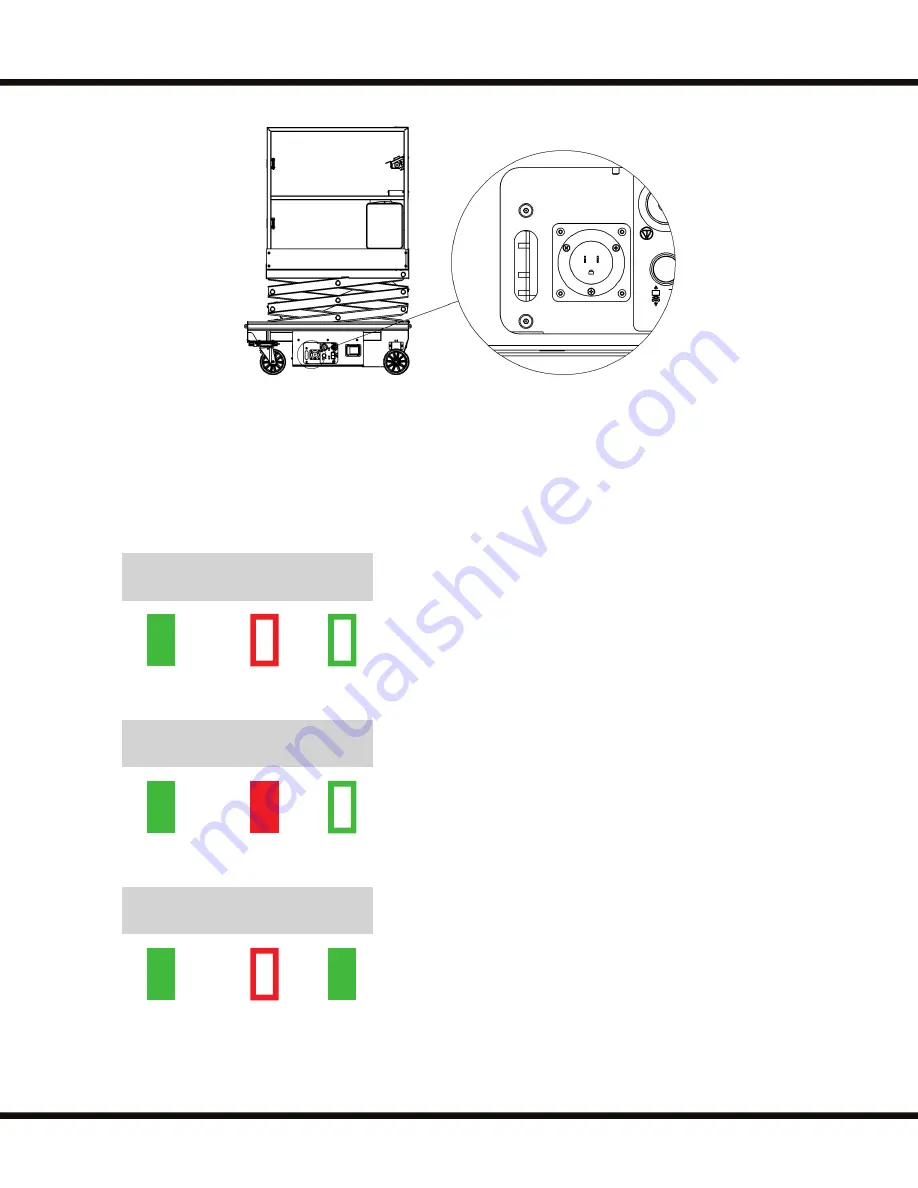
Reading the battery displays
This display indicates that the power is on but there is no connection
to a battery. The charger must see approximately five (5) volts on a
battery to deliver D/C current.
This display indicates that power is on and that the output is delivering
D/C current to the battery.
This display indicates that power is on and that the output is finished
charging and is in a float maintenance model.
FIGURE 19: Battery Charger and Light Locations
Battery solution is at its proper strength when the battery is manufactured. Use distilled water and keep fluid
up to proper level. When required, water should be added to battery after charging, unless water level is
below the plates.
Green LED
(ON)
Red LED
(OFF)
Green LED
(ON)
Red LED
(ON)
Green LED
(OFF)
Green LED
(ON)
Red LED
(OFF)
Green LED
(ON)
POWER
BATTERY 1 STATUS
CHARGING READY
BATTERY 1 STATUS
CHARGING READY
POWER
BATTERY 1 STATUS
CHARGING READY
POWER
Green LED
(OFF)
SECTION 6
OPERATION
31
OPERATION & SAFETY MANUAL
PA1.1-S REV A
Summary of Contents for PA-1030
Page 21: ...THIS PAGE WAS INTENTIONALLY LEFT BLANK 21 OPERATION SAFETY MANUAL PA1 1 S REV A ...
Page 29: ...THIS PAGE WAS INTENTIONALLY LEFT BLANK 29 OPERATION SAFETY MANUAL PA1 1 S REV A ...
Page 34: ...NOTES PUSH AROUND SERIES PA 1030 34 ...
Page 35: ...NOTES 35 OPERATION SAFETY MANUAL PA1 1 S REV A ...