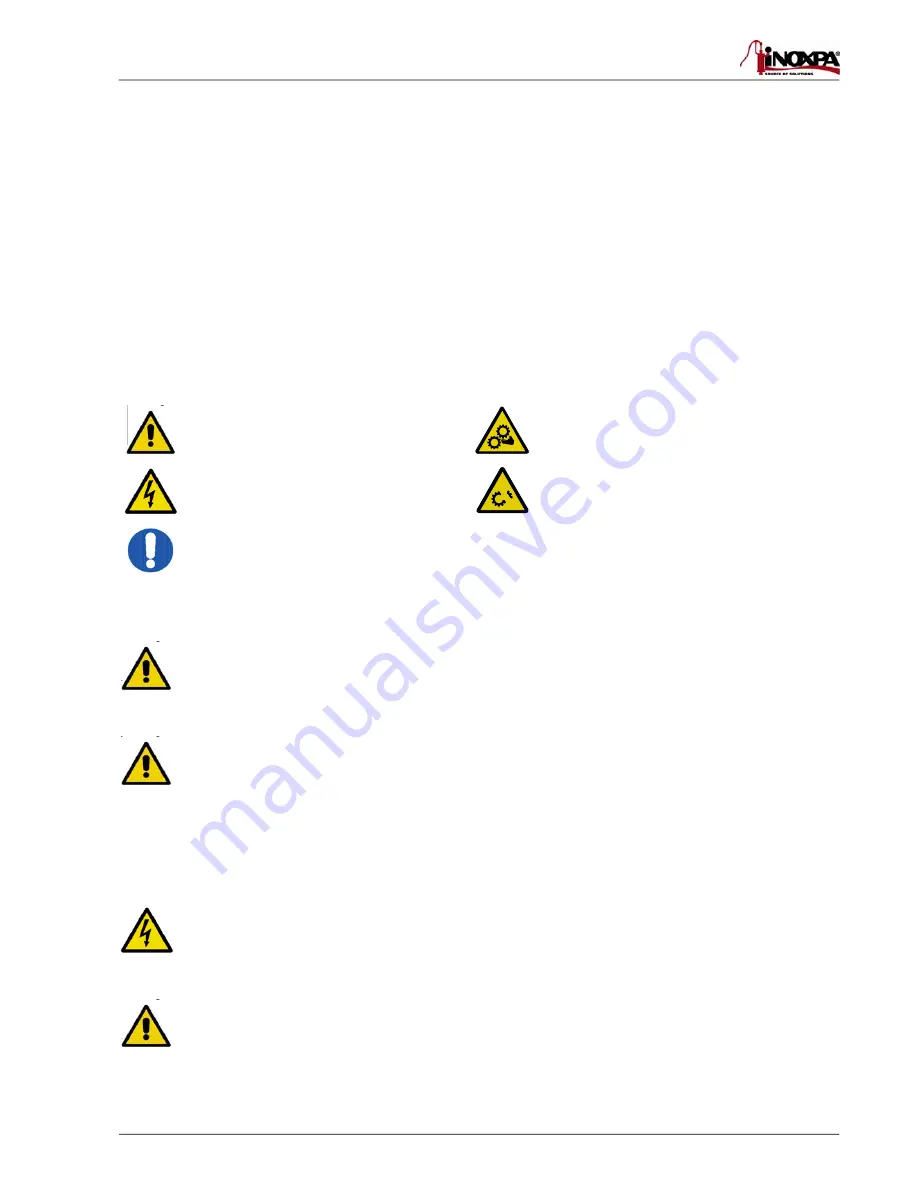
ED. 2010/11
1.Safety
3
1.
Safety
1.1.
INSTRUCTION MANUAL
This instruction manual contains the basic instructions that must be followed during installation, commissioning and
maintenance work.
The information given herein is based on the most up-to-date data available.
INOXPA reserves the right to modify this instructions manual without having to give prior notice.
1.2.
COMISSIONING INSTRUCTIONS
This instruction manual contains both essential and useful information in order that your valve be properly handled and
maintained.
Not only should the safety instructions set forth in this chapter be obeyed, but all those special measures and recommendations
that have been added to other chapters herein must also be observed. It is extremely important that these instructions be kept
in a set place near the installation.
1.3.
SAFETY
1.3.1.
Warning signs
Danger for people in general
Danger of injury caused by rotating parts
of the equipment.
Danger! Electricity
Danger to the proper operating of the
machine.
Obligation to ensure safety at work.
1.4.
GENERAL SAFETY INSTRUCTIONS
Please read the instruction manual carefully before installing and commissioning the control head.
Should you have any doubts or queries, contact INOXPA.
1.4.1.
During the installation procedure
Your must always bear in mind the
Technical Specifications
set forth in Chapter 8.
The installation and use of the C-TOP control head must always be carried out in accordance with
health and safety rules that are to be applied.
Before putting the valve / actuator into operation, check to make sure that it has been correctly
assembled and that the shaft has been perfectly aligned. Incorrect alignment and/or excessive force
applied during the securing of the control head may give rise to serious mechanical problems in the
same.
During the installation procedure, all the electrical work must be carried out by duly authorised
personnel.
1.4.2.
During operation
You must always bear in mind the
Technical Specifications
set forth in Chapter 8. The limit values that
have been set must NEVER be exceeded.
NEVER touch the valve and/or pipes that come into contact with the liquid whenever the valve is in
service. If it works with hot products, there is a risk of getting burned.