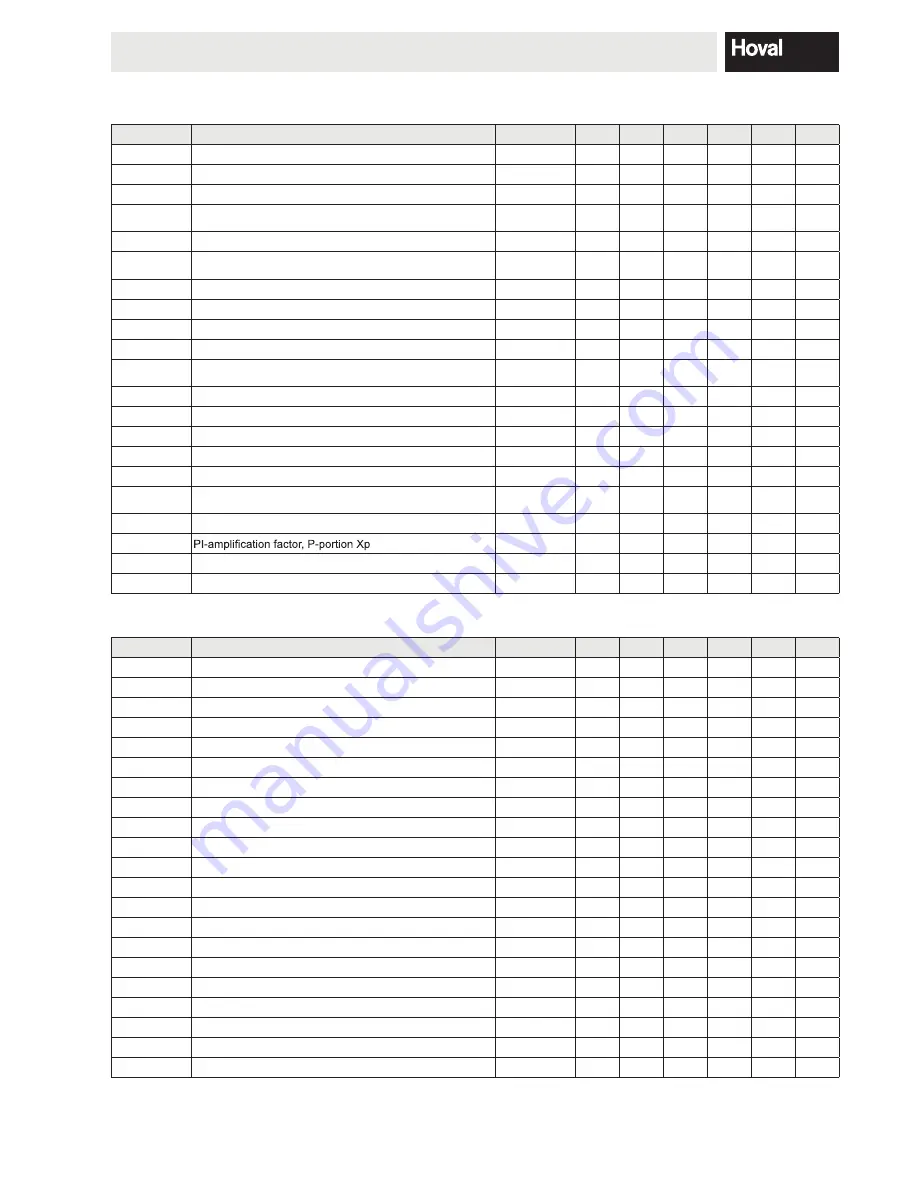
49
4 214 283 / 00
OVERVIEW OF SETTINGS
DHW
Par.
Designation
Factory
10
20
30
40
50
Lev.
DHW-NIGHT DHW - economy temperature
40/ 45 °C
BE
2
DHW-legionella protection-day
OFF
HF
3
DHW-egionella protection-time
2:00
HF
4
DHW-legionella protection-temperature
50/ 55/ 65/
70 °C
HF
5
DHW-temperature recording
1
HF
6
DHW-maximum temperature limit
50/ 55/ 65/
70 °C
HF
7
DHW-mode of operation
1
HF
8
DHW-tank discharge protection
ON/ OFF
HF
9
DHW-charging temperature excess
7/ 20 K
HF
10
DHW-switching difference
5 K
OEM
11
DHW-charging pump follow-on
0.5/ 1/ 2/ 5
min
OEM
12
ZKP-switching time program
AUTO
HF
13
ZKP-economy interval (pause)
0 min
HF
14
ZKP-economy interval (period duration)
20 min
HF
17
H-GEN behaviour during SLP follow-on time
AUTO/ OFF
HF
18
DHW-parallel loading
OFF
HF
19
DHW-time-out
OFF/
30 min
HF
20
PI-reference value control
OFF
HF
21
0,1 %/ K
OEM
22
PI-scanning time Ta
20 s
OEM
23
PI -reset time Tn
600 s/ °C
OEM
UNMIXED CIRC
Par.
Designation
Factory
10
20
30
40
50
Lev.
1
Type of reduced operation
ECO/ ABS
HF
2
Heating system (exponent)
DK= 1,30
HF
3
Room override (in connection with room sensor)
3
HF
4
Room factor
OFF
HF
5
Adaptation heating curve
OFF
HF
6
Switch-on optimisation
1
HF
7
Heating limit
0,5
OEM
8
Room frost protection limit
10 °C
HF
9
Room thermostat function
OFF
HF
10
Outside temperature allocation
0
HF
11
Constant temperature reference value
20 °C
HF
12
Minimum temperature limit
10 °C
HF
13
Maximum temperature limit
55/ 75 °C
HF
14
Temperature elevation Heating circuit
DK=0
HF
15
Pump follow-on
5 min
HF
16
Screed function
OFF
HF
23
Room control K-factor
8
HF
24
Room control Tn-factor
35 min
HF
25
Vacation mode
STBY
HF
36
Minimum value override
OFF
HF
Name heating circuit (max. 5 letters)
XXXXX
HF