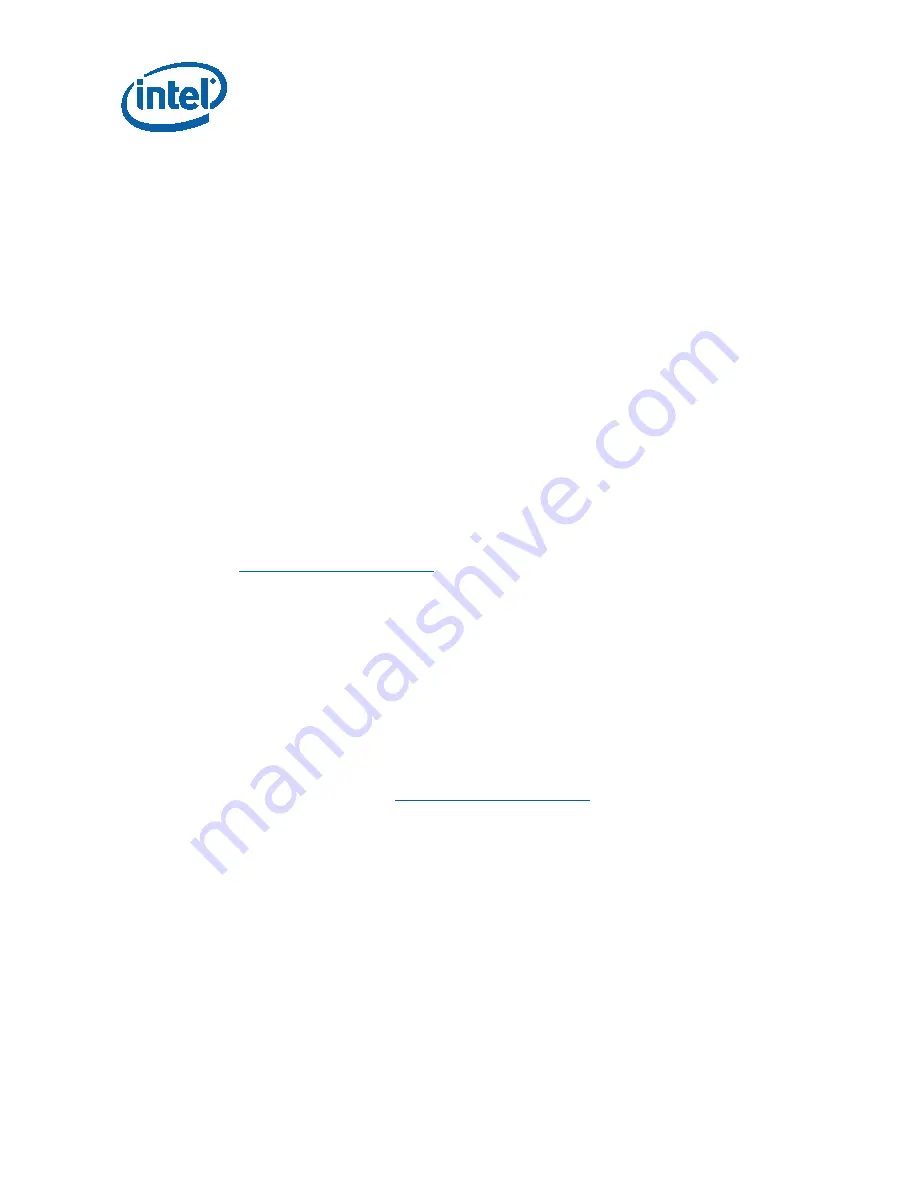
Processor Thermal/Mechanical Information
20
Thermal and Mechanical Design Guidelines
required to meet a required performance. As the heatsink fin density (the number of
fins in a given cross-section) increases, the resistance to the airflow increases: it is
more likely that the air travels around the heatsink instead of through it, unless air
bypass is carefully managed. Using air-ducting techniques to manage bypass area can
be an effective method for controlling airflow through the heatsink.
2.3.1
Heatsink Size
The size of the heatsink is dictated by height restrictions for installation in a system
and by the real estate available on the motherboard and other considerations for
component height and placement in the area potentially impacted by the processor
heatsink. The height of the heatsink must comply with the requirements and
recommendations published for the motherboard form factor of interest. Designing a
heatsink to the recommendations may preclude using it in system adhering strictly to
the form factor requirements, while still in compliance with the form factor
documentation.
For the ATX/microATX form factor, it is recommended to use:
•
The ATX motherboard keep-out footprint definition and height restrictions for
enabling components, defined for the platforms designed with the LGA775 socket
in Appendix G of this design guide.
•
The motherboard primary side height constraints defined in the ATX Specification
V2.1 and the microATX Motherboard Interface Specification V1.1 found at
The resulting space available above the motherboard is generally not entirely available
for the heatsink. The target height of the heatsink must take into account airflow
considerations (for fan performance for example) as well as other design
considerations (air duct, and so forth).
For BTX form factor, it is recommended to use:
•
The BTX motherboard keep-out footprint definitions and height restrictions for
enabling components for platforms designed with the LGA77 socket in Appendix G
of this design guide.
•
An overview of other BTX system considerations for thermal solutions can be
obtained in the latest version of the Balanced Technology Extended (BTX) System
Design Guide found at2.3.2
Heatsink Mass
With the need to push air cooling to better performance, heatsink solutions tend to
grow larger (increase in fin surface) resulting in increased mass. The insertion of
highly thermally conductive materials like copper to increase heatsink thermal
conduction performance results in even heavier solutions. As mentioned in
Section 2.1, the heatsink mass must take into consideration the package and socket
load limits, the heatsink attach mechanical capabilities, and the mechanical shock and
vibration profile targets. Beyond a certain heatsink mass, the cost of developing and
implementing a heatsink attach mechanism that can ensure the system integrity
under the mechanical shock and vibration profile targets may become prohibitive.
Summary of Contents for AT80569PJ080N - Core 2 Quad 3 GHz Processor
Page 24: ...Processor Thermal Mechanical Information 24 Thermal and Mechanical Design Guidelines...
Page 80: ...Heatsink Clip Load Metrology 80 Thermal and Mechanical Design Guidelines...
Page 82: ...Thermal Interface Management 82 Thermal and Mechanical Design Guidelines...
Page 108: ...Fan Performance for Reference Design 108 Thermal and Mechanical Design Guidelines...