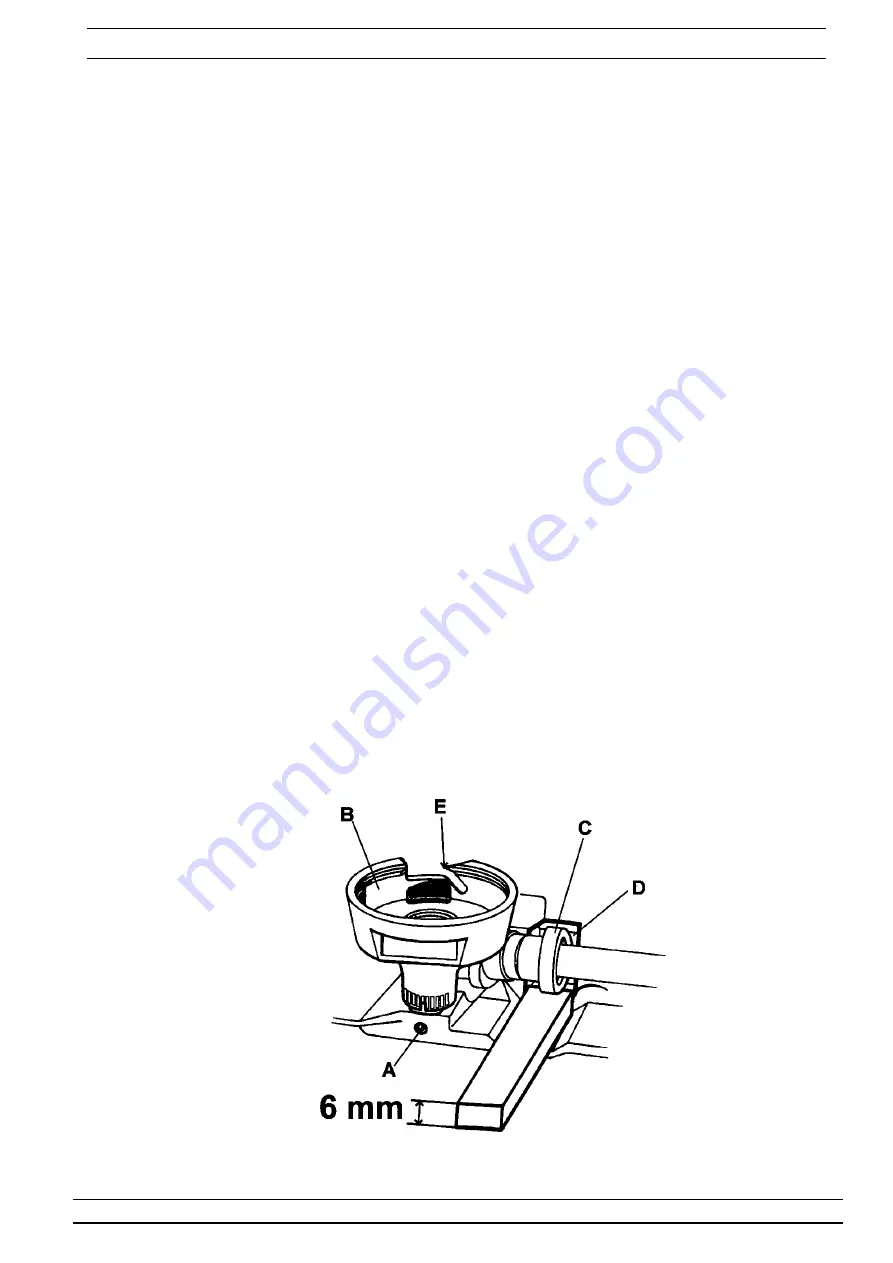
46
47
104 72 57-26
104 72 57-26
Hook compl.
Dismounting
1. Dismount rear cove and front cover .
2. Dismount the feeding step motor.
3. Dismount the feeding unit.
4. Loosen screw (A) and lift hook compl. (B).
Mounting
1. Turn the hand wheel until the highest part (C) of the eccentric points backwards and is within the
recess (D) in the arm, and the gap between the feeding eccentric and the arm is 6 mm (see ill.).
2. Position washer, adjustment stud and dust shield onto the arm. With the adjustment stud forward.
3. Place the hook so that its tip (E) points straight backwards.
4. Press the hook shaft downwards so that it is without play and tighten screw (A).
5. Mount the feeding unit .
Thereafter set:
2.
Setting of the hook in relation to the feeding eccentric.
1.
Play of the hook gear.
6.
Setting of the feed dog in relation to the presser foot.
9.
Gap between the needle and the hook.
13.
Timing of the hook in relation to the needle.
14.
Needle height.
10.
The setting of the stitch plate (hook cover) in relation to the needle in the feeding direction.
11.
The sideways setting of the stitch plate (hook cover) in relation to the feed dog.
12.
The hook height.
15.
Feed dog height.
18.
Stitch length balance.
The hook can be dismounted without removing the feeding step motor and the feeding unit.
Dismount covers, hook cover, presser foot holder, needle and bobbin basket. Loosen the locking
screw of the hook shaft, lift the hook shaft. Lift the feed dog (long stitch length).
Note!
The position of the hook in relation to the lower shaft mustn’t be changed.