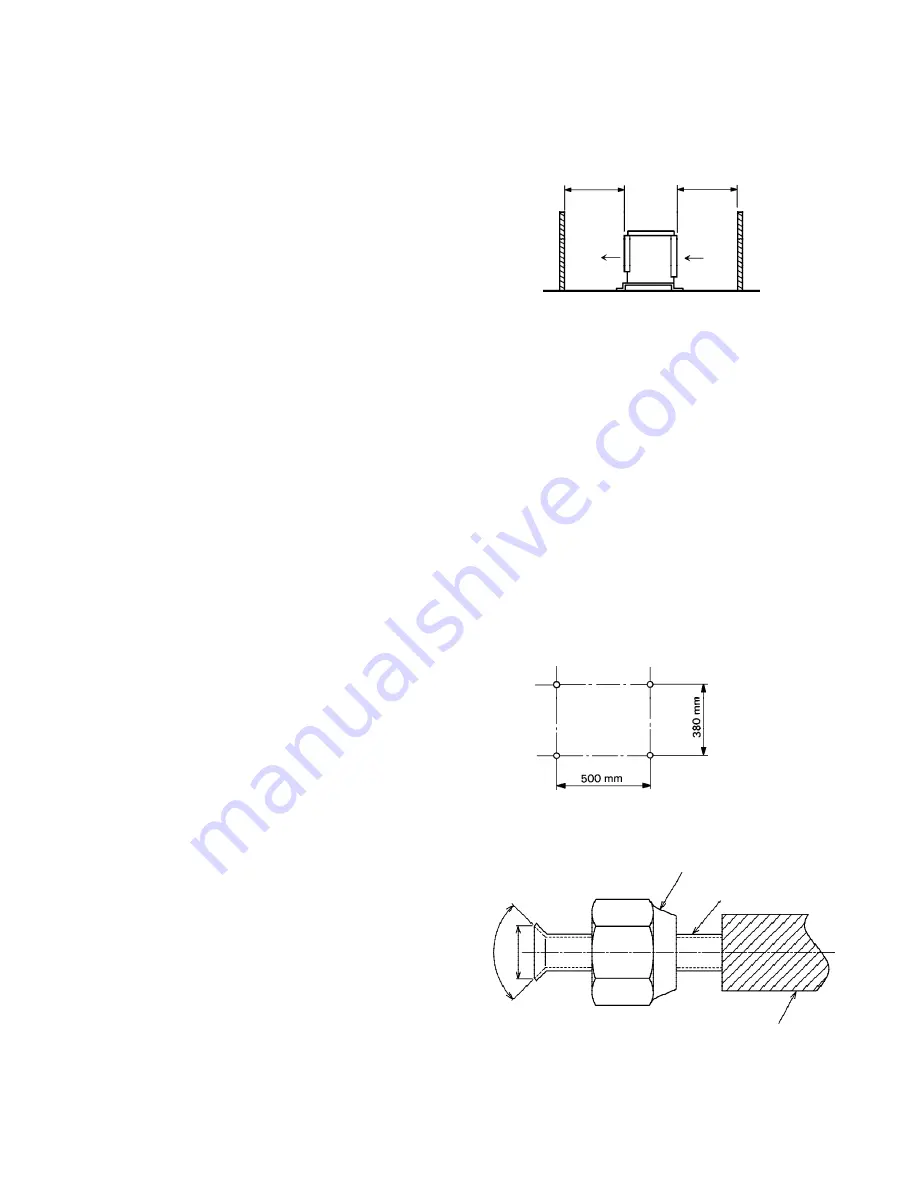
32
32
E1CG4880210
E1CG4880210
Fig. 16
Fig. 16
Min. 60 cm clearance
Min. 60 cm clearance
Air
Air
Air
Air
Fig. 17
Fig. 17
Fig. 18
Fig. 18
Flare Nut
Flare Nut
Copper Tube
Copper Tube
Pipe Insulation
Pipe Insulation
90°±0.5
13.2-14 DIA
[b] LOCATION
[b] LOCATION
The Condenser is intended for outdoor use and must be positioned in a permanent well
The Condenser is intended for outdoor use and must be positioned in a permanent well
ventilated site under the following guidelines:
ventilated site under the following guidelines:
* Select a firm and flat site.
* Select a firm and flat site.
* Should not be exposed to harsh or adverse
* Should not be exposed to harsh or adverse
weather conditions.
weather conditions.
* Preferably a dry and well ventilated area with 60
* Preferably a dry and well ventilated area with 60
cm clearance on both front and rear for ease of
cm clearance on both front and rear for ease of
maintenance and service should they be required.
maintenance and service should they be required.
* Normal condenser ambient temperature: +1°C to +40°C. Temperatures not within this
* Normal condenser ambient temperature: +1°C to +40°C. Temperatures not within this
operating range may affect the production capacity of the icemaker.
operating range may affect the production capacity of the icemaker.
* When the Condenser Unit is installed on a roof, a 50 cm height base is recommended to
* When the Condenser Unit is installed on a roof, a 50 cm height base is recommended to
prevent heat reflection and to avoid the possibility of the unit standing in water.
prevent heat reflection and to avoid the possibility of the unit standing in water.
* The maximum line length is 10 m. For information on longer line installations, call Hoshizaki
* The maximum line length is 10 m. For information on longer line installations, call Hoshizaki
Care +44 (0) 1223242254.
Care +44 (0) 1223242254.
* The Condenser should not be installed more than 6 m above the height of the icemaker or
* The Condenser should not be installed more than 6 m above the height of the icemaker or
more than 2 m below it.
more than 2 m below it.
Note:
Note: If the recommended guidelines of the installation are exceeded, the icemaker
If the recommended guidelines of the installation are exceeded, the icemaker
performance may be reduced.
performance may be reduced.
[c] INSTALLATION
[c] INSTALLATION
1) This Condenser Unit is provided with four
1) This Condenser Unit is provided with four
mounting holes. Secure the Condenser Unit
mounting holes. Secure the Condenser Unit
with four bolts. See Fig. 17.
with four bolts. See Fig. 17.
2) Remove the Flare Nut from each of the Access
2) Remove the Flare Nut from each of the Access
Valves on the icemaker and Condenser Unit.
Valves on the icemaker and Condenser Unit.
Note:
Note: Remove and discard the Copper Caps on
Remove and discard the Copper Caps on
the Flare Nuts.
the Flare Nuts.
3) The two copper tubes (9.52 mm OD) to be
3) The two copper tubes (9.52 mm OD) to be
provided at site should be insulated
provided at site should be insulated
separately. Place the Flare Nuts onto each
separately. Place the Flare Nuts onto each
end of the tubes and flare the tube ends.
end of the tubes and flare the tube ends.
Summary of Contents for IM-240AME
Page 6: ...2 2 E1CG4880210 E1CG4880210 b IM 240DWME Water cooled b IM 240DWME Water cooled ...
Page 7: ...3 3 E1CG4880210 E1CG4880210 c IM 240DSME Remote Air cooled c IM 240DSME Remote Air cooled ...
Page 8: ...4 4 E1CG4880210 E1CG4880210 d IM 240XME Air cooled d IM 240XME Air cooled ...
Page 9: ...5 5 E1CG4880210 E1CG4880210 e IM 240XWME Water cooled e IM 240XWME Water cooled ...
Page 10: ...6 6 E1CG4880210 E1CG4880210 f IM 240XSME Remote Air cooled f IM 240XSME Remote Air cooled ...
Page 11: ...7 7 E1CG4880210 E1CG4880210 g IM 240AME Air cooled g IM 240AME Air cooled ...
Page 62: ...58 58 E1CG4880210 E1CG4880210 b IM 240DWME IM 240XWME b IM 240DWME IM 240XWME ...
Page 63: ...59 59 E1CG4880210 E1CG4880210 c IM 240DSME IM 240XSME c IM 240DSME IM 240XSME ...
Page 64: ...60 60 E1CG4880210 E1CG4880210 d IM 240AME d IM 240AME ...