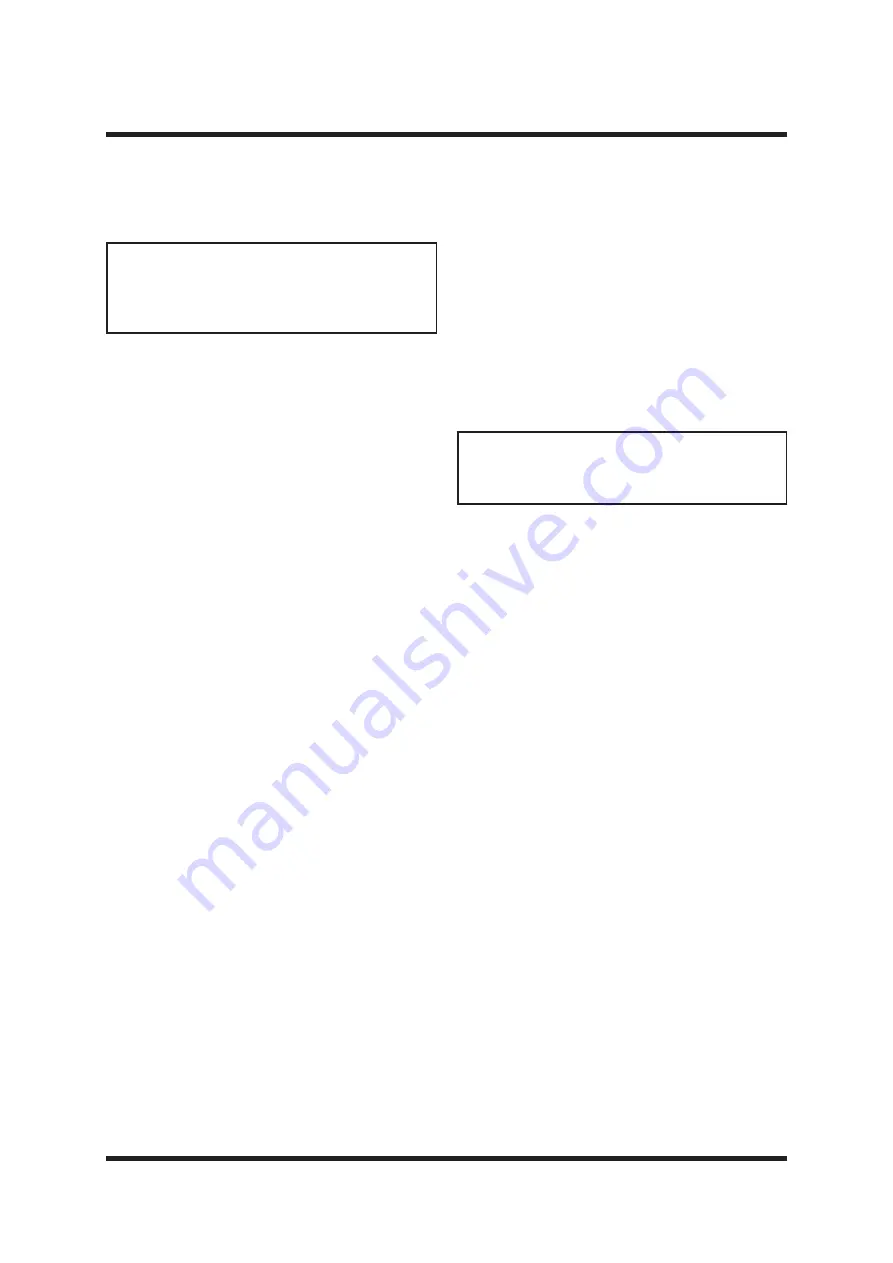
Field Installing Liquid Level Measuring
Device
Caution.
Container must be completely empty before
removing the liquid level device or the port plug��
Severe injury or damage could accur if container
contains pressure��
If desired, and the container is equipped with a port for
liquid level measuring device, it must be installed before
filling the container��
To install the liquid liquid level measuring device,
remove the plug the plug in the liquid level port on the
container��
Make certain the O-ring on the device, the thread on
the device and the container port, are clean�� Apply a small
amount of PTFE silicone grease to the O-ring and the
thread on the device��
Install the device into the port and tighten to a metal
to metal contact��
Filling
Filling can only be undertaken by trained and authorised
UL and FM fill stations��
1�� With the Container ready for filling a check is made
to the filling instruction sheet and the container fill weight,
time, date and fill details record��
2�� The container is placed on a scales and the
appropriate filling adapter attached to the container valve
discharge port��
3�� Attach the fill hose / vent line from the filling rig
outlet to filling adapter��
4�� Reset the scale to zero to compensate for weight of
container and fill hose��
5�� Switch on the pump marked ‘Liquid’ on filling
cabinet and fill container to required weight, refer to fill
tolerances table 24�� (less approximately 0��7 kg (1��5 lbs)
which is present in pipework and will be forced through
during pressurisation)�� When the fill is reached switch off
pump��
6�� Remove container from scales, zero scales and
weigh to verify fill is within tolerance, adjust if required��
7�� Attach low pressure switch wires to test box and
regulate nitrogen pressure to 13��8 bar (200 psi) on fill rig
and switch on supply��
8�� Slowly increase the nitrogen pressure on the
approved pressure regulator to the stated pressure on the
filling instruction sheet, making the relevant allowances in
pressure to compensate for the current room temperature
(see the temperature correction chart Table 25)�� Read off
the calibrated external fill pressure gauge to determine
when the intended charging pressure has been reached��
(Check that the container pressure gauge reads within ±
1 bar (± 14��5 psi) of the fill gauge, replace container gauge
if outside this tolerance)��
Caution.
When superpressurising, a pressure
regulator must be used when the pressure source is a
tank of high pressure gas��
Ensure that the test box registers a change in state
(normally open to normally closed or normally closed to
normally open) at approximately 24 bar rising (350 psi)��
9�� Agitate the container to accelerate nitrogen
absorption into the agent and top up the pressure
accordingly�� Switch off nitrogen supply once absorption
has stopped��
10�� Attach the closing down adaptor to the container
valve top cap and connect the nitrogen closing down line��
Regulate the nitrogen pressure to 40 bar (580 psi) with the
fill rig��
11�� Open the closing down valve for 1 second only to
force the valve shuttle down�� The container valve can be
heard to close�� Turn off the nitrogen supply and vent the
closing down line with the needle valve��
12�� Vent the fill hose to atmosphere�� If the pressure
drops to zero as shown on fill rig gauge marked outlet
within 10 seconds, the valve has closed�� (Top up if
necessary)
13�� Remove the closing down line adapter��
14�� If valve does not close after 5 applications, the
cylinder must be de-pressurised�� Ensure vent valve is
closed when not required to prevent contamination on fill
line��
15�� Test all ports with leak detection spray, and
Schrader with water/soap solution��
If a leaks is observed, minor leaks may be cured by
tightening the offending components��
2
SECTION 9 - RECHARGING PROCEDURE
FM-200® (UL/FM)
14A-07H
02
2010-03