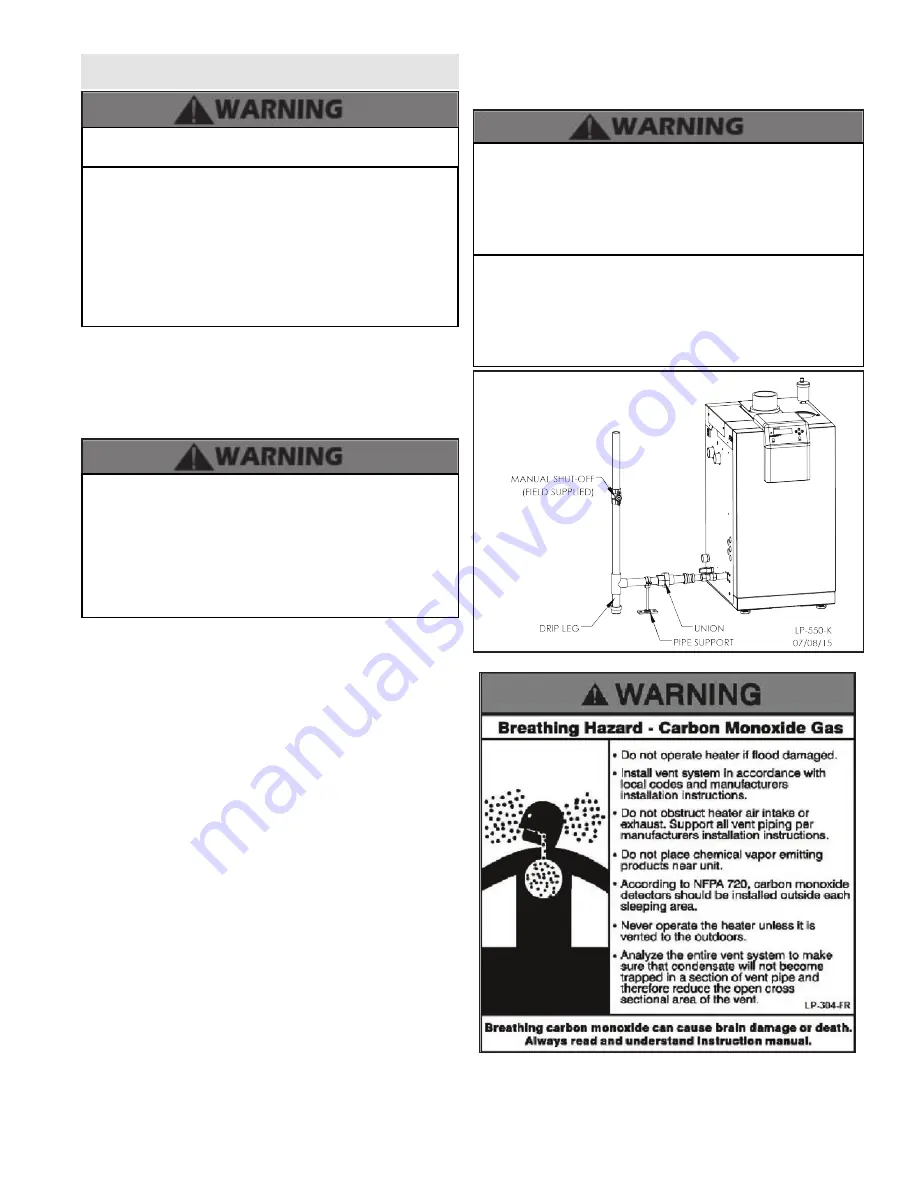
LP-551 Rev. 3.9.16
35
Part 7 - Gas Connections
Failure to follow all precautions could result in fire, explosion,
severe injury, or death.
It is very important that you are connected to the type of
gas noted on the rating plate. “LP” for liquefied petroleum,
propane gas, or “NG” for natural or city gas. Do not do a gas
conversion without an approved gas conversion kit. Follow
the included instructions VERY carefully if converting the
boiler. Prior to turning the gas on, all gas connections must
be approved by the local gas supplier or utility, in addition to
the governing authority. Failure to follow these instructions
could result in property damage, serious injury, or death.
The gas supply shall have a maximum inlet pressure of less
than 14” w.c. (3.5 kPa), and a minimum of 3.5” w.c. (.87 kPa).
The entire piping system, gas meter and regulator must be
sized properly to prevent pressure drop greater than 0.5” (.12
kPa) as stated in the National Fuel Gas Code. This information
is listed on the rating label.
UL recognized fuel gas detectors are recommended in
all enclosed propane and natural gas applications where
there is a potential for an explosive mixture of fuel gas to
accumulate. The installation of these detectors should
be made in accordance with the detector manufacturer’s
recommendations, and/or local laws. Failure to install fuel gas
detectors in these applications could result in fire, explosion,
property damage, severe personal injury, or death.
A. Gas Piping
1. Run the gas supply line in accordance with all applicable
codes.
2. Locate and install manual shutoff valves in accordance with
state and local requirements.
3. In Canada, the Manual Shutoff must be identified by the
installing contractor.
4. It is important to support gas piping as the unit is not
designed to structurally support a large amount of weight.
5. Purge all gas lines thoroughly to avoid start up issues with
air in the lines.
6. Sealing compound must be approved for gas connections.
Support gas supply piping with hangers, not by the boiler or its
accessories. The boiler gas valve and blower will not support the
weight of the piping. Make sure the gas piping is protected from
physical damage and freezing, where required. Failure to follow
these instructions could result in gas leakage, and result in fire,
explosion, property damage, severe personal injury, or death.
Do not use Teflon tape on gas line pipe thread. Use a pipe
compound rated for use with natural and propane gases. Apply
sparingly on male pipe ends, leaving the two end threads bare
and flow unobstructed. Failure to follow these instructions could
result in gas leakage or blockage, and result in fire, explosion,
property damage, severe personal injury, or death.
Figure 26 - Gas Connection
The gas connection on the boiler is 3/4” for 80/110/150 models
and 1” for 220/299/301/399 models. It is mandatory that this
fitting is used for connection to a field fabricated drip leg as
shown in the illustratioN per the National Fuel Gas Code. You
must ensure that the entire gas line to the connection at the
boiler is no smaller than the unit supplied connection.
Once all inspections have been performed, the piping must
be leak tested. If the leak test requirement is a higher test
pres¬sure than the maximum inlet pressure, you must isolate
the boiler from the gas line. In order to do this, shut the gas
off using factory and field-installed gas cocks. This will prevent
high pressure. Failure to do so may damage the gas valve. In
the event the gas valve is exposed to a pressure greater than
½ PSI, 14” w.c. (3.5 kPa), the gas valve must be replaced.
Never use an open flame (match, lighter, etc.) to check gas
connections.
Care must be taken when applying compound to prevent
blockage or obstruction of gas flow which may affect the
operation of the unit.
Summary of Contents for EP-220 VWH
Page 33: ...LP 551 Rev 3 9 16 33 Figure 24 Cascade Master and FollowerWiring ...
Page 34: ...LP 551 Rev 3 9 16 34 Figure 25 Internal Connection Diagram ...
Page 57: ...LP 551 Rev 3 9 16 57 Figure 30 Combustion System Replacement Parts 220kBTU Model ...
Page 58: ...LP 551 Rev 3 9 16 58 Figure 31 Combustion System Replacement Parts 299 399kBTU Models ...
Page 59: ...LP 551 Rev 3 9 16 59 Figure 32 Replacement Parts All Models ...