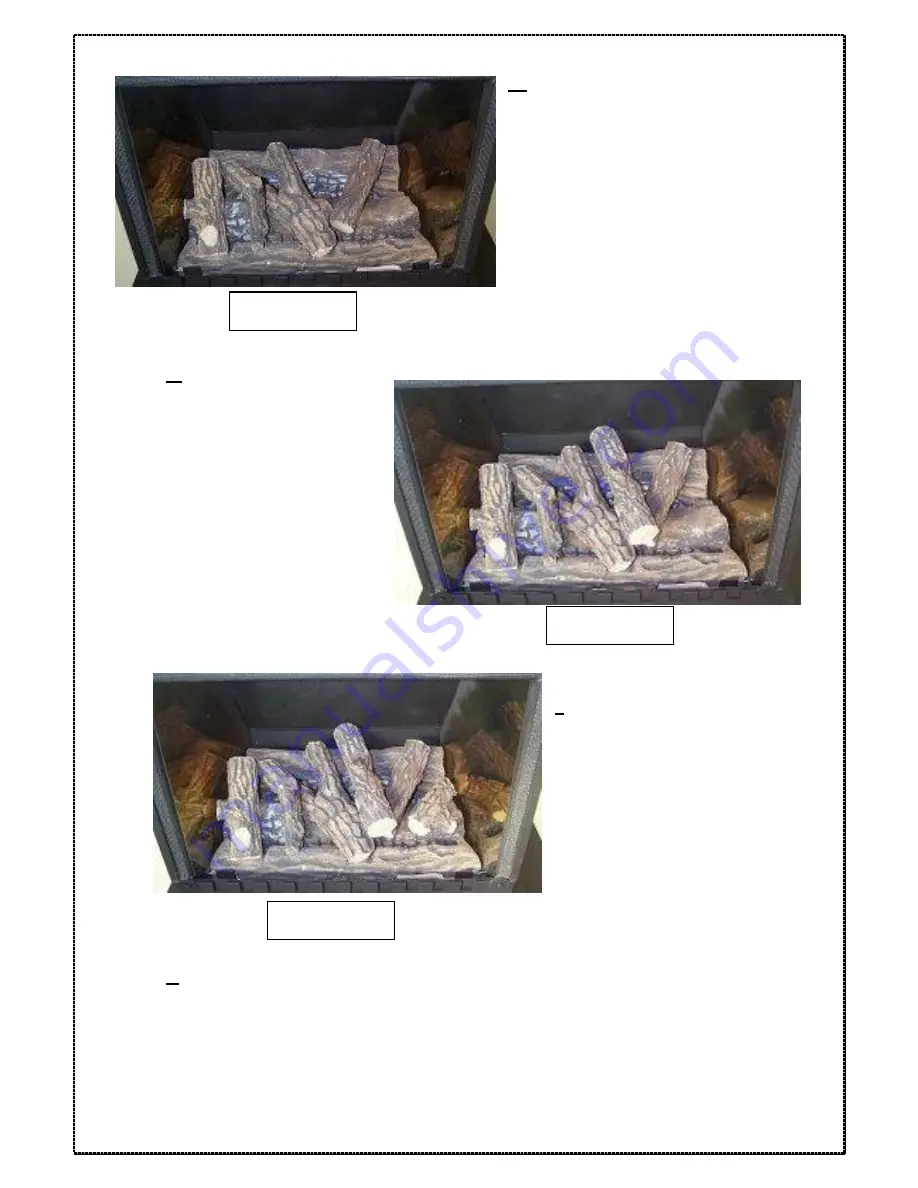
RevE 18/02/14
15
G.
The fourth log is the shorter of the
two straight logs and sits in the notch
on the large log between the trunk
and the short branch, as shown in
diagram B14. The log should rest on
the middle ceramic on the flat
section to the right of the large log.
The top of the log should rest in the
groove on the rear ceramic, again
as shown in diagram B14.
H.
The fifth log is the
longer of the two straight
logs, the top of this should
sit in the final groove on
the rear ceramic in
between the large log
and the shorter straight
log. The log should also
rest on the join between
the small branch on the
large log and the smaller
straight log. This can be
seen in diagram B15.
I.
The sixth and final log
has a single branch
coming from it and one
end is shaped to be
parallel with the
mirrored side. It should
sit on the flat surface on
the centre ceramic as
shown in diagram B16.
J.
The fire-bed should now be completed. The stove should be lit and the
flame picture checked with the glass panel fixed securely in place. Any
adjustments to the flame picture can then be made as required.
Diagram B14
Diagram B15
Diagram B16