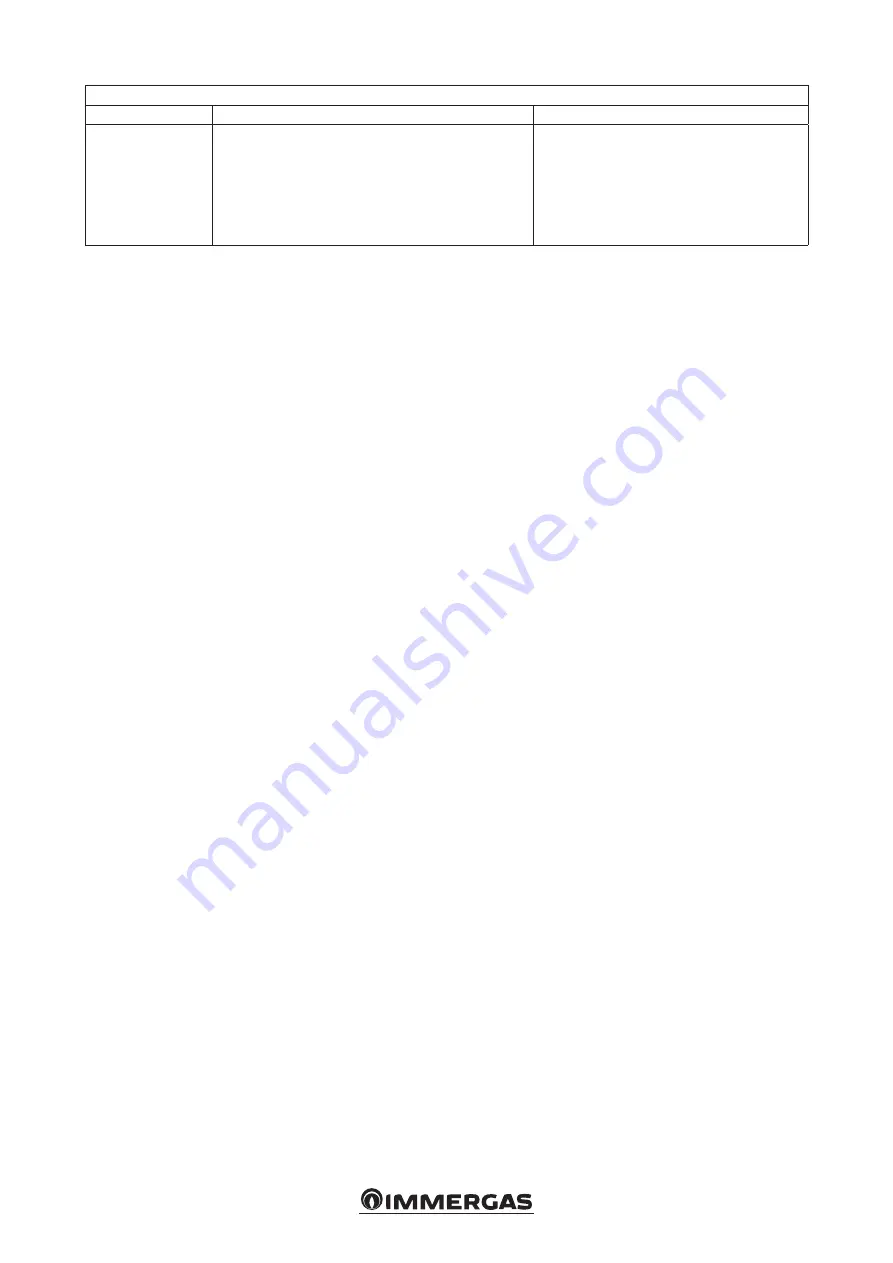
8
Menù Service ->Test switch Max pres
Menu item
Description
Range
Test Pressure switch
Test method for high pressure switch.
N.B. to run the test, set the value to 1 and wait for the test result
0 = Off
1 = Test required
N.B. the following states are managed by the machine DO NOT USE
2 = AP Test in progress
3 = AP Test performed correctly
4 = AP Test failed for maximum time reached
5 = AP Test failed for flow switch error
6 = AP Test failed for low water temperature
7 = AP Test failed for inverter error
N.B.: the Test mode has been implemented for
the execution of tests. When the Test mode
is active, the water temperature set point is
ignored by the control system.
When the Test mode is active, the pump
operation is forced.
Attention: if the test shows the need to replace
the pressure switch, you must recover the
coolant charge, this type of pressure switch is
not installed on automatic valves (Schrader
type).
Visually inspect the protection tools (valves,
pressure switches), at least once a year.
If the chiller works in a place where the
atmosphere is corrosive, the protective device
must be inspected more frequently.
Periodically search for leaks, immediately
eliminating all those eventually found.
Periodically ascertain that the vibration level is
contained within the standard limits, meaning
that it is close to that emitted at the time of first
chiller start-up.
Before opening a cooling circuit, make sure to
transfer the coolant in the cylinders specifically
designed for this purpose and consult the
pressure gauges.
Following the failure of equipment, replace the
coolant observing the procedure described in
NF E29-795 or have the coolant analysed by a
specialised laboratory.
If the cooling circuit remains open after
an intervention (i.e. the replacement of a
component, etc.):
•
seal the openings if duration is less than one
day;
•
if longer than 1 days, charge the circuit
with nitrogen without oxygen (principle of
inertia).
The purpose is to prevent the penetration of
atmospheric humidity and resulting corrosion.
1.2.4. Considerations about the safety of
repair interventions.
The maintenance of all installation components
must be performed by authorised personnel,
in order to prevent the risk of deterioration
and injuries. Promptly eliminate any defects
and leaks. The authorised technician is obliged
to promptly repair the fault detected. After
repairing the individual units, make sure that the
protection devices work properly and fill out a
verification report of the parameters.
Observe the rules and recommendations
prescribed for the unit, as well as the safety
standards of the HVAC systems, such as: EN
378, ISO 5149, etc.
If the power supply cable is damaged, it
must be replaced by the manufacturer, its
assistance service or personnel with similar
requirements, in order to avoid the arising of
a potentially dangerous situation.
RISK OF EXPLOSION.
When purging and pressurising the cooling
circuit required for leak detection, do not use
either air or gas containing oxygen. Mixtures
of pressurised air or gases containing oxygen
can cause explosions. The oxygen triggers a
violent reaction if it comes into contact with
oils and lubricants.
Therefore, for leak detection, it is essential to
use only nitrogen, possibly supplemented with
suitable gas tracer.
Failure to comply with these recommendations
could imply serious consequences, even fatal,
for people, as well as serious damage to the
system.
Never exceed the maximum operating
pressures specified. Check the minimum and
maximum test pressures allowed, comparing
them with that indicated on this manual and
with the pressures indicated on the unit plate.
Do not unsolder or cut with cutting torch
the coolant pipes or any cooling circuit
components before all the coolant (liquid
and vapour) and oil have been made to flow
through the heat pump. The steam traces must
be expelled from the circuit by blowing dry
nitrogen. If in contact with an open flame, the
coolant generates toxic gases.
For this reason it is necessary to have the
required protection means and have a flame
extinguishing system at hand which is suitable
to the appliance features and type of coolant
used in it.
The coolant must never be decanted for
siphoning.
Prevent the liquid coolant from coming into
contact with the skin or sprayed in the eyes.
Wear protective gloves and goggles. If the
coolant falls on the skin, was it off with
abundant water and soap. If the coolant is
sprayed in the eyes, immediately rinse them
with running water and then immediately
consult a doctor.
The accidental release of coolant, caused by
minor leaks or significant leaks following
the rupture of a pipe or sudden leak from
a discharge valve, can cause frostbite and
burns to exposed personnel. Do not ignore
such injuries. Installers, owners and skilled
technicians of the assistance service of these
units must:
•
Contact a doctor before treating these
injuries.
•
Have access to a first aid kit, especially to treat
eye injury.
We recommend observing the provisions of EN
378-3 Appendix 3 and ISO5149.
Never use open flames or live steam on the
cooling circuit. Otherwise, dangerous pressure
may develop inside them.
Summary of Contents for AUDAX TOP
Page 1: ...AUDAX TOP 18 21 ErP IE Instruction and recommendation booklet 1 040572ENG...
Page 2: ......
Page 70: ......
Page 71: ......