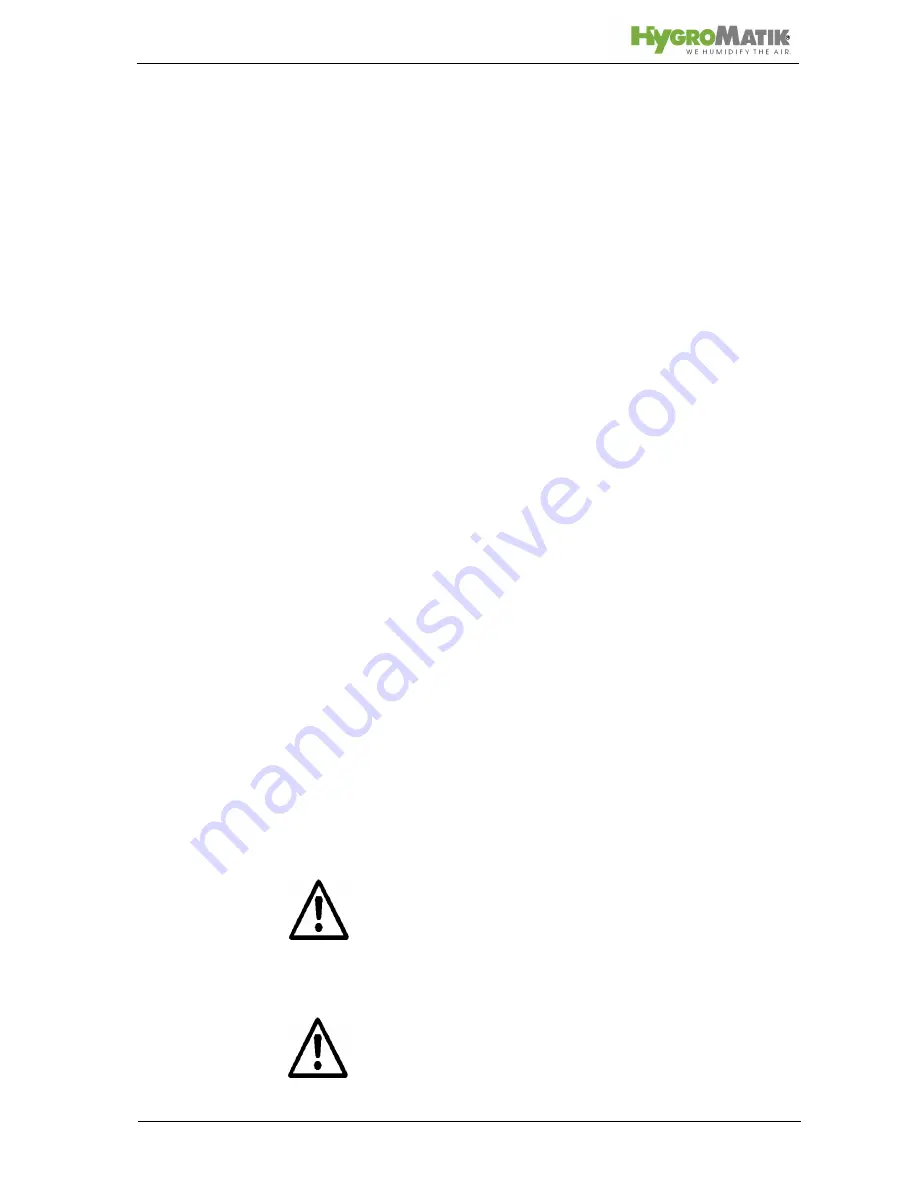
Page 54
9.7 Cleaning the Water Inlet Solenoid Valve
Removal
»
Shut off water supply and loosen water installation hose
connection.
»
Remove cylinder please also see chapter „Removing
and Cleaning Steam Cylinder“
»
Loosen connecting hose (21) from the base.
»
Detach e-cable from the solenoid valve.
»
Loosen solenoid valve mounting screws (28).
»
Remove solenoid valve from the borehole.
»
Remove fine mesh filter (29) from the solenoid valve,
clean and replace if needed.
Installation
»
Insert fine mesh filter (29).
»
Place solenoid valve with seal in the borehole of the
unit housing.
»
Attach solenoid valve tightly with screws (28).
»
Screw on water installation hose.
»
Connect e-cable to the solenoid valve.
»
Attach connecting hose (21) to the base.
» Install
cylinder.
»
Turn on the tap.
»
Switch on the unit and check for leaks during operation.
If leakage occurs, switch off power supply and follow safety
instructions for work on live components.
9.8 Checking Cable Connections and Electrode
Cables
»
Make sure that no cable and plug connections are
loose.
Warning:
Plugs must be pressed down onto electrodes as far as
they will go.
Loose cable connections cause excessive contact resistance
and overheating of contact surfaces.
»
Check electrode plug isolation, replace plugs as
needed.
Warning:
Replace electrode plugs after removing and reinstall-
ing them several times.