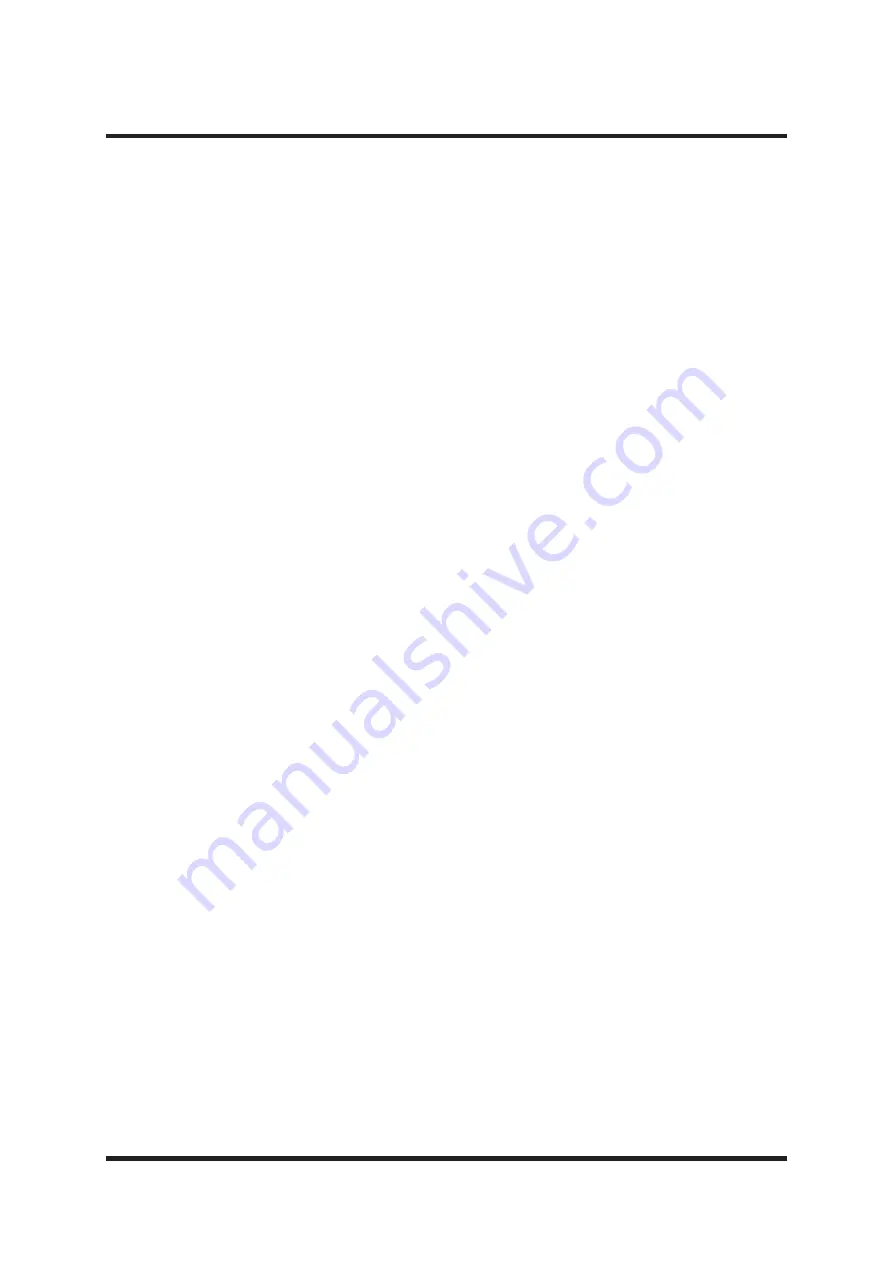
Container / Valve Assy leakage Test
A leakage test is required for all filled FM-200
®
valves
and container assemblies after being left to stand in a
bonded area for at least 24 hours�� Two test options are
available�� The test equipment used for both test options is
a leak detector and calibration gas��
Halotek Leak Detector Test
1�� After 24 hours standing, the valve pressure gauge
should be checked for pressure loss (refer to temperature
correction chart to adjust for temperature change)�� The
container and valve assembly should then be checked for
leakage using the Halotek leak detector unit��
2�� Testing should take place in an area free of FM-
200
®
contamination��
3�� Take the Halotek unit & calibration gas and within
the FM-200
®
free environment, calibrate the unit��
4�� Adjust the Halotek leak detector to gain a steady
audible pulse, in free air, of about 2 to 4 pulses per
second��
5�� Conduct a stability check by leaving the Halotek unit
for approximately 3 minutes in a clean air environment�� If
the pulse rate is observed to stay within the range of 2 to 4
pulses per second, proceed to the repeatability check��
If the stability check is inconclusive, repeat
stability check in an alternative clean environment�� If
stability problems persist, contact R&D department for
instruction��
6�� The leak standard of 0��13 oz/year should be condi-
tioned to a temperature of 20 °C +/-5 °C (68 °F ± 9 °F) for
at least 24 hours��
7�� Conduct a calibration repeatability test��
8�� Remove the cap from the leak standard, screw the
calibration nozzle into the outlet of the bottle and open the
hand valve fully��
9�� Place the Halotek probe into the calibration nozzle��
Within 5 seconds the pulse rate should start to increase
and be a continuous tone within 15 seconds��
10�� Remove the probe from the nozzle and position
the Halotek unit away from the gas source�� The pulse rate
should revert back to the original rate of 2 to 4 pulses per
second within 15 seconds��
11�� Repeat test a further two times�� If repeatability
test indicates that the unit is functioning within the set
parameters, proceed to the container leak test��
However, if the repeatability check is inconclusive,
repeat check in an alternative clean environment�� If
repeatability problems persist, contact R&D department
for instruction�� Close the hand valve of the leak standard
after use��
Helium Sniffer Test (Alternative Test)
Details of the procedure and equipment required are
available from the Original Equipment Manufacturer
(O��E��M) on request��
Container Leak Test
Carefully probe the container/valve assembly at all probes
and openings�� Ensure that the probe is not brought into
direct contact with any objects as this can lead to spurious
results and ensure that the dwell time of the probe is
sufficiently long (more than 5 seconds) to ensure any
leak is detected�� Any significant and repeatable increase
of the audible pulse rate should be taken as an indication
of a leak and the container and valve assembly should be
rejected��
Once the leakage source has been rectified, the
container and valve assembly should be subjected to a
further leak test using the Halotek unit��
© 2010 Macron Safety Systems (UK) Limited
SECTION 9 - RECHARGING PROCEDURE
EQUIPMENT:
FM-200® (UL/FM)
PUBLICATION:
14A-07H
ISSUE No.
02
DATE:
2010-03