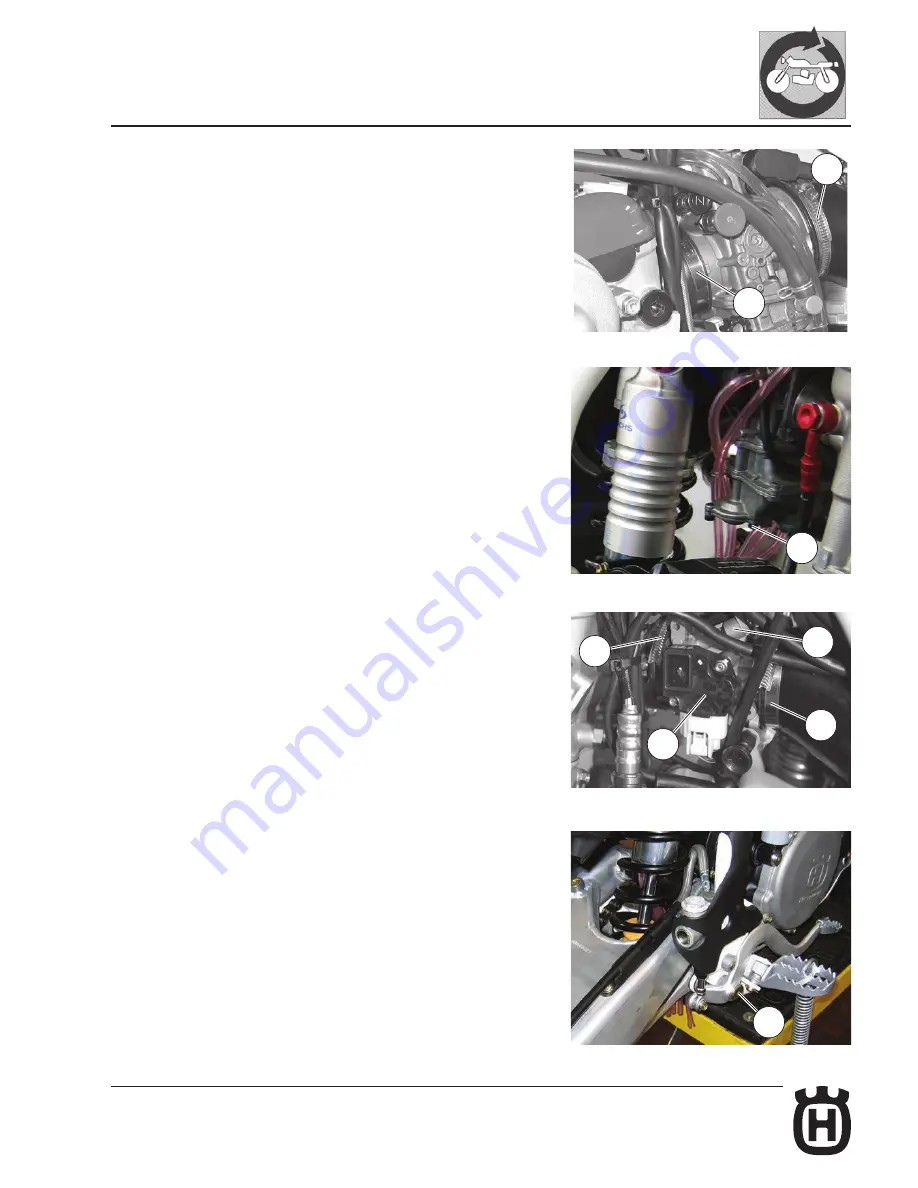
E.9
Part. N. 8000 H0364 (09-2008)
GENERAL OPERATIONS
4) TC-TXC: Loosen the clamps (3) and (4) that fasten the carburetor to the
intake manifold and air filter box manifold. Pull back the carburetor to free it from
the intake manifold and extract the carburetor from the right side of the motorcy-
cle. Remove the carburetor floater chamber lower screw (5), the floater cham-
ber then eliminate the remaining gasoline.
4
Remove the fastening pin (8) and the rear brake pedal.
4) TE-SMR: loosen the left clamp (1) of the sleeve on the throttle body and the
front clamp (2) on the cylinder head. Disconnect the connector from the M.A.Q.S.
(6) on the throttle body of the main cable. Remove the throttle body (7); when
reassembly the throttle body, adjust the T.P.S. again (see chapter S).
1
2
3
7
6
5
8
Summary of Contents for 2009 TE 250
Page 6: ...a 4 Part N 8000 H0368 09 2008 FOREWORD SUMMARY ...
Page 7: ...b 1 Part N 8000 H0368 09 2008 IMPORTANT NOTICES Section b ...
Page 10: ...b 4 Part N 8000 H0368 09 2008 IMPORTANT NOTICES ...
Page 11: ...A 1 Part N 8000 H0368 09 2008 GENERAL Section A ...
Page 20: ...A 10 Part N 8000 H0368 09 2008 GENERAL ...
Page 21: ...B 1 Part N 8000 H0368 09 2008 MAINTENANCE Section B ...
Page 29: ...C 1 Part N 8000 H0368 09 2008 TROUBLES AND REMEDIES Section C ...
Page 34: ...C 6 Part N 8000 H0368 09 2008 TROUBLES AND REMEDIES ...
Page 35: ...SETTINGS AND ADJUSTMENTS Part N 8000 H0368 09 2008 D 1 Section D ...
Page 37: ...SETTINGS AND ADJUSTMENTS Part N 8000 H0368 09 2008 D 3 TC TXC TE SMR ...
Page 69: ...E 1 Part N 8000 H0364 09 2008 GENERAL OPERATIONS Section E ...
Page 95: ...F 1 Part N 8000 H0368 09 2008 ENGINE DISASSEMBLY Section F ...
Page 97: ...F 3 Part N 8000 H0368 09 2008 ENGINE DISASSEMBLY ...
Page 120: ...F 26 Part N 8000 H0368 09 2008 ENGINE DISASSEMBLY ...
Page 147: ...H 1 Part N H0368 09 2008 ENGINE REASSEMBLY Section H ...
Page 189: ...H 43 Part N H0368 09 2008 ENGINE REASSEMBLY ...
Page 191: ...I 1 Part N 8000 H0368 09 2008 FRONT SUSPENSION Section I ...
Page 193: ...I 3 Part N 8000 H0368 09 2008 FRONT SUSPENSION TE SMR TC TXC ...
Page 240: ...I 50 Part N 8000 H0368 09 2008 FRONT SUSPENSION ...
Page 258: ...J 18 Part N 8000 H0368 09 2008 REAR SUSPENSION ...
Page 259: ...L 1 Part N 8000 H0368 09 2008 BRAKES Section L ...
Page 268: ...L 10 Part N 8000 H0368 09 2008 BRAKES SMR TE TC TXC ...
Page 270: ...L 12 Part N 8000 H0368 09 2008 BRAKES ...
Page 277: ...M 7 Part N 8000 H0368 09 2008 ELECTRIC SYSTEM DIGITAL INSTRUMENT 5 19 22 21 13 11 9 20 ...
Page 279: ...M 9 Part N 8000 H0368 09 2008 ELECTRIC SYSTEM DIGITAL INSTRUMENT 6 5 10 11 7 9 9 8 ...
Page 326: ...M 56 Part N 8000 H0368 09 2008 ELECTRIC SYSTEM DIGITAL INSTRUMENT ...
Page 327: ...N 1 Part N 8000 H0368 09 2008 ENGINE COOLING SYSTEM Section N ...
Page 332: ...N 6 Part N 8000 H0368 09 2008 ENGINE COOLING SYSTEM ...
Page 370: ...P 2 Part N 8000 H0368 09 2008 HYDRAULIC CONTROL CLUTCH ...
Page 374: ...P 6 Part N 8000 H0368 09 2008 HYDRAULIC CONTROL CLUTCH ...
Page 375: ...Q 1 Part N 8000 H0368 09 2008 OPTIONAL PARTS LIST Section Q ...
Page 378: ...Q 4 Part N 8000 H0368 09 2008 OPTIONAL PARTS LIST ...
Page 385: ...T 1 Part N 8000 H0368 09 2008 LUBRICATION SYSTEM Section T ...
Page 387: ...T 3 Part N 8000 H0368 09 2008 LUBRICATION SYSTEM LUBRICATION SYSTEM DIAGRAM ...
Page 388: ...T 4 Part N 8000 H0368 09 2008 LUBRICATION SYSTEM ...
Page 389: ...W 1 Part N 8000 H0368 09 2008 SPECIFIC TOOLS Section W ...
Page 412: ...Y 16 Part N 8000 H0368 09 2008 FRAME AND WHEELS ...