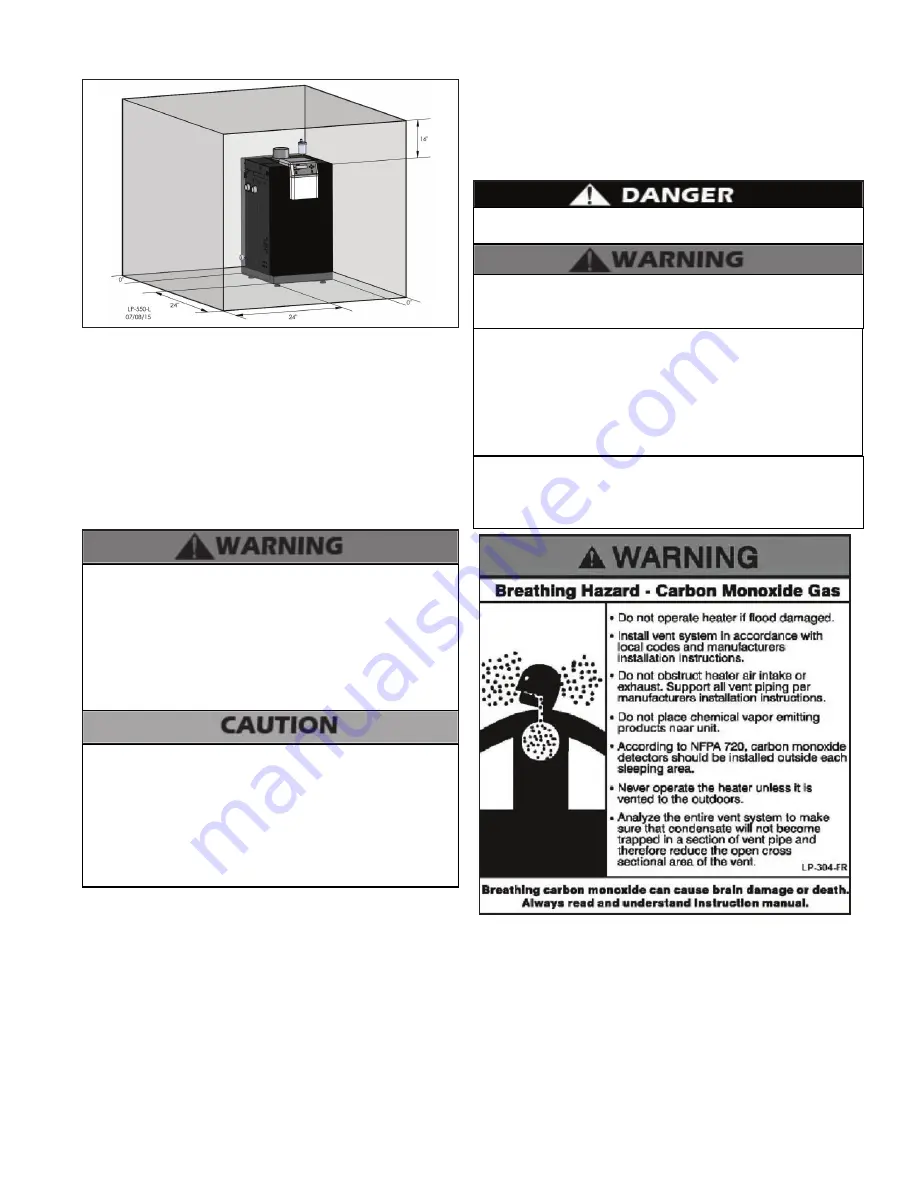
LP-551 Rev. 3.9.16
9
D. Clearances for Service Access
NOTE:
If you do not provide the minimum clearances shown
in Figure 2 it might not be possible to service the boiler without
removing it from the space.
NOTE:
A combustible door or removable panel is acceptable
front clearance.
Minimum Clearances from Combustible Materials
•
Hot water pipes - at least 1” from combustible materials
•
Exhaust vent pipe - at least 1” from combustible
materials
Figure 2 - Recommended Service Clearances
All boilers eventually leak. It is recommended to install a
catch pan beneath the boiler. This catch pan should be sized
with a maximum depth of 2”, and a minimum diameter 2”
greater than the diameter of the boiler. The catch pan should
empty into an open drain line. This drain line should be 3/4”
ID minimum, piped to an open drain. Failure to follow these
instructions could result in property damage. Such damages
ARE NOT covered by product warranty.
The space must be provided with combustion / ventilation air
openings correctly sized for all other appliances located in the
same space as the boiler. The boiler cover must be securely
fastened to prevent the boiler from drawing air from the
boiler room. This is particularly important if the boiler is in a
room with other appliances. Failure to comply with the above
warnings could result in substantial property damage, severe
personal injury, or death.
E. Residential Garage Installation
Precautions
If the boiler is located in a residential garage, per ANSI Z223.1:
•
Install the boiler burner and ignition devices a mini-
mum of 18” above the floor of the garage. This will
ensure the burner and ignition devices are well off the
floor.
•
When raising the boiler ensure the entire bottom and
fully filled weight of the boiler are fully supported.
•
Locate or protect the boiler so it cannot be damaged
by a moving vehicle.
F. Exhaust Vent and Intake Pipe
The boiler is rated ANSI Z21.13 Category IV (pressurized vent,
Failure to vent the boiler properly will result in serious personal
injury or death.
Do not attempt to vent this boiler by any means other than
those described in this manual. Doing so will void the warranty
and may result in severe personal injury or death.
Vents must be properly supported. Boiler exhaust and intake
connections are not designed to carry heavy weight. Vent
support brackets must be within 1’ of the boiler and the balance
at 4’ intervals. Boiler must be readily accessible for visual
inspection for first 3’ from the boiler. Failure to properly support
vents could result in property damage, severe personal injury,
or death.
The exhaust discharged by this boiler may be very hot. Avoid
touching or other direct contact with the exhaust gases of the
vent termination assembly. Doing so could result in severe
personal injury or death.
1. Direct Vent of Exhaust and Intake
If installing a direct vent option, combustion air must be drawn
from the outdoors directly into the boiler intake and exhaust
must terminate outdoors. There are three basic direct vent
options detailed in this manual: 1. Side Wall Venting, 2. Roof
Venting, and 3. Unbalanced Venting.
Be sure to locate the boiler such that the exhaust vent and
intake piping can be routed through the building and properly
terminated. Different vent terminals can be used to simplify and
eliminate multiple penetrations in the building structure (see
Optional Equipment in Venting Section). The exhaust vent and
intake piping lengths, routing, and termination methods must
likely to form condensate in the vent) and requires a special vent
system designed for pressurized venting.
NOTE: The venting options described here (and further
detailed in the Venting section, this manual) are the lone
venting options approved for this boiler. Failure to vent the
boiler in accordance with the provided venting instructions
will void the warranty.
Summary of Contents for EP-220 VWH
Page 33: ...LP 551 Rev 3 9 16 33 Figure 24 Cascade Master and FollowerWiring ...
Page 34: ...LP 551 Rev 3 9 16 34 Figure 25 Internal Connection Diagram ...
Page 57: ...LP 551 Rev 3 9 16 57 Figure 30 Combustion System Replacement Parts 220kBTU Model ...
Page 58: ...LP 551 Rev 3 9 16 58 Figure 31 Combustion System Replacement Parts 299 399kBTU Models ...
Page 59: ...LP 551 Rev 3 9 16 59 Figure 32 Replacement Parts All Models ...