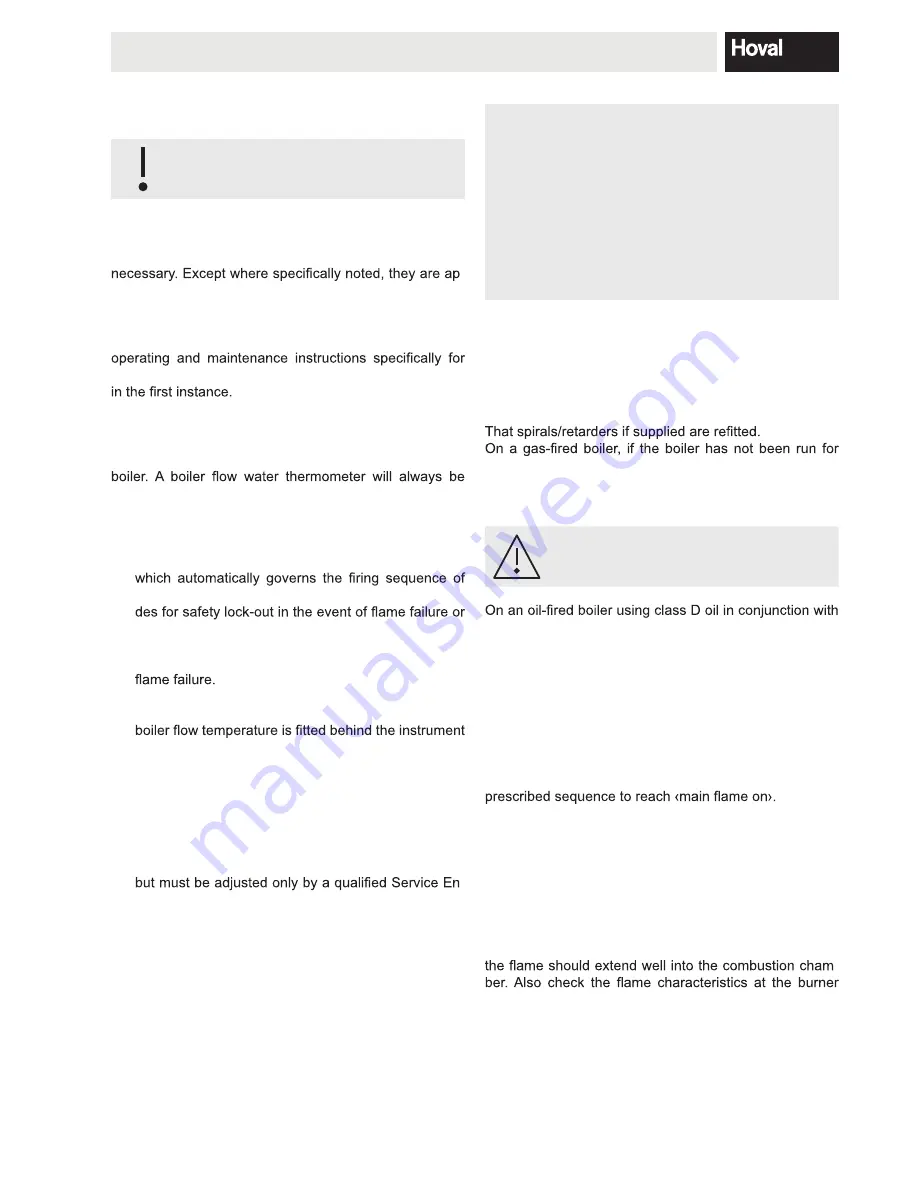
35
4 214 283 / 00
OVERVIEW OF SETTINGS
6.2 Operating
Instructions
PLEASE READ: Important Notes for the
Boiler Attendant
These instructions are the minimum necessary to enable
an operator to start, run and stop the boiler.
They cover also the simple routine servicing procedures
-
plicable irrespective of the fuel used - gas or oil - BS class
D (35 sec).
If the heating system designer or installer has prepared
the whole plant, those instructions should be referred to
Instruments and Controls
Instruments are generally mounted at the top front of the
present, an altitude gauge may also be provided.
The basic controls for any boiler will be:
a. A sequence-control box (mounted on the burner)
pre-purge, ignition, pilot or reduced start, and provi-
other unsafe condition.
This control box will have advisible indication of lock
out and a manual-reset button for use in the event of
b. A control thermostat which allows adjustment of the
panel facia to discourage unauthorised adjustment
after it has been set by the commissioning engineer.
c. A safety-limit thermostat which comes into operation
should the control thermostat fail to shut the burner
down.The limit stat is usually set at 10°C above the
control thermostat’s maximum setting. No automatic
control may be interfered with by the boiler attendant
-
gineer.
There may be special burner controls equipment or
additional controls to be integrated with the standard
burner control equipment. The function and setting
of these will be covered by the suppliers e.g. BMS.,
sequence controls high and low pressure switches
and water level controls, associated with indepen-
dendently pressurised systems.
Sequencing of boilers under BMS control.
When a bank of boilers are sequenced to operate un-
der the dictates of a BMS control system, it is very im-
portant that on-line boilers are properly matched to
the available heating load at any one time.
This will avoid too frequent cycling of the burners as
they stop and start (introducing cold pre and post
purge air into the boiler each time this happens).
Over time this can result in the boilers suffering from
thermal shock and premature failure of the pressure
parts.
6.2.1 Starting up after cleaning the boiler or a Sum-
mer shut down.
Ensure that fuel lines are fully purged and that fuel is
available at the burner at the correct pressure and tem-
perature.
some time, or if a fuel supply pipe has been disconnec-
ted, purge the piping via the bleed nipple up stream of the
burner to ensure that a gas/air mixture is avoided.
NOTE:
A gas/air mixture is dangerous as it will
explode if subjected to a spark.
a singlepipe supply system, ensure that air is bled from
the system if the oil pipe has been disconnected.
Ensure fuel supply valves are open. Where a pump is in-
corporated in an oil fuel supply system, ensure the pump
is switched ON. Check all switches, e.g. time switch, and
thermostats are in the ‘calling’ for heat condition. Switch
ON electrical supply to the burner at the main switch.
Switch the control panel mounted switch to ON. The bur-
ner control box should now monitor the burner through its
Normal Running
The boiler will switch on/off under the dictates of the con-
trol thermostat. The boiler temperature at any particular
moment can be seen from the boiler thermometer.
Allow the boiler to reach its set temperature and then
-
through the burner inspection window. If any deterioration
is noted, the heating engineer should ensure the neces-
sary action is taken.
check the burner flame through boiler door sight glass;