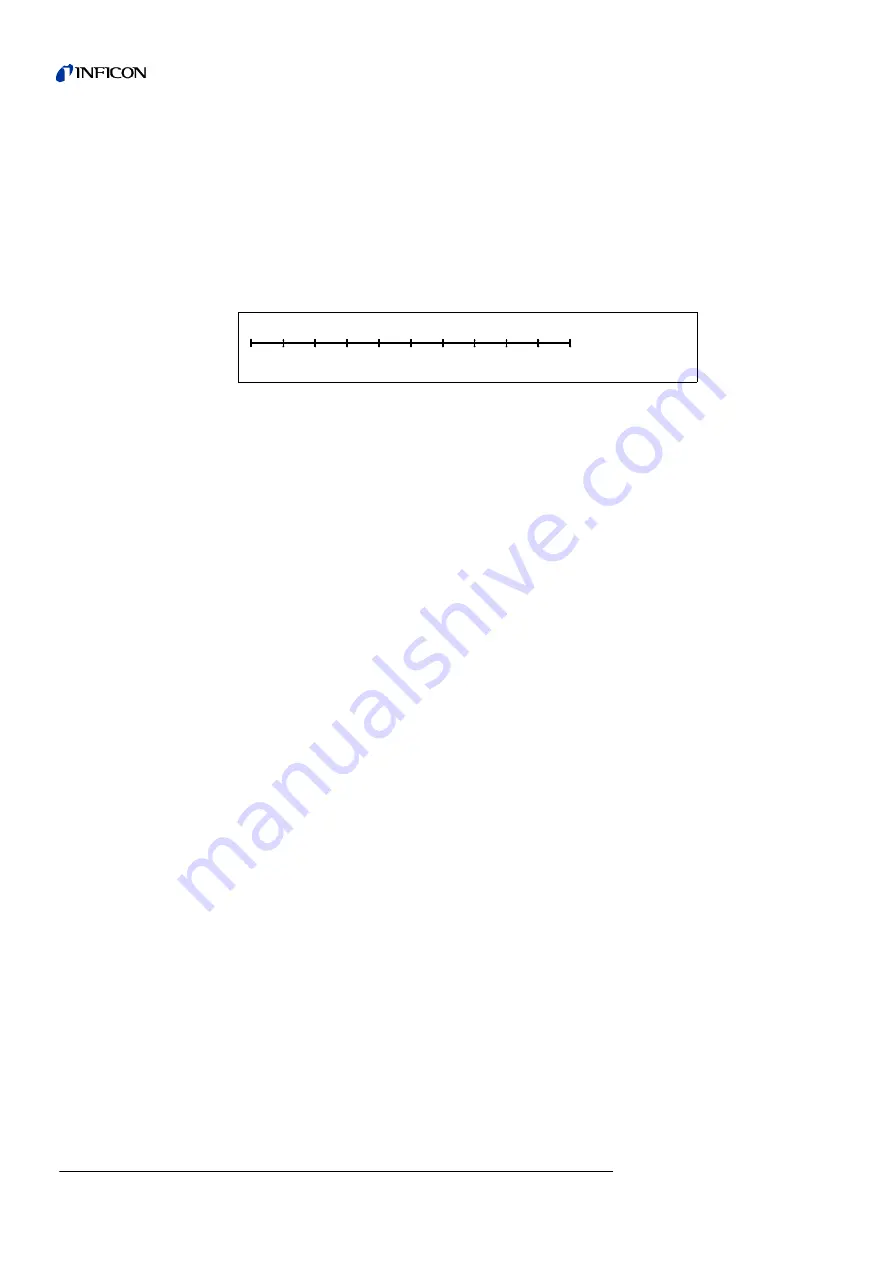
66
Description of the Menu
iina
74
e 0
6
.f
m
te
chn
ica
l ha
nd
boo
k
(1
40
8)
LR lin
The leak rate output voltage is scaled linear. The fundamental voltage is 0-10 V in
scalable steps from 0.5 to 10 volts per decade.
For information about scaling see chapter
LR log
The leakrate is recorded on a logarithmic scale. The voltage output ranges from
1 … 10 V with steps of 0.5 V per decade.
For adjusting of scaling see chapter
LR mantissa:
The leak rate mantissa is recorded linearly from 1 … 10 V.
LR exponent
The exponent is recorded. Step function: U = 1 … 10 V with steps of 0.5 V per
decade, starting with 1 V = 1×10
-12
.
6.6.4.3
RS232 Protocol
•
>
>
>
Fig. 6-11 Example of range of leak rate, log, 0.5 V/decade
0
1
2
3
4
5
6
7
8
9
10
V
-12
-10
-8
-6
10
10
10
10
LR in channel 1
-4
-2
0
+2
10
10
10
10
Softkey 3:
Diagnostics
Gives the chance to read parameters, e.g. during maintenance.
Softkey 4:
Printer Manual
Leak rates measured by this function can be sent to RS232 printers or PC. The
measured value can be displayed via hyperterminal programs. The baudrate of this
printer function is set to 9600, 8N1. Connected data loggers must be set to these
parameters.
Format of the leak rate output:
LR = 1.00E-10 09:Apr.07 08:25 MEAS
LR:
Leak rate
The measured value is equal to the number which then follows. In case
of overflow or underflow the symbol < (leak rate is less then the stated
value) or > (leak rate is greater than the stated value) is output accor-
dingly.
1.00E-10:
Output of the measured value in the unit set up, followed by date and
time.
MEAS:
The UL5000 is in the measure mode.
When pressing the START button once again in the measure mode or activation of
the START input at the DIGITAL IN port the leak rate will be send out.