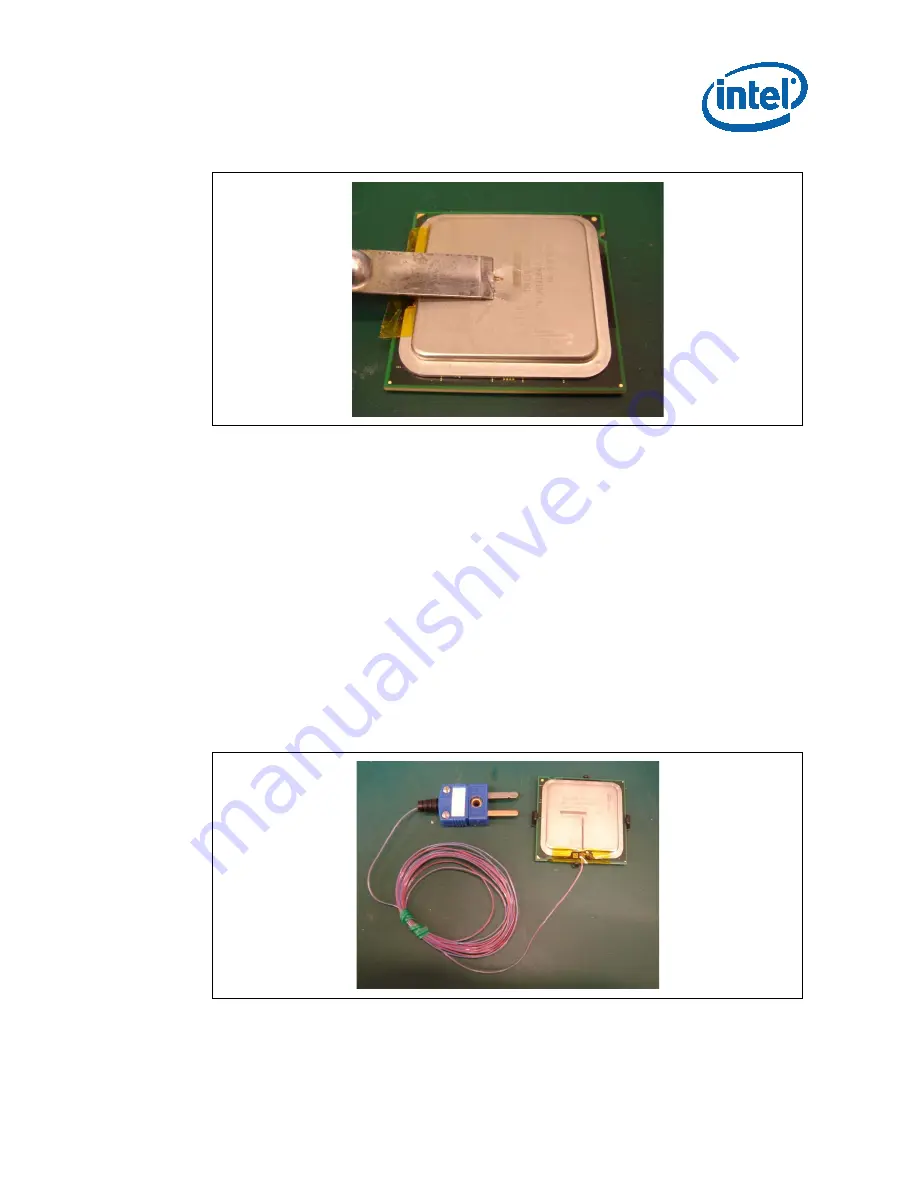
Case Temperature Reference Metrology
Thermal and Mechanical Design Guidelines
101
Figure 7-35. Removing Excess Adhesive from IHS
33.
Using a blade, carefully shave any adhesive that is above the IHS surface
(Figure 7-35). The preferred method is to shave from the edge to the center of
the IHS.
Note:
The adhesive shaving step should be performed while the adhesive is partially cured,
but still soft. This will help to keep the adhesive surface flat and smooth with no pits
or voids. If there are voids in the adhesive, refill the voids with adhesive and shave a
second time.
34.
Clean IHS surface with IPA and a wipe.
35.
Clean the LGA pads with IPA and a wipe.
36.
Replace the land side cover on the device.
37.
Perform a final continuity test.
38.
Wind the thermocouple wire into loops and secure or if provided by the vendor
back onto the plastic roll. (Figure 7-36).
Figure 7-36. Finished Thermocouple Installation
39.
Place the device in a tray or bag until it’s ready to be used for thermal testing use.
Summary of Contents for AT80569PJ080N - Core 2 Quad 3 GHz Processor
Page 24: ...Processor Thermal Mechanical Information 24 Thermal and Mechanical Design Guidelines...
Page 80: ...Heatsink Clip Load Metrology 80 Thermal and Mechanical Design Guidelines...
Page 82: ...Thermal Interface Management 82 Thermal and Mechanical Design Guidelines...
Page 108: ...Fan Performance for Reference Design 108 Thermal and Mechanical Design Guidelines...