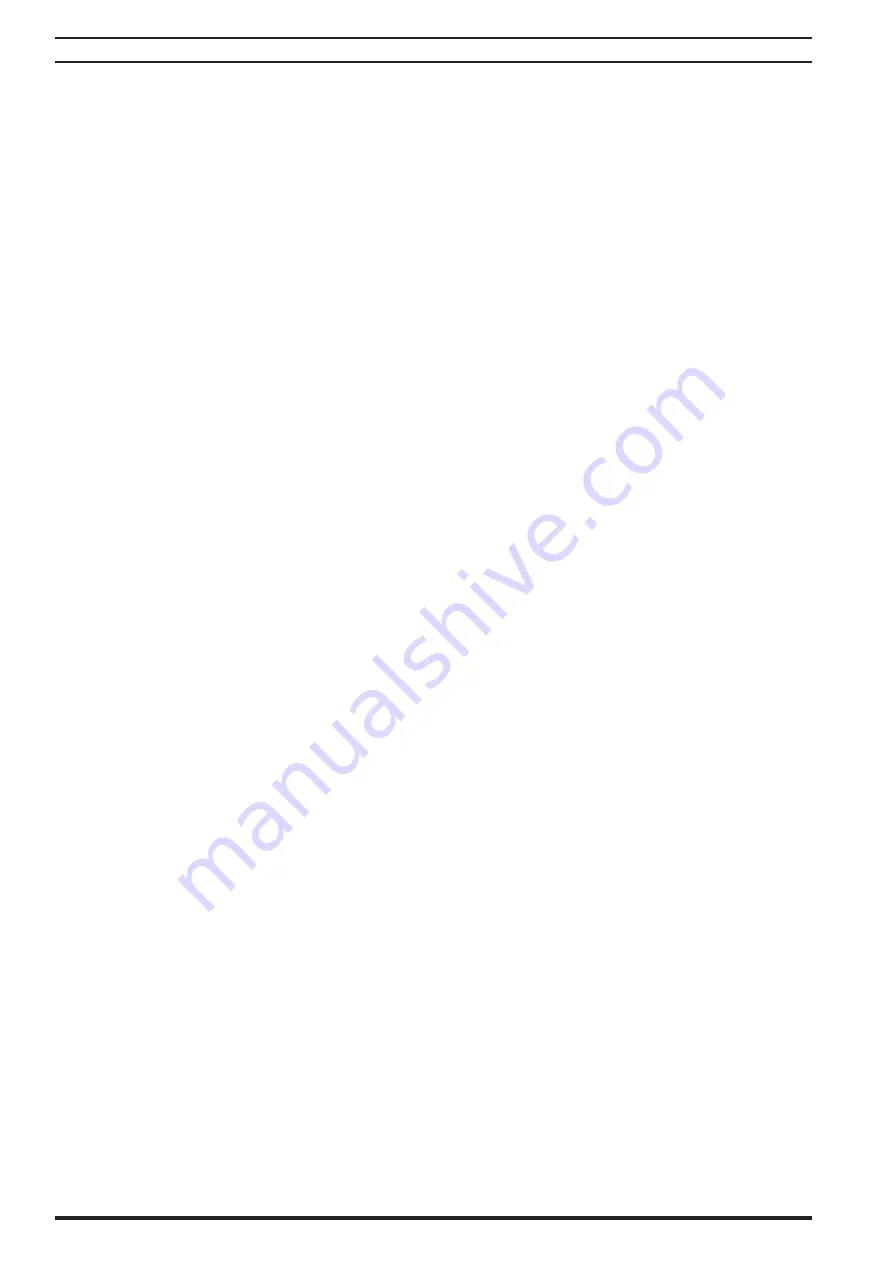
Page 42 of 44
EP20-XXXXX-XXX-XXX (en)
16. WARRANTY DECLARATION
Ingersoll-Rand / ARO, through its Reseller, warranty the products to be free of defects in material and workmanship, as deter-
mined by ARO inspection, within (24) TWENTY FOUR MONTHS from the date of placing the product in operation with the ini-
tial end customer or (26) TWENTY SIX MONTHS from the date of shipment, whichever occurs first.
Accordingly, the Warranty
is not available for products purchased from unauthorized sellers, because IR cannot oversee or take action to correct
product quality issues caused by unauthorized sellers.
This exclusion includes all products that are purchased from unau-
thorized sellers, including unauthorized Internet sites and unauthorized storefronts on online marketplaces.
Ingersoll-Rand / ARO will provide a new part or repaired part, at its election, in place of any part which is found upon its inspec-
tion to be defective in material and workmanship during the period described above. Such part will be repaired or replaced
without charge to the initial end customer during normal working hours at the place of business of a Reseller authorized to
sell the type of Product involved or other establishment authorized by Company. Initial end customer must present proof of
purchase (and purchase date) at the time of exercising this warranty and ship the product pre-paid authorized repair facility.
This warranty does not apply to failures occurring as a result of abuse, misuse, negligent repairs, corrosion, substitution of
non-Ingersoll Rand / ARO parts, erosion and normal wear and tear, alterations or modifications made to the Products without
express written consent of Ingersoll-Rand / ARO, or failure to follow the recommended operating practices and maintenance
procedures as provided in the product's operating and maintenance publications.
THIS WARRANTY IS IN LIEU OF ALL OTHER WARRANTIES (EXCEPT OF TITLE), EXPRESSED OR IMPLIED, AND THERE ARE
NO WARRANTIES OF MERCHANTABILITY OR OF FITNESS FOR A PARTICULAR PURPOSE.
The remedies of the initial end customer set forth under the provisions of warranty outlined above are exclusive. The total lia-
bility of Ingersoll-Rand / ARO, or its Reseller, with respect to this sale or the Products and services furnished under this sale, in
connection with the performance or breach of this warranty, or from the sale, delivery, installation, repair or technical direction
covered by or furnished under this sale, whether based on contract, warranty, negligence, indemnity, strict liability or other-
wise shall not exceed the purchase price of the unit or Products upon which such liability is based.
INGERSOLL RAND / ARO AND ITS RESELLER SHALL IN NO EVENT BE LIABLE TO THE INITIAL END CUSTOMER, ANY SUC-
CESSORS IN INTEREST OR ANY BENEFICIARY OR ASSIGNEE RELATING TO THIS SALE FOR ANY CONSEQUENTIAL, INCI-
DENTAL, INDIRECT, SPECIAL OR PUNITIVE DAMAGES ARISING OUT OF THIS SALE OR ANY BREACH THEREOF, OR ANY
DEFECTS IN, OR FAILURE OF, OR MALFUNCTION OF THE PRODUCTS UNDER THIS SALE WHETHER BASED UPON LOSS
OF USE, LOST PROFITS OR REVENUE, INTEREST, LOST GOODWILL, WORK STOPPAGE, IMPAIRMENT OF OTHER GOODS,
LOSS BY REASON OF SHUTDOWN OR NON-OPERATION, INCREASED EXPENSES OF OPERATION, COST OF PURCHASE
OF REPLACEMENT POWER OR CLAIMS OF USER OR CUSTOMERS OF THE USER FOR SERVICE INTERRUPTION WHETHER
OR NOT SUCH LOSS OR DAMAGE IS BASED ON CONTRACT, WARRANTY, NEGLIGENCE, INDEMNITY, STRICT LIABILITY OR
OTHERWISE.