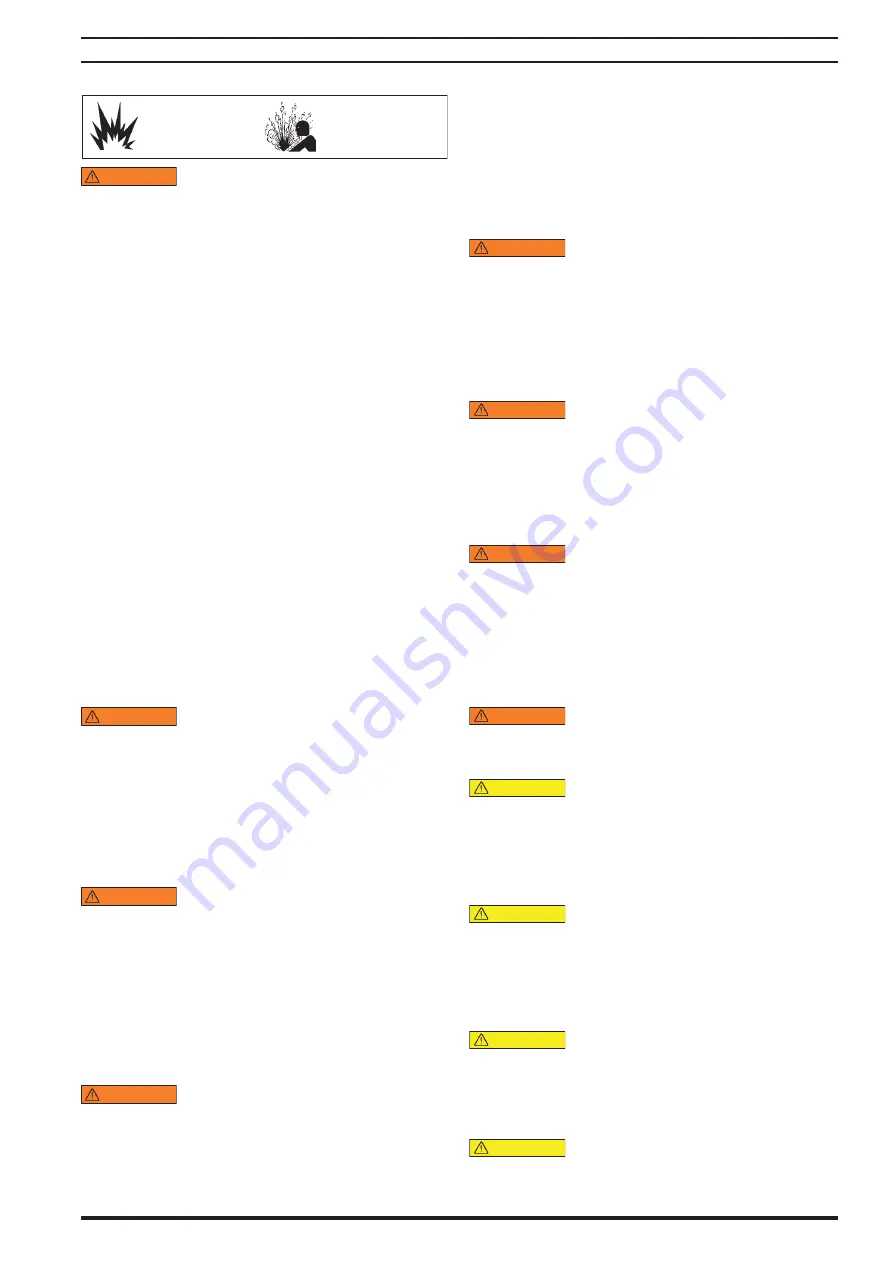
EP20-XXXXX-XXX-XXX (en)
Page 7 of 44
3. OPERATING AND SAFETY PRECAUTIONS
READ, UNDERSTAND, AND FOLLOW THIS INFORMATION TO AVOID INJURY AND PROPERTY DAMAGE.
EXCESSIVE FLUID PRESSURE
STATIC SPARK
HAZARDOUS MATERIALS
HAZARDOUS PRESSURE
WARNING
STATIC SPARK. Can cause explosion re-
sulting in severe injury or death. Ground pump and
pumping system.
Sparks can ignite flammable material and vapors.
The pumping system and object being sprayed must
be grounded when it is pumping, flushing, recirculat-
ing or spraying flammable materials such as paints,
solvents, lacquers, etc. or used in a location where
surrounding atmosphere is conducive to spontaneous
combustion. Ground the dispensing valve or device,
containers, hoses and any object to which material is
being pumped.
Secure pump, connections and all contact points to
avoid vibration and generation of contact or static
spark.
Consult local building codes and electrical codes for
specific grounding requirements.
After grounding, periodically verify continuity of
electrical path to ground. Test with an ohmmeter from
each component (e.g., hoses, pump, clamps, contain-
er, spray gun, etc.) to ground to ensure continuity.
Ohmmeter should show 0.1 ohms or less.
Submerse the outlet hose end, dispensing valve or de-
vice in the material being dispensed if possible. (Avoid
free streaming of material being dispensed.)
Use hoses incorporating a static wire.
Use proper ventilation.
Keep inflammables away from heat, open flames and
sparks.
Keep containers closed when not in use.
WARNING
Excessive fluid pressure developed by
pump can cause personal injury, pump damage or
property damage.
Fluid pressure developed by the pump do not exceed
the maximum as stated on the pump model plate.
Be sure material hoses and other components are
able to withstand fluid pressures developed by this
pump. Check all hoses for damage or wear. Be certain
dispensing device is clean and in proper working con-
dition.
WARNING
INSTALLATION OF ELECTRICAL COMPO-
NENTS FOR HAZARDOUS DUTY APPLICATIONS.
Pumps that will operate in environments defined as
“hazardous locations” must only be installed, con-
nected and set-up by qualified personnel with knowl-
edge and understanding of protection classes, regula-
tions and provisions for apparatus in hazardous areas,
for the region where the pump will operate, because
these regulations and provisions, along with the defi-
nition of what constitutes hazardous areas vary by
location.
WARNING
ELECTRIC SHOCK HAZARD. This equip-
ment must be grounded. Improper grounding, setup,
or usage of the system can cause electric shock.
Turn off and remove power before disconnecting any
cables and before servicing or installing equipment.
Connect only to grounded power source.
All electrical wiring must be done by a qualified elec-
trician and comply with all local codes and regula-
tions. For North America hazardous locations (NEC/
CEC), ensure wiring is done by a qualified and certified
electrician according to NFPA 70 and CSA C22.1. Refer
to IEC 60079-14 for ATEX/IECEx wiring requirements.
Refer to VFD label and manual for minimum capacitor
discharge time prior to any service.
WARNING
HAZARDOUS PRESSURE. Can result in
serious injury or property damage. Do not service or
clean pump, hoses or dispensing valve while the sys-
tem is pressurized.
Disconnect and lockout / tagout power supply to elec-
tric motor and VFD. Relieve pressure from the system
by opening dispensing valve or device and / or care-
fully and slowly loosening and removing outlet hose
or piping from pump.
WARNING
HAZARDOUS MATERIALS. Can cause se-
rious injury or property damage. Do not attempt to
return a pump to the factory or service center that
contains hazardous material. Safe handling practices
must comply with local and national laws and safety
code requirements.
Obtain Material Safety Data Sheets on all materials
from the supplier for proper handling instructions.
WARNING
EXPLOSION HAZARD. Models containing
aluminum wetted parts cannot be used with 1-1-1
-Trichloroethane,Methylene Chloride or other Halo-
genated Hydrocarbon solvents which may react and
explode.
Check pump crankcase section, PRV section, Oil mod-
ule section, fluid caps, manifolds and all wetted parts
to assure compatibility before using with solvents of
this type.
WARNING
MISAPPLICATION HAZARD. Do not use
models containing aluminum wetted parts with food
products for human consumption. Plated parts can
contain trace amounts of lead.
CAUTION
Verify the chemical compatibility of the
pump wetted parts and the substance being pumped,
flushed or recirculated. Chemical compatibility may
change with temperature and concentration of the
chemical(s) within the substances being pumped,
flushed or circulated. For specific fluid compatibility,
consult the chemical manufacturer.
CAUTION
HOT SURFACE. Metallic wetted sections
can reach up to the same temperature as the fluid
temperature (up to 100°C). Precautions should be
taken to restrict access to hot surfaces when needed.
Proper personal protective equipment (PPE) for hot
surfaces should be worn. Check to ensure parts have
cooled down sufficiently prior to any maintenance.
CAUTION
Maximum temperatures are based on
mechanical stress only. Certain chemicals will signifi-
cantly reduce maximum safe operating temperature.
Consult the chemical manufacturer for chemical com-
patibility and temperature limits. Refer to PUMP DATA
on page 3 of this manual.
CAUTION
Be certain all operators of this equipment
have been trained for safe working practices, under-
stand it’s limitations, and wear safety goggles / equip-
ment when required.