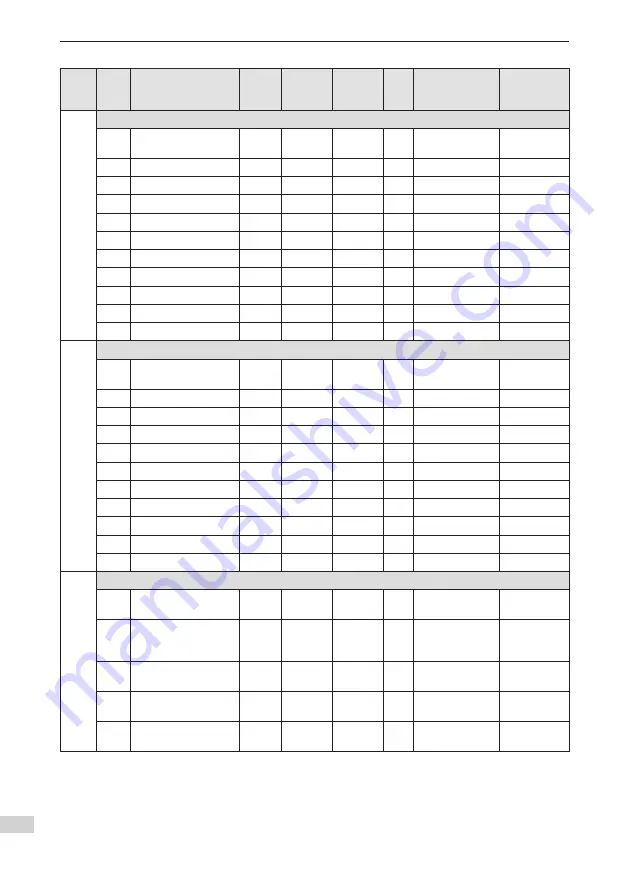
- 172 -
List of Object Groups
Index
(hex)
Sub-
index
(hex)
Name
Access
PDO
Mapping
Data
Type
Unit
Data Range
Default
1A20
TPDO21 Mapping Object
00
Number of mapped
objects in TPDO21
RW
NO
UINT8
-
0–0x0A
0x0A
01
1st mapping object
RW
NO
UINT32
-
0–0xFFFFFFFF
0x703F0010
02
2nd mapping object
RW
NO
UINT32
-
0–0xFFFFFFFF
0x70410010
03
3rd mapping object
RW
NO
UINT32
-
0–0xFFFFFFFF
0x70610008
04
4th mapping object
RW
NO
UINT32
-
0–0xFFFFFFFF
0x70640020
05
5th mapping object
RW
NO
UINT32
-
0–0xFFFFFFFF
0x706C0020
06
6th mapping object
RW
NO
UINT32
-
0–0xFFFFFFFF
0x70B90010
07
7th mapping object
RW
NO
UINT32
-
0–0xFFFFFFFF
0x70BA0020
08
8th mapping object
RW
NO
UINT32
-
0–0xFFFFFFFF
0x70BC0020
09
9th mapping object
RW
NO
UINT32
-
0–0xFFFFFFFF
0x70F40020
0A
10th mapping object
RW
NO
UINT32
-
0–0xFFFFFFFF
0x70FD0020
1A30
TPDO31 Mapping Object
00
Number of mapped
objects in TPDO31
RW
NO
UINT8
-
0–0x0A
0x0A
01
1st mapping object
RW
NO
UINT32
-
0–0xFFFFFFFF
0x783F0010
02
2nd mapping object
RW
NO
UINT32
-
0–0xFFFFFFFF
0x78410010
03
3rd mapping object
RW
NO
UINT32
-
0–0xFFFFFFFF
0x78610008
04
4th mapping object
RW
NO
UINT32
-
0–0xFFFFFFFF
0x78640020
05
5th mapping object
RW
NO
UINT32
-
0–0xFFFFFFFF
0x786C0020
06
6th mapping object
RW
NO
UINT32
-
0–0xFFFFFFFF
0x78B90010
07
7th mapping object
RW
NO
UINT32
-
0–0xFFFFFFFF
0x78BA0020
08
8th mapping object
RW
NO
UINT32
-
0–0xFFFFFFFF
0x78BC0020
09
9th mapping object
RW
NO
UINT32
-
0–0xFFFFFFFF
0x78F40020
0A
10th mapping object
RW
NO
UINT32
-
0–0xFFFFFFFF
0x78FD0020
1C12
Sync Manager 2_Assigned RPDO
00
Number of assigned
RPDOs
RW
NO
UINT8
-
0–0x04
0x04
01
1st PDO mapping
object index of
assigned RPDO
RW
YES
UINT16
-
0–0xFFFF
0x1600
02
Index for Object 2 of
assigned RPDO
RW
YES
UINT16
-
0–0xFFFF
0x1610
03
Index for Object 3 of
assigned RPDO
RW
YES
UINT16
-
0–65535
0x1620
04
Index for Object 4 of
assigned RPDO
RW
YES
UINT16
-
0–65535
0x1630
Summary of Contents for SV820N Series
Page 128: ...127 6 Trial Running 6 2 The definition part of FB 3 Five function blocks in FB...
Page 143: ...142 6 Trial Running 6 3 Open Visual studio and create a New Twincat3 Project...
Page 146: ...145 6 Trial Running 6 Click OK Click OK...
Page 147: ...146 6 Trial Running 6 Click Yes Click OK...
Page 149: ...148 6 Trial Running 6 C The default RPDO list is as follows...
Page 150: ...149 6 Trial Running 6...
Page 152: ...151 6 Trial Running 6 7 Activate the configuration and switch over to the running mode Click...
Page 158: ...157 6 Trial Running 6 Create a new POU...
Page 159: ...158 6 Trial Running 6 Create a new FB add MC_power MC_jog MC_home MC_absolute MC_reset to FB...
Page 160: ...159 6 Trial Running 6 Call axis_motion in main Call the program in PLCTASK...
Page 181: ...Revision History Date Revised Version Revised Details May 2017 A00 First release...