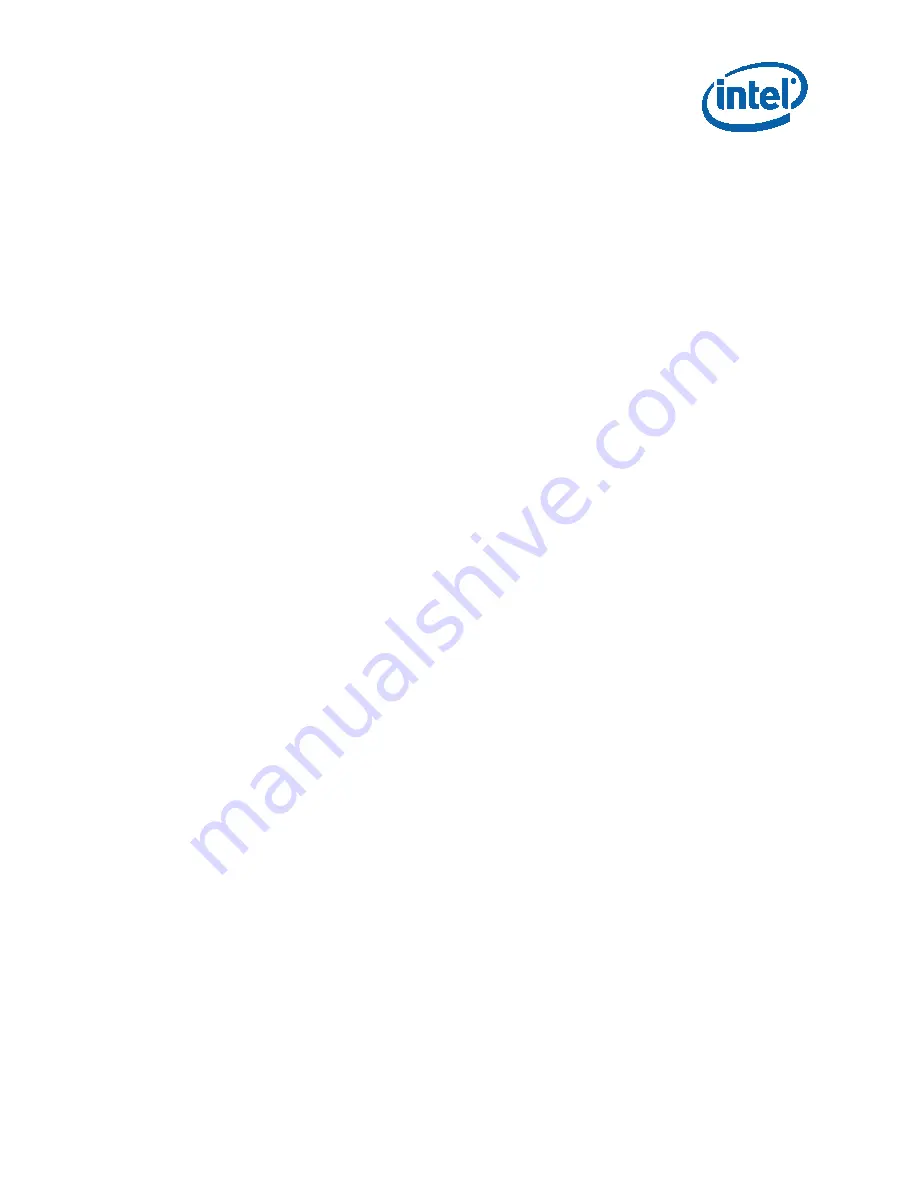
Balanced Technology Extended (BTX) Thermal/Mechanical Design Information
Thermal and Mechanical Design Guidelines
41
5.1.3
Effective Fan Curve
The TMA must fulfill the processor cooling requirements shown in Table 5–1 when it is
installed in a functional BTX system. When installed in a system, the TMA must
operate against the backpressure created by the chassis impedance (due to vents,
bezel, peripherals, and so forth) and will operate at lower net airflow than if it were
tested outside of the system on a bench top or open air environment. Therefore, an
allowance must be made to accommodate or predict the reduction in Thermal Module
performance due to the reduction in heatsink airflow from chassis impedance. For this
reason, it is required that the Thermal Module satisfy the prescribed
Ψ
CA
requirements
when operating against an impedance that is characteristic for BTX platforms.
Because of the coupling between TMA thermal performance and system impedance,
the designer should understand the TMA effective fan curve. This effective fan curve
represents the performance of the fan component AND the impedance of the stator,
heatsink, duct, and flow partitioning devices. The BTX system integrator can evaluate
a TMA based on the effective fan curve of the assembly and the airflow impedance of
their target system.
Note:
It is likely that at some operating points the fans speed will be driven by the system
airflow requirements and not the processor thermal limits.
Figure 5-1 shows the effective fan curve for the reference design TMA. These curves
are based on analysis. The boundary conditions used are the S2 6.9L reference
chassis, the reference TMA with the flow partitioning device, extrusion and an AVC
Type II fan geometry.
When selecting a fan for use in the TMA care should be taken that similar effective fan
curves can be achieved. Final verification requires the overlay of the Type II MASI
curve to ensure thermal compliance.
Summary of Contents for CELERON PROCESSOR E3000 - THERMAL AND MECHANICAL DESIGN
Page 24: ...Processor Thermal Mechanical Information 24 Thermal and Mechanical Design Guidelines ...
Page 80: ...Heatsink Clip Load Metrology 80 Thermal and Mechanical Design Guidelines ...
Page 82: ...Thermal Interface Management 82 Thermal and Mechanical Design Guidelines ...
Page 108: ...Fan Performance for Reference Design 108 Thermal and Mechanical Design Guidelines ...