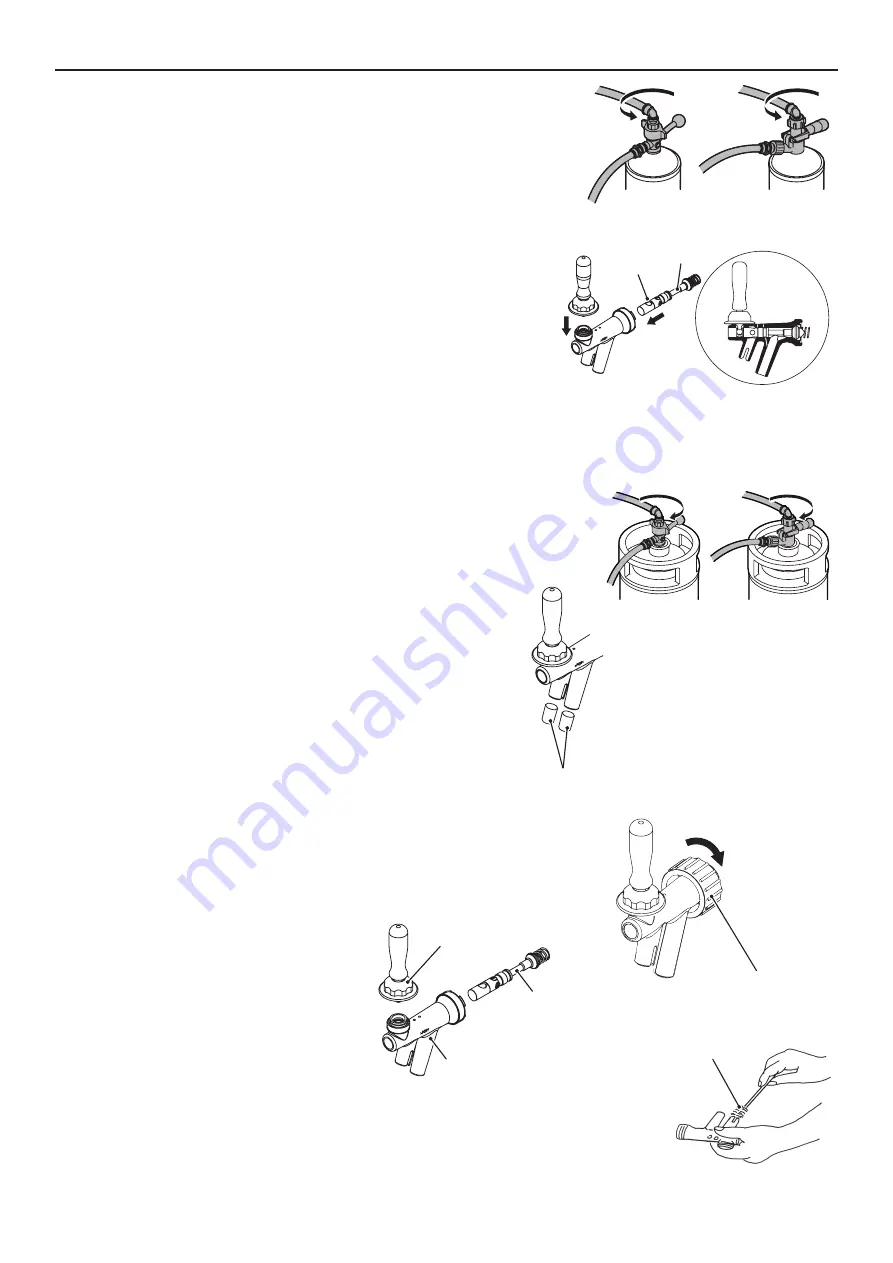
24
ENGLISH
21) Turn the keg coupler counterclockwise to remove it from the cleaning tank.
22) Thoroughly wash and dry the cleaning sponge and store it for later use.
23) Repeat the above steps 9) to 22) until clear water comes out of the beer tap.
Note: Receive the water in a mug or glass to check its clearness. Repeat a few
times until water becomes clear.
24) Turn the union nut clockwise to remove the beer tap.
25) Loosen the cap nut to disassemble the beer tap. Fit the valve shaft in the
original (normal) direction while aligning the holes in the beer tap and valve
shaft (larger hole facing up), and tighten the cap nut.
Note: Assemble the beer tap correctly, or beer cannot be dispensed
properly.
26) Attach the beer tap on the unit by turning the union nut counterclockwise.
27) Wash the cleaning tank interior thoroughly, turn the tank upside down to dry, and cap it tightly for storage.
28) Hold the bottom of the operation panel unit and pull the front handle toward you to unlock. Pull down the operation panel unit
until it stops to cover up the beer tap lever.
Note: To prevent malfunction, do not pull down the operation panel unit with the beer
tap removed.
29) Turn the keg coupler clockwise to attach it to the beer keg.
Note: Wash the joint between the keg coupler and beer keg if it is not clean.
30) Wipe off moisture from the end of the beer tap nozzles. Clean and attach
the nozzle caps (accessory).
Note: Always attach the accessory nozzle caps at the end of dispensing
operation or during periods of non-use to prevent entrance of
insects or dirt into the beer tap nozzles.
6. DISASSEMBLY AND CLEANING OF BEER TAP (WEEKLY)
1) Follow the steps 1) to 7) of “2. BEER CIRCUIT”.
2) Lift up the operation panel unit slowly until it clicks and locks into place.
3) Turn the union nut clockwise to remove the beer tap.
4) Loosen the cap nut to disassemble the beer tap.
5) Use a neutral dishwashing detergent and the accessory brush to clean inside the beer tap and
valve shaft.
Valve Shaft
Hole
1
2
Rotary Type
Vertical Type
Nozzle Cap
Union Nut
Loosen
Cap Nut
Valve Shaft
Nozzle
Rotary Type
Vertical Type
Brush