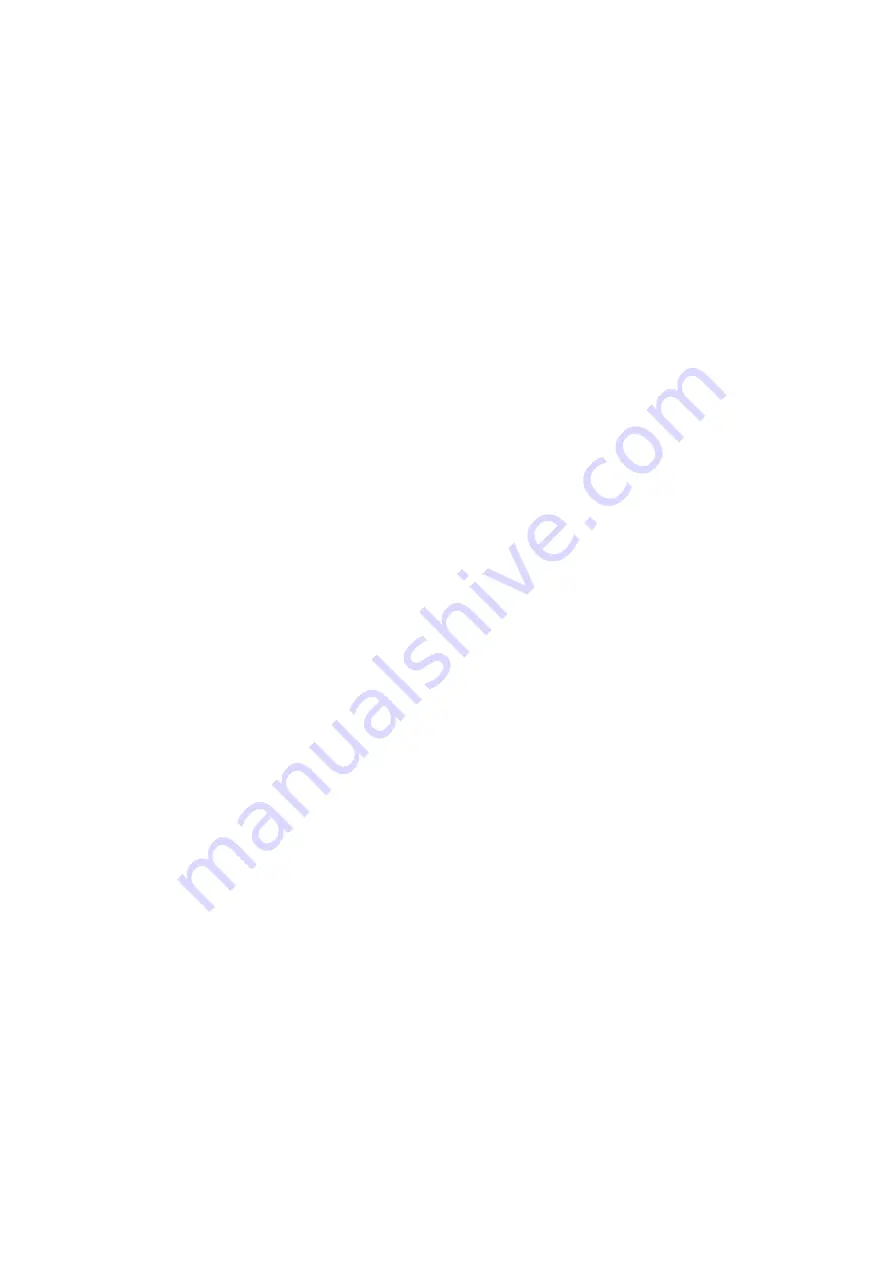
Immergas S.p.A. declines all liability due to printing or transcription errors, reserving the right to make any modifications to its technical and commercial
documents without prior notice.
Dear Customer,
Our compliments for having chosen a top-quality Immergas product, able to assure well-being and safety for a long period of time.
As an Immergas customer
you can also count on a qualified after-sales service, prepared and updated to guarantee constant efficiency of your boiler. Read the following pages carefully: you
will be able to draw useful suggestions regarding the correct use of the appliance, the respect of which, will confirm your satisfaction for the Immergas product.
For assistance and scheduled maintenance contact Authorised After-Sales centres: they have original spare parts and are specifically trained directly by the
manufacturer.
General recommendations
All Immergas products are protected with suitable transport packaging.
The material must be stored in dry environments protected against bad weather.
The instruction book is an integral and essential part of the product and must be consigned to the new user also in the case of transfer or succession of ownership.
It must be stored with care and consulted carefully, as all of the warnings provide important safety indications for installation, use and maintenance stages.
This instructions manual provides technical information for installing Immergas boilers. As for the other issues related to boiler installation (e.g. safety in the work
site, environment protection, injury prevention), it is necessary to comply with the provisions specified in the regulations in force and principles of good practice.
In compliance with legislation in force, the systems must be designed by qualified professionals, within the dimensional limits established by the Law. Installation
and maintenance must be performed in compliance with the regulations in force, according to the manufacturer's instructions and by an authorised company,
which has specific technical expertise in the system sector, as required by Law.
Improper installation or assembly of the Immergas appliance and/or components, accessories, kit and devices can cause unexpected problems to people, animals
and objects. Read the instructions provided with the product carefully to ensure a proper installation.
Maintenance must be carried out by an authorised company. The Authorised After-sales Service represents a guarantee of qualification and professionalism.
The appliance must only be destined for the use for which it has been expressly declared. Any other use will be considered improper and therefore potentially
dangerous.
If errors occur during installation, operation and maintenance, due to non compliance with technical laws in force, standards or instructions contained in this
book (or however supplied by the manufacturer), the manufacturer is excluded from any contractual and extra-contractual liability for any damages and the
appliance warranty is invalidated.
The company IMMERGAS S.p.A., with registered office in via Cisa Ligure 95 42041 Brescello (RE), declares that the design, manufacturing and after-sales
assistance processes comply with the requirements of standard UNI EN ISO 9001:2008.
For further details on the product CE marking, request a copy of the Declaration of Conformity from the manufacturer, specifying the appliance model
and the language of the country.
Summary of Contents for 3.025499
Page 1: ...MAGIS HERCULES ERP IE Instruction and recommendation booklet 1 038684ENG ...
Page 2: ......
Page 39: ...39 3 3 2 2 INSTALLER USER MAINTENANCE TECHNICIAN ...
Page 66: ...66 ...
Page 67: ...67 ...