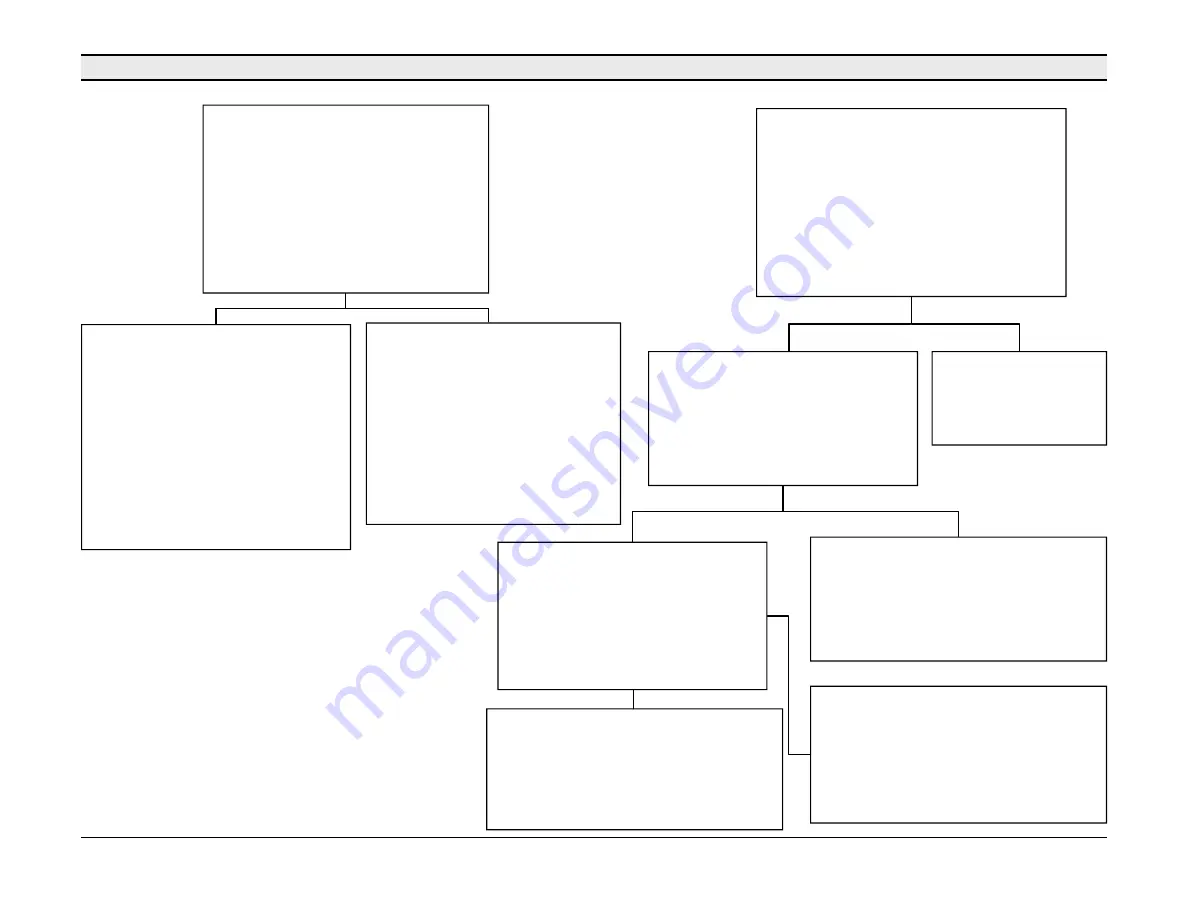
Section 8: TROUBLESHOOTING
Page 5
8
OM-ZR-May15
Clamp Will Not Close (Continued)
Clamp pressure cycles up & down
Turn clamp switch to OPEN for 2 seconds
Shut down engine
Disconnect clamp quick-disconnect
couplers
Restart engine
Turn clamp switch to CLOSE
Clamp pressure is constant
Turn clamp switch to OPEN for
2 seconds
Shut down engine
Replace clamp seals
Reconnect clamp quick-disconnect
couplers
After repairs, resume normal
operation
Clamp pressure cycles up & down
Turn clamp switch to OPEN for
2 seconds
Shut down diesel engine
Reconnect clamp quick-disconnect
couplers
Clean shuttle valve (SV1)
After repairs, resume normal operation
Clamp pressure is constant
Turn clamp switch to OPEN for 2 seconds
Shut down engine
Disconnect and reconnect clamp quick-
disconnect couplers
Restart engine
Turn clamp switch to CLOSE
Clamp does not close
Shut down engine
Disconnect close-clamp hose at clamp
Restart engine
Turn clamp switch to CLOSE
Clamp closes
Resume normal
operation
Point A
Clamp closes
Turn clamp switch to OPEN for 2 seconds
Shut down engine
Recheck clamp quick-disconnect couplers
If problem not solved, call ICE
Clamp does not close
Shut down engine
Clean, repair or replace clamp
holding valve (CV7)
Reconnect open-clamp hose at clamp
Resume operation
Flow from close-clamp hose
Shut down engine
Reconnect close-clamp hose at clamp
Disconnect open-clamp hose at clamp
Restart engine
Clamp switch to CLOSE
No flow from open-clamp hose
Turn clamp switch to OPEN for 2 seconds
Shut down engine
Recheck clamp quick-disconnect couplers
If problem not solved, call ICE