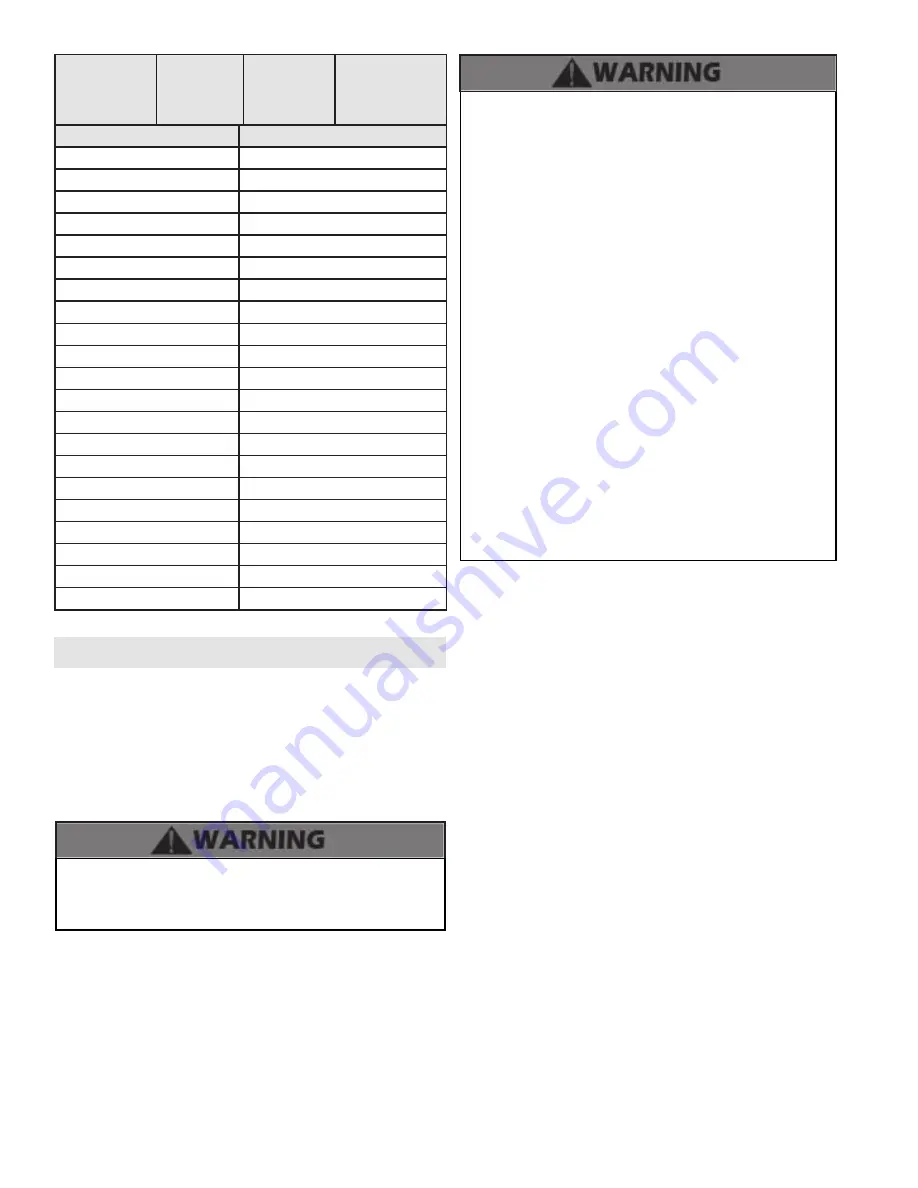
LP-551 Rev. 3.9.16
54
Supply
Temperature
Sensor
(7700P-073)
Indirect
Sensor
(7250P-325)
Return
Sensor
(7250P-667)
Dual Flue
Temperature
Sensor
(7450P-176)
Temperature (
o
F)
Resistance (ohms)
32
32624
41
25381
50
19897
59
15711
68
12493
77
10000
86
8056
95
6530
104
5324
113
4365
122
3599
131
2982
140
2483
149
2079
158
1748
167
1476
176
1252
185
1066
194
912
203
782
212
674
Table 32 - Sensor Temperature Resistance
Part 12 - Maintenance
A. Procedures
Periodic maintenance should be performed once a year by a
qualified service technician to assure that all the equipment
is operating safely and efficiently. The owner should make
necessary arrangements with a qualified heating contractor
for periodic maintenance of the boiler. The installer must also
inform the owner that a lack of proper care and maintenance of
the boiler may result in a hazardous condition.
BEFORE EACH HEATING SEASON a trained and qualified
service technician should perform the inspections as per the
boiler inspection and maintenance schedule in this manual.
Failure to do so could result in death or serious injury.
The combustion chamber insulation in this product contains
ceramic fiber material. Ceramic fibers can be converted
to cristobalite in very high temperature applications. The
International Agency for Research on Cancer (IARC) has
concluded, “Crystalline silica inhaled in the form of quartz
or cristobalite from occupational sources is carcinogenic to
humans (Group 1).”
•
Avoid breathing dust and contact with skin and eyes.
•
Use a NIOSH certified dust respirator (N95). This type
of respirator is based on the OSHA requirements for
cristobalite at the time this document was written. Other
types of respirators may be needed depending on job
site conditions. Current NIOSH recommendations can
be found on the NIOSH website: http://www.cdc.gov/
niosh/homepage.html. NIOSH approved respirators,
manufacturers, and phone numbers are also listed on
this website.
•
Wear long-sleeved, loose fitting clothing, gloves, and
eye protection.
•
Apply enough water to the combustion chamber lining
to prevent dust.
•
Wash potentially contaminated clothes separately from
other clothing. Rinse clothes washer thoroughly.
NIOSH stated First Aid.
•
Eye: Irrigate immediately.
•
Breathing: Fresh air.
B. Combustion Chamber Coil Cleaning Instructions
*Before beginning this procedure, have on hand the following
items:
•
a nylon, stainless steel, or brass brush (not steel)
•
gloves and eye protection
1. Shut down the boiler by using the following steps:
a. Close the gas valve. Shut down the unit, and wait for it to
be cool to the touch.
b. Disconnect the condensate piping from the outside
connection, (not from the boiler side), so flow from
condensate reservoir can be observed.
c. Disconnect electrical connections from the gas valve,
spark electrode, flame rectification probe, and combustion
blower.
d. Remove the four (4) screws on the aluminum ¾” NPT
connector on the right side of the gas valve.
e. Disconnect the wiring connected to the combustion
blower motor.
f. Remove the six (6) 10MM nuts from the burner plate
assembly.
g. Pull the entire burner plate assembly with blower still
attached towards you, while removing or pushing aside
any wiring to allow removal of the assembly.
2. Spray the coils liberally with a spray bottle filled with clear
tap water. Confine the spray to the area being cleaned. Avoid
getting the ceramic target wall wet. If the condensate system
is blocked, use a vacuum to clear it.
3. Scrub coils of any buildup with a nylon, stainless steel, or
brass brush. Do not use a steel brush. Vacuum the debris from
the coils.
4. Spray the coils again with clear tap water. Confine the spray
Summary of Contents for EP-220 VWH
Page 33: ...LP 551 Rev 3 9 16 33 Figure 24 Cascade Master and FollowerWiring ...
Page 34: ...LP 551 Rev 3 9 16 34 Figure 25 Internal Connection Diagram ...
Page 57: ...LP 551 Rev 3 9 16 57 Figure 30 Combustion System Replacement Parts 220kBTU Model ...
Page 58: ...LP 551 Rev 3 9 16 58 Figure 31 Combustion System Replacement Parts 299 399kBTU Models ...
Page 59: ...LP 551 Rev 3 9 16 59 Figure 32 Replacement Parts All Models ...