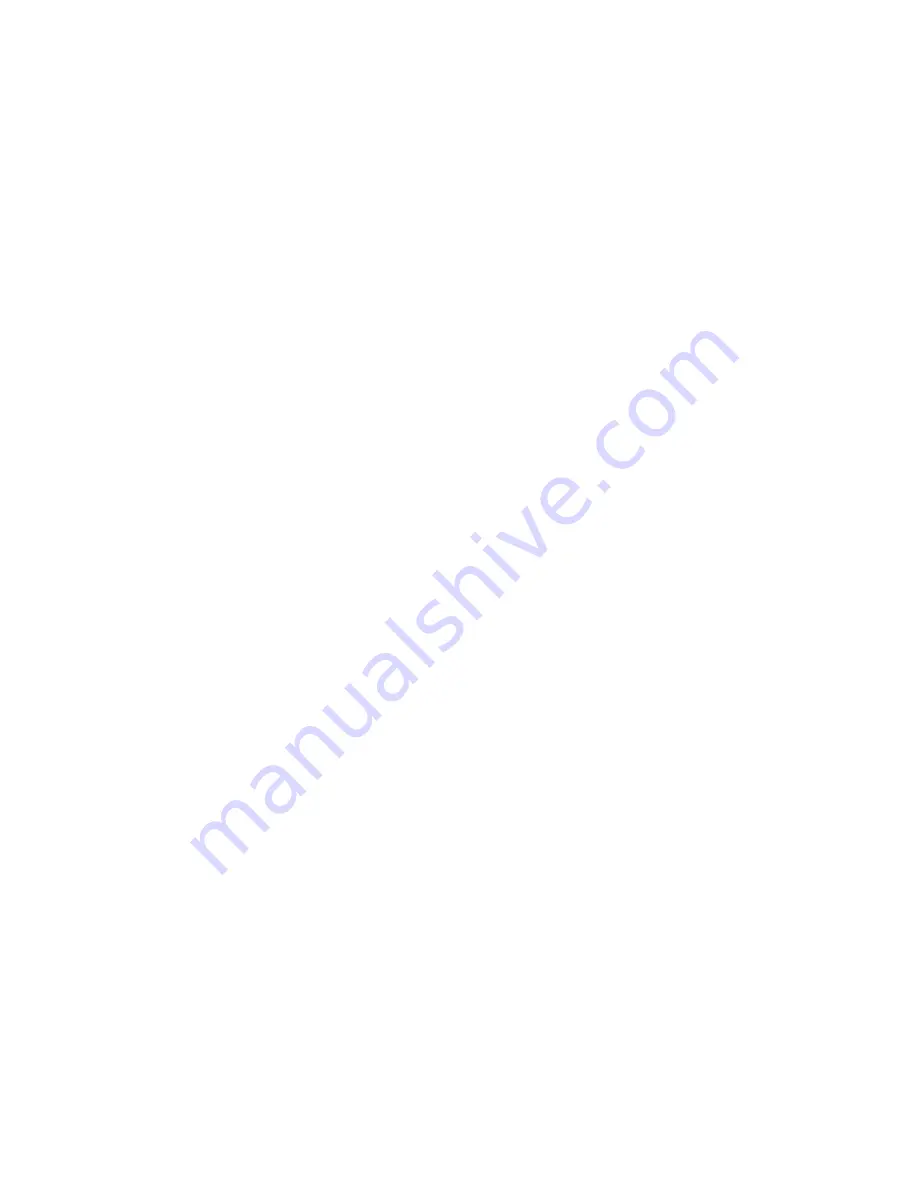
ALL SEASON AIR CONDITIONING SYSTEM
25
If the system operates normally, move the
service valves to the operating position.
Remove the gauge lines and cap the gauge port
fittings.
CHECKING AND ADDING OIL
In normal operation, a small amount of oil is
always circulating throughout the refrigerat-
ing system. An oil sight glass is provided in
the compressor so that you can see if the oil
is splashing when the compressor is running.
It does not indicate the oil level when the
compressor is stopped. The oil level is
determined by stopping the compressor and
closing the suction and discharge service
valves to the lines. This isolates the
compressor from the rest of the system and
leaves the system sealed from the atmosphere.
Loosen the gauge port cap on the discharge
service valve slightly and let the gas in the
compressor purge to the air slowly until the
charge in the compressor is released. Relieve
the crankcase pressure by loosening the oil
filler plug slowly and remove it when oil has
stopped foaming.
The usual charge of oil in the compressor
is 10 ounces. Should it be necessary to add
oil, use a refrigerant type oil of 280 to 300
Seybolt. Use a straight piece of wire as a
dipstick. Check at the oil filler hole. Use
the wire dipstick as near vertical as possible.
To avoid adding too much oil, add slowly and
check with dip stick; take two or three
readings, each time wiping the dipstick dry.
The following should be used to determine
the correct oil level with the compressor warm
and stopped.
Vertical Mounted Type ("Rambler", "Wasp",
and "Hornet" 6)
Minimum 9 Oz. Avdp. 1-1/8" on Stick
Maximum 10 Oz. Avdp. 1-1/2" on Stick
Horizontal Mounted Type ("Hornet" V-8)
Minimum 9 Oz. Avdp. 1-1/4" on Stick
Maximum 10 Oz. Avdp. 1-9/16" on Stick
Replace oil filler plug.
"Crack" the suction service valve slightly
for approximately a few seconds until a
hissing sound is heard from the valve to allow
the system to purge air from the compressor
through the discharge service port.
Tighten the discharge service valve port cap.
After the air has been purged from the
system, return the service valves to the
operating position.
Install valve stem caps; operate system and
allow to run a few minutes. Observe the oil
splash in the sight glass of the compressor.
There should be oil splash if there is
sufficient oil in the system.
NOTE: The refrigerant charge should be
checked whenever oil is added to the
compressor.
CAUTION:
The oil in the container origi-
nally is packed moisture free and every
effort should be made to maintain its
status. The oil will quickly absorb any
moisture with which it comes in contact.
The container should not be opened until
ready for use, and be recapped immedi-
ately after use. Tools, tubes, gauge
sets, and replacement parts should be
kept clean. The system should not be open
any longer than absolutely necessary.
Oil Level When Replacing Compressor
Precautions should be taken to prevent an over
or under charge of oil whenever the compressor
is replaced. The oil charge in a new compres-
sor is sufficient for an entire system. In a
system that has been running, there is always
some oil circulating through it.
Purge the gas pressure in the crankcase of
the original compressor to 0 pounds pressure
slowly after the line valves are closed.
Check the oil level without running the
compressor. Running the compressor will cause
a sudden drop in pressure in the crankcase and
may cause oil pumping. The oil level in the
crankcase would then be temporarily lowered,
putting an over-charge of oil in the evapora-
tor, so a false reading is obtained when
checking the oil level.
Check the oil level in the new compressor
and add or remove oil from it until the oil
level is the same as it is in the compressor
to be replaced.
After the new compressor has been run for 10
or 15 minutes, recheck the oil level.
MOISTURE AND AIR IN THE SYSTEM
Presence of air and moisture in the system is
harmful. Precautions should be exercised to
prevent both from entering the system. Mois-
ture and air often enter together because in
all air there is more or less water vapor along
with the oxygen, nitrogen, and other gases of
which air is composed. Moisture and air may
enter through leaky shaft seals, faulty tubing
connections, defective gasket joints, and
other leaks. It can get in during service
operations which are incorrectly performed and
during installation of equipment. Water or
moisture may enter with refrigerants or oil
which has been allowed to gain water through
contact with air. As a precaution, the
compressor oil container should only be opened
when in use.
Water causes the most serious troubles.
Water does not dissolve in Freon-12 but
separates and remains apart from the refriger-
ant. Consequently, the separated water is
likely to freeze into ice and clog the small
openings in the expansion valve. Ice in the
expansion valve orifice stops flow of refrig-
erant. Then the evaporator and valve warm up,
the ice melts, and refrigeration once more
takes place, only to be stopped again as more
Summary of Contents for 1955 Rambler
Page 1: ......
Page 2: ......
Page 3: ......
Page 4: ......
Page 28: ......
Page 38: ......
Page 42: ......
Page 87: ...46 T E C H N I C A L S E R V I C E M A N U A L...
Page 88: ...ELECTRICAL WIRING DIAGRAMS...
Page 89: ......
Page 90: ......
Page 91: ...ELECTRICAL WIRING DIAGRAMS...
Page 92: ......
Page 93: ......
Page 94: ......
Page 95: ......
Page 96: ......
Page 97: ......
Page 98: ......
Page 99: ......
Page 100: ......
Page 101: ......
Page 102: ......
Page 103: ......
Page 119: ......
Page 127: ......
Page 151: ...OVERDRIVE 5...
Page 165: ......
Page 179: ......
Page 199: ......
Page 200: ...2 TECHNICAL SERVICE MANUAL...
Page 223: ......
Page 243: ......
Page 251: ......
Page 255: ...ALL SEASON AIR CONDITIONING SYSTEM 5 Figure 2 Freon 12 Temperature Pressure Relation Curve...
Page 287: ......
Page 288: ......
Page 289: ......
Page 291: ......
Page 292: ......