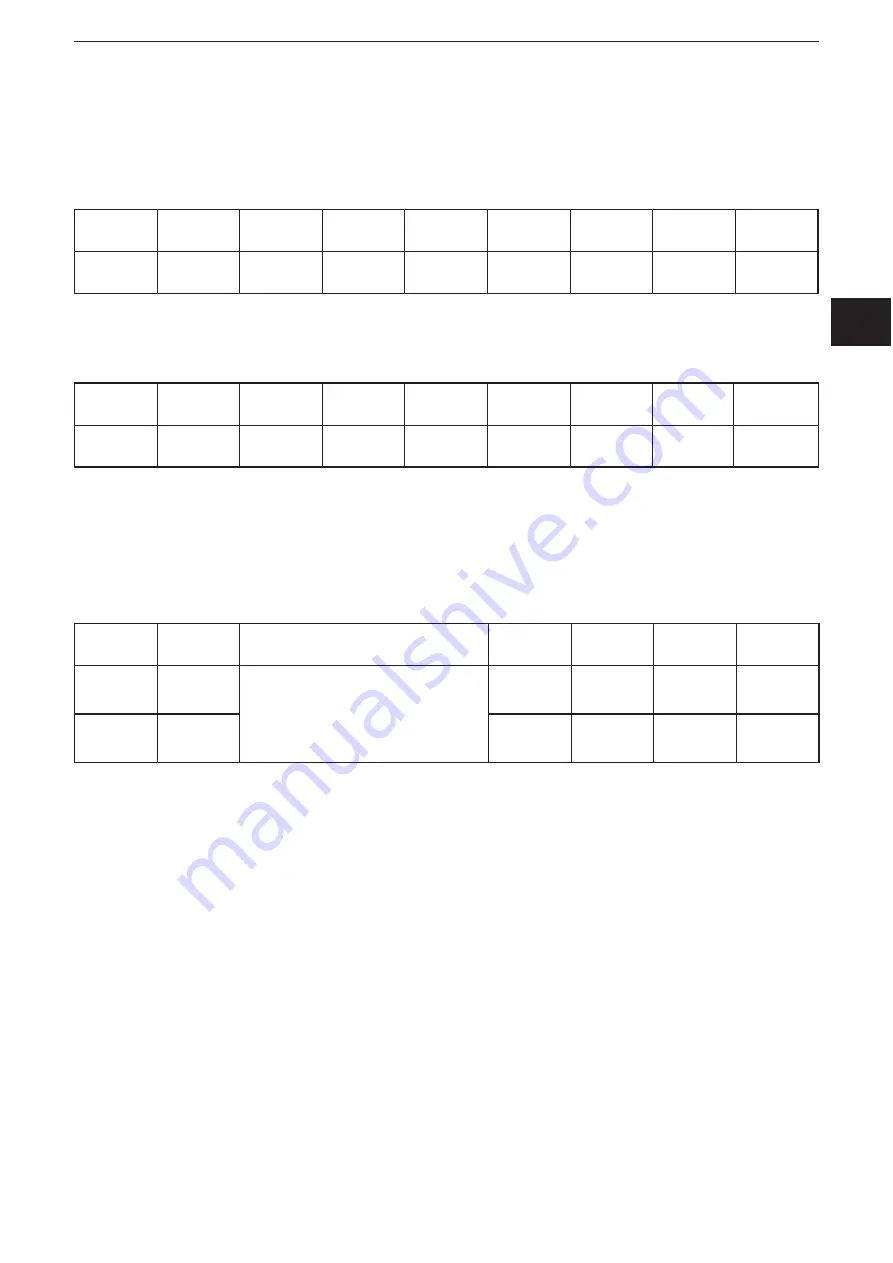
UK
Field modules DP
13
5 Data mapping of the modules
5.1 Data mapping: Stand-alone and extension modules
5.1.1 Digital input modules
Bit
7
6
5
4
3
2
1
0
M12
C3P2
C3P4
C2P2
C2P4
C1P2
C1P4
C0P2
C0P4
Input data in the process image (C = female connector, P = pin)
5.1.2 Digital output modules
Bit
7
6
5
4
3
2
1
0
M12
C3P2
C3P4
C2P2
C2P4
C1P2
C1P4
C0P2
C0P4
Output data in the process image (C = female connector, P = pin)
5.1.3 Digital combined modules
4 digital inputs and 4 digital outputs
4 bits input and 4 bits output are mapped:
Bit
7...4
3
2
1
0
Input
Byte 0
(M12)
Reserved
C1P2
C1P4
C0P2
C0P4
Output
Byte 0
(M12)
C3P2
C3P4
C2P2
C2P4
Data in the process image (C = female connector, P = pin)
Summary of Contents for Ecomot300 AC2630
Page 35: ...UK Field modules DP 35 ...